ABB 751010R0815 Power supply unit
What this chapter contains
This chapter contains the instructions that you must follow when selecting the motor,
cables, protections, cable routing and way of operation for the drive system.
Note: The installation must always be designed and made according to applicable
local laws and regulations. ABB does not assume any liability whatsoever for any
installation which breaches the local laws and/or other regulations. Furthermore, if
the recommendations given by ABB are not followed, the drive may experience
problems that the warranty does not cover.
Motor selection and compatibility
1. Select the motor according to the rating tables in chapter Technical data. Use the
DriveSize PC tool if the default load cycles are not applicable.
2. Check that the motor ratings lie within the allowed ranges of the drive control
program:
• motor nominal voltage is 1/2 ... 2 · UN of the drive
• motor nominal current is 1/6 ... 2 · I2hd of the drive in DTC control and
0 ... 2 · I2hd in scalar control. The control mode is selected by a drive parameter
3. Check that the motor voltage rating meets the application requirements:
See note 7 below the Requirements table, page 42.
4. Consult the motor manufacturer before using a motor in a drive system where the
motor nominal voltage differs from the AC power source voltage.
5. Ensure that the motor insulation system withstands the maximum peak voltage in
the motor terminals. See the Requirements table below for the required motor
insulation system and drive filtering.
Example 1: When the supply voltage is 440 V and a drive with a diode supply is
operating in motor mode only, the maximum peak voltage in the motor terminals
can be approximated as follows: 440 V · 1.35 · 2 = 1190 V. Check that the motor
insulation system withstands this voltage.
Resistor braking Motor voltage rating
no resistor braking is in use UN
frequent or long term brake cycles will be used UACeq1
UN = rated input voltage of the drive
UACeq1 = UDC/1.35
UACeq1 = the equivalent AC power source voltage of the drive in V AC.
UDC = the maximum DC link voltage of the drive in V DC.
For resistor braking: UDC= 1.21 × nominal DC link voltage.
Note: Nominal DC link voltage is UN × 1.35 in V DC.
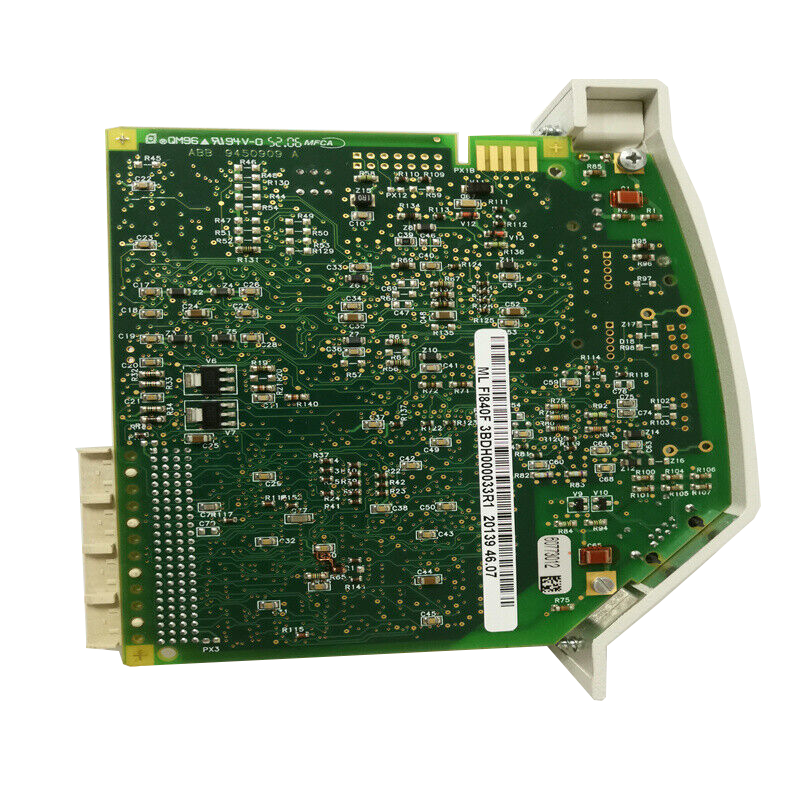
Protecting the motor insulation and bearings
The output of the drive comprises – regardless of output frequency – pulses of
approximately 1.35 times the equivalent mains network voltage with a very short rise
time. This is the case with all drives employing modern IGBT inverter technology.
The voltage of the pulses can be almost double at the motor terminals, depending on
the attenuation and reflection properties of the motor cable and the terminals. This in
turn can cause additional stress on the motor and motor cable insulation.
Modern variable speed drives with their fast rising voltage pulses and high switching
frequencies can generate current pulses that flow through the motor bearings, which
can gradually erode the bearing races and rolling elements.
The stress on motor insulation can be avoided by using optional ABB du/dt filters.
du/dt filters also reduce bearing currents.
To avoid damage to motor bearings, the cables must be selected and installed
according to the instructions given in the hardware manual. In addition, insulated N end (non-driven end) bearings and output filters from ABB must be used according
to the following table. Two types of filters are used individually or in combinations:
• optional du/dt filter (protects motor insulation system and reduces bearing currents).
• common mode filter (mainly reduces bearing currents).
Requirements table
The following table shows how to select the motor insulation system and when an
optional ABB du/dt filter, insulated N-end (non-driven end) motor bearings and ABB
common mode filters are required. Ignoring the requirements or improper installation
may shorten motor life or damage the motor bearings and voids the warranty.
Motor type Nominal mains
voltage (AC line
voltage)
Requirement for
Motor insulation
system
ABB du/dt filter, insulated N-end bearing and ABB common mode
filter
PN < 100 kW
and
frame size < IEC 315
100 kW < PN < 350 kW
or
frame size > IEC 315
PN > 350 kW
or
frame size > IEC 400
PN < 134 hp
and
frame size <
NEMA 500
134 hp < PN < 469 hp
or
frame size >
NEMA 500
PN > 469 hp
or
frame size >
NEMA 580
A
B
B
Random wound M2_,
M3_ and
M4_
UN < 500 V Standard - + N + N + CMF
500 V < UN < 600 V Standard + du/dt + du/dt + N + du/dt + N + CMF
or
Reinforced - + N + N + CMF
600 V < UN < 690 V
(cable length <
150 m)
Reinforced + du/dt + du/dt + N + du/dt + N + CMF
600 V < UN < 690 V
(cable length >
150 m)
Reinforced - + N + N + CMF
Form-wound
HX_ and
AM_
380 V < UN < 690 V Standard n.a. + N + CMF PN < 500 kW: + N +
CMF
PN > 500 kW: + N +
CMF + du/dt
Old* form wound HX_
and modular
380 V < UN < 690 V Check with the motor
manufacturer.
+ du/dt with voltages over 500 V + N + CMF
Random wound HX_
and AM_ **
0 V < UN < 500 V Enamelled wire with
fibre glass taping
+ N + CMF
500 V < UN < 690 V + du/dt + N + CMF
HDP Consult the motor manufacturer.