GE 8725-CA-RB Railbus isolator carrier with PFM
The SafetyNet Controller has a number of LED’s that indicate thestatus and mode of operation of the Controller. The table below
explains what they refer to and describes their operation:
SafetyNet Controller - Specification
SIL 2 Certified Controller 8851- LC-MT
LED name
Power
Master
Healthy
Fault
Failsafe
LAN A
LAN B
COM 1
COM 2
Safe Mode
I/O COM
Colour On Off Flashing
Green 12V power supply to the
Controller is ON.
The internal communication link
(Railbus) between Controller and
IO Modules is working correctly.
The internal communication link
(Railbus) between Controller
and IO Modules is not in use.
The internal communication link
(Railbus) between Controller and
IO Modules is in fault.
In SAFE mode. In CONFIGURATION mode.
(Master) Running the application
program. (Standby) Capable of
running the application program.
If FAILSAFE LED is also ON - has
performed controlled shutdown.
If HEALTH LED is also Flashing - has
requested a “refresh” of parameters.
For all other Controller states.
The Controller is running the
application program.
The Controller is initialising after
a power cycle.
No IO Module scanning is
taking place and the application
program is not running.
IO data is not current - cannot
take control.
(Master) Reading IO data on
start-up. (Standby) Copying
configuration and control
parameters from the Master.
The Controller is the Master in a
redundant pair or is in simplex mode.
If HEALTH LED is also ON - is in
Failsafe. If HEALTH LED is OFF - is
offline.
12V power supply to the
Controller is OFF.
The Controller is the Standby in
a redundant pair.
Yellow
Yellow
Red
Red
Yellow LED is ON when a packet of data is being transmitted.
LED is ON when a packet of data is being transmitted.
LED is latched ON for 2 seconds after a valid packet of data is received.
LED is latched ON for 2 seconds after a valid packet of data is received
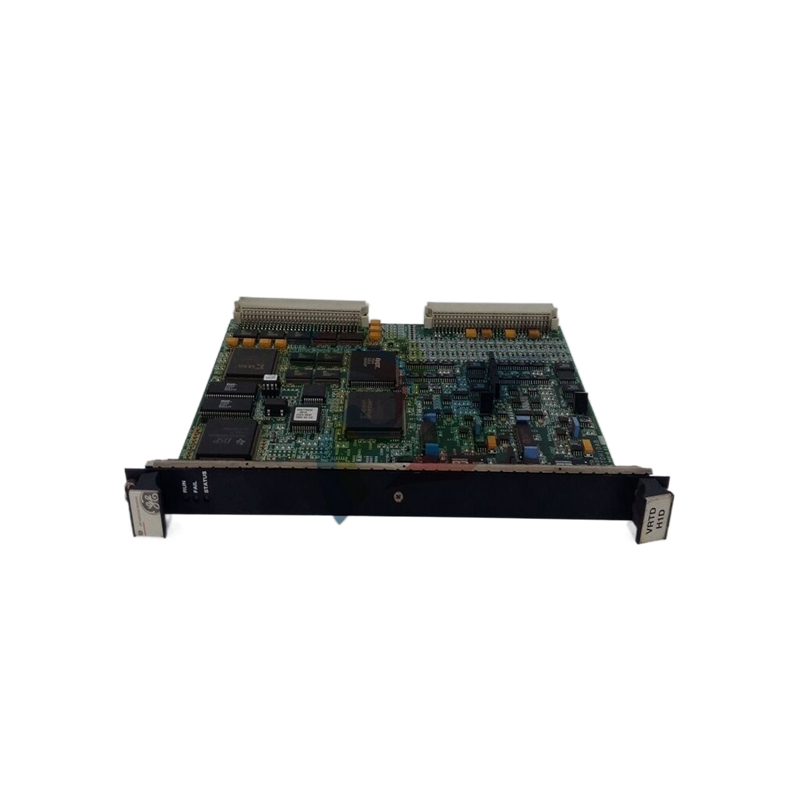
MOST Workbench
The MOST Workbench is the engineering
and documentation tool for the MOST
Process Control and SafetyNet Systems.
The Workbench is used to perform the
following tasks:
♦ Configure IO Channel and
Module parameters
♦ Configure Controller and
network parameters
♦ Input and manage the IO tag
database
♦ Engineer and document the
control or safety application
♦ Generate wizards to simplify
HMI design
♦ Simulate and test control and
safety applications
♦ Generate reports to assist in
Factory and Site Acceptance
Testing
SafetyNet Workbench
The SafetyNet Workbench (8841-LC-MT) has
all the features of the standard Workbench,
but additionally includes the special tools
required for safety applications.
Safety programming
languages
The Workbench provides three IEC61131
programming languages that can be used to
write safety-related application programs:
♦ Ladder logic (LD)
♦ Function Block Diagram (FBD)
♦ Structured Text (ST)
Configuration Mode and
Safety Responsibility
Changes to safety-related parameters are
carried out with the SafetyNet Controller in
“Configuration Mode”. Access to this mode is
restricted to personnel with “Safety
Responsibility” and its use is constrained by a
number of further layers of protection for
downloading parameters to SafetyNet
Controllers. The SafetyNet system defines 6
password protected levels of access authority
– with only the 3 highest levels being granted
“Safety Responsibility”.
Trusted Hosts
To prevent access to SafetyNet Controllers by
non-approved instances of the Workbench,
remote Modbus devices, asset management
packages and HMI, only those that the
SafetyNet Controller identifies as “Trusted
Hosts” can download new parameters.
Each Trusted Host is recognised by its IP and
MAC addresses (remote Modbus devices are
recognised by the serial port to which they
are connected). For each Trusted Host a
number of other restrictions can be defined:
♦ Modbus write not allowed
♦ Workbench write not allowed
♦ HART pass-through not allowed
Key Switch Protection
When a SafetyNet Controller is added to the
Workbench the user is given the option of
selecting a tag to act as a “Key Switch”. This
can be used by an Operator to lock the
SafetyNet System so that Configuration Mode
cannot be entered without their awareness or
permission.
The Key Switch can be a physical switch,
driven from an HMI screen or it can be an
output from the SafetyNet application.
Controller Passwords
When a SafetyNet Controller is added to the
Workbench the user is given the option to use
a Controller Password. If this option is
selected, it is subsequently impossible to
enter Configuration Mode without the
Controller Password.