ABB CI534V02 3BSE010700R1 interface communication module
A disturbance record can be triggered byeither the leading or lagging edges of all
binary signals or by events generated by the
internal protection algorithms. Up to 10 general-purpose binary inputs may be configured
to enable external signals to trigger a disturbance record. In addition, there is a binary
input in the central and the bay unit for starting
the disturbance recorders of all bay units.
The number of analog channels that can be
recorded, the sampling rate and the recording
period are given in Table 14. A lower sampling
rate enables a longer period to be recorded.
The total recording period can be divided into
a maximum of 15 recording intervals per bay
unit.
Each bay unit can record a maximum of 32
binary signals, 12 of which can be configured
as trigger signals.
The function can be configured to record the
pre-disturbance and post-disturbance states
of the signals.
The user can also determine whether the recorded data is retained or overwritten by the
next disturbance (FIFO = First In, First Out).
This function is performed in a stand-alone
mode in the bay unit (see page 7).
Note:
Stored disturbance data can be transferred via
the central unit to other computer systems for
evaluation by programs such as PSM505 [3].
Files are transferred in the COMTRADE format.
After retrieving the disturbance recorder data,
it is possible to display them graphically with
PSM505 directly.
Communication interface
Where the busbar protection has to communicate with a station automation system (SAS),
a communication module is added to the central unit. The module supports the interbay
bus protocols IEC 61850-8-1, IEC 60870-5-
103 and LON.
The IEC 61850-8-1 interbay bus transfers via
either optical or electrical connection:
• differential current of each protection zone
• monitoring information from REB500 central unit and bay units
• binary events (signals, trips and diagnostic)
• trip reset command
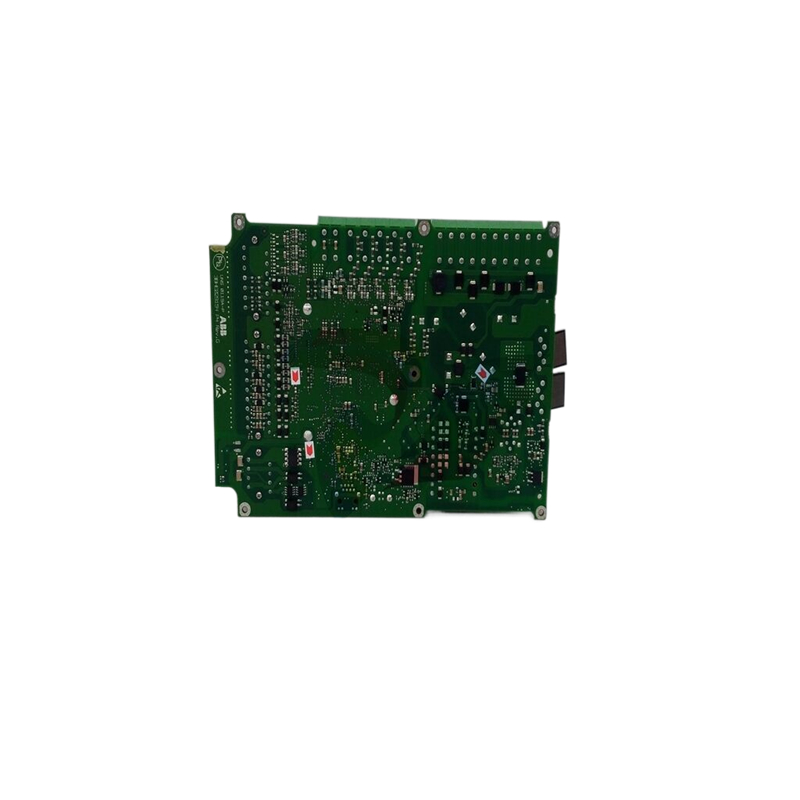
• disturbance recording data (via MMS file
transfer protocol)
• time synchronization with Simple Network
Time Protocol (SNTP)
• two independent time servers are sup ported. Server 2 as backup time
The LON interbay bus transfers via optical
connection:
• differential currents of each protection zone
• binary events (signals, trips and diagnostic)
• trip reset command
• disturbance recording data (via HMI500)
• time synchronization
The IEC 60870-5-103 interbay bus transfers
via either optical or electrical connection:
• time synchronization
• selected events listed in the public part
• all binary events assigned to a private part
• all binary events in the generic part
• trip reset command
Test generator
The HMI program (HMI500) which runs on a
PC connected to either a bay unit or the cen tral processing unit includes a test generator.
During commissioning and system mainte nance, the test generator function enables the
user to:
• activate binary input and output signals
• monitor system response.
• test the trip circuit up to and including the
circuit-breaker
• test the reclosure cycles
• establish and perform test sequences with
virtual currents and voltages for the bay
protection of the REB500sys
The test sequencer enables easy testing of
the bay protection without the need to decom mission the busbar protection. Up to seven
se-quences per test stage can be started. The
sequences can be saved and reactivated for
future tests.
Isolator supervision
The isolator replica is a software feature with out any mechanical switching elements. The
software replica logic determines dynamically
the boundaries of the protected busbar zones