GE 8711-CA-NS Node services carrier, screw terminal LAN
Mixing safe and standard
Standard IO Modules can be mounted on
SafetyNet Nodes - together with SafetyNet
IO Modules - without affecting the node's
functional safety performance. Only
standard applications can read data from
standard Modules, but both standard and
SafetyNet applications are allowed to write
to standard modules. This flexibility can
simplify hardware design, where the
physical constraints of the particular locality
demand such an approach.
Serial interfaces
The Open approach extends to Modbus
serial interface products - which can be
connected to any node (SafetyNet or
standard) by an RS485 connection.
As with data from standard IO Modules, this
data can be read by standard Controllers,
but not by SafetyNet Controllers. Both
standard and SafetyNet Controllers can
write to such devices.
Comprehensive
programming tools
The SafetyNet System is programmed using
the Workbench software package - in
common with the MOST Process Control
Products. In addition to providing the
options of programming the required safety
function in one of three IEC 61131-3
languages (Ladder Diagram, Function Block
Diagram and Structured Text) the package
also provides many useful tools to assist in
testing and commissioning.
Restricted access
Access to modify safety-related parameters
within the configuration and application
program must be restricted to authorised
personnel. The SafetyNet system provides a
number of layers and methods of providing
this protection. Only users with "Safety
Responsibility" can access the safety-related
aspects of the Workbench. Only computers
that the SafetyNet Controller identifies as
"trusted hosts" can download new
parameters. A download can only take
place when an "over-ride key-switch" is set to
the required position. And, if required, each
SafetyNet Controller can be protected by its
own password - without which access to the
safety parameters is denied.
Maintaining field instruments
Maintenance over-rides can be
implemented from operator workstations in
full compliance with the guidelines from
TUV. Users define - as part of the safety
application - the actions to be taken to
maintain a particular instrument and the
SafetyNet System then implements these
pre-defined actions.
HART capability
The SafetyNet System allows full access to
HART field devices for Emerson's AMS
maintenance software. (The first release of
SafetyNet will not have full HART capability,
contact MTL for further information).
Earth leakage detection
Earth leakage fault detection may be
implemented using the 8751-CA-NS
Controller Carrier in conjunction with an
input channel from an 8811-IO-DC Discrete
I/O Module. If ELFD is not required,
SafetyNet Controllers can be mounted on
8750-CA-NS Controller Carriers.
On-line changes
Where allowed by local practices - and
following adequate testing and approval -
new safety programs and configuration can
be downloaded on-line and in real time. In
some situations, this may be possible
without interrupting the operation of the
safety function
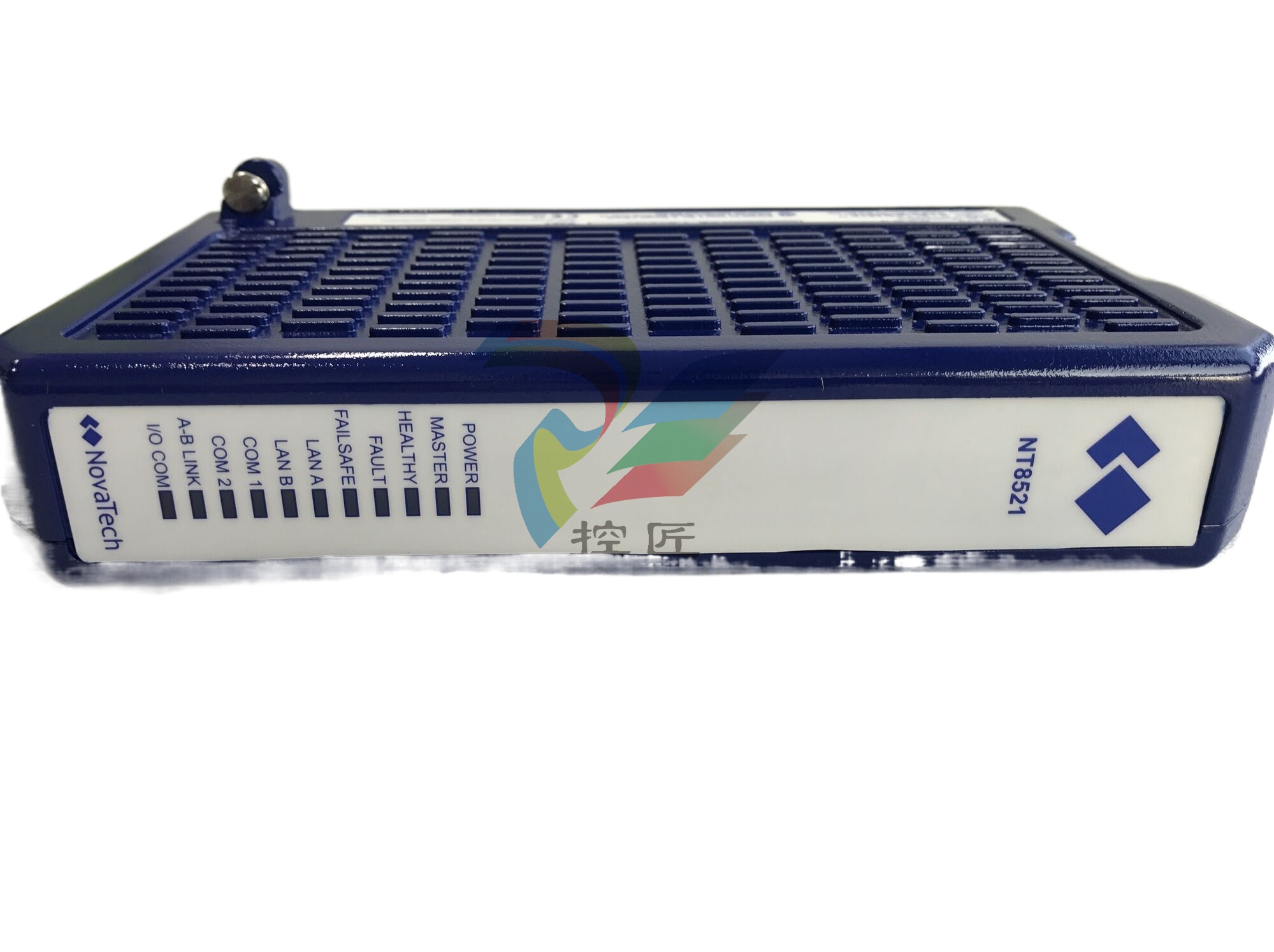
SafetyNet Controller - Runs the safety
application program and carries out
diagnostic checks to ensure it is operating
correctly. If a fault is detected, it will shut
itself down.
SafetyNet Module configured for digital
outputs. Obeys commands sent by the
Controller to set outputs. Internal
diagnostics check that the module is
working correctly. If a fault is detected, the
Module will set outputs to their safe state
of de-energised.
SafetyNet Analog Input Module monitors
the inputs and carries out internal
diagnostics to check that the module is
operating correctly.
SafetyNet Module configured for digital
inputs. Monitors the inputs and also
checks for line faults. Internal diagnostics
check that the module is operating
correctly
Harsh and hazardous
environments
The SafetyNet System is as rugged as the
other MOST Process Control Components:
-40ºC to +70ºC operating ambient
temperature; Zone 2 or Class 1 Division 2
hazardous area mounting; G3 corrosion
resistance; and enhanced shock and
vibration capability. The system will operate
in the most extreme environments found in
process industries, allowing remote
mounting and a truly distributed architecture
in even the most demanding situations.
Event Logging and Sequence
of Events Recording
The SafetyNet System has the same Event
Logging and Sequence of Events (SOE)
recording capability as the MOST Process
Control System. Data received from SafetyNet
Modules is time-stamped by the SafetyNet
Controller with a resolution of better than
200ms (this is dependent on the execution
cycle - small nodes will deliver better
resolution). Data from dedicated (non-SIL)
SOE modules is time-stamped with a
resolution of less than 0.25ms between
different channels of the same SOE module
and less than 1ms between channels from
different SOE modules. The SafetyNet
Controller can record up to 8000 events
before its event data buffer begins to be overwritten by new data.
Reduced cabling and
termination costs
In common with the MOST Process Control
Components, the SafetyNet System offers
users the opportunity to significantly reduce
their spending on wiring and termination
costs. Moving control and safety hardware
out of the control room and on to the plant
gives significant savings. The Field Terminal
design allows users to avoid unnecessary
spend on marshalling cabinets, cross wiring
and marshalling terminals. Integral tagging
and fusing further simplifies cabinet design
and installation.