ABB D-20-0-1102 Flame Power Unit
PROFOBUS DP: the bus for the Decentralized PeripheryThe PROFIBUS DP (RS485) is responsible for communication between the
Controller level of a process automation system and the decentralized periphery in
the field, also intrinsic safety (RS485-IS) via DP-Ex barriers into hazardous area.
One feature of PROFIBUS DP is its scalable high speed of transmission up to
12 Mbit/s.
PROFIBUS PA: extension for Process Automation
This PROFIBUS variant was developed for the process industry. PROFIBUS PA
interacts with a fix transmission rate of 31,25 kbit/s and is designed for connection
of bus-powered 2-wire field devices such as transmitters and actuators.
It correspond to IEC Standard 61158-2 and can be also applied to intrinsically safe
installations (EEx i) in Zone 1 / Div.1.
Linking Devices are used to integrate PA bus lines into the PROFIBUS DP network.
This ensures that all information is available in a continuously connected network
through the complete PROFIBUS system (DP and PA).
PROFIBUS Technology Terms
ISO/OSI Reference Model
In accordance with the international ISO/OSI model, a fieldbus protocol can be
uniquely described by means of up to 7 transmission levels. Specific tasks are
assigned to each level in this system. PROFIBUS DP and PROFIBUS PA use only
the first two levels as well as the user interface, which resides in level 7 and where
application functions that can be utilized by the user are determined along with
system and device behavior. Level 1 defines the physical aspect of transmission
(physical layer). This includes, for example, the method of transmission, the
transmission medium, and lengths of lines, while level 2 specifies the bus access
protocol (data link layer).
Bus Access Control
The bus access control (MAC, Medium Access Control) is a specific procedure that
determines at which point in time a PROFIBUS device can send data. While active
devices (master) can start the exchange of information, passive devices (slaves) may
only begin communication when prompted by an active device. A distinction is
made between a controlled, deterministic access procedure with real-time
capabilities (master-slave with PROFIBUS) and a random, non-deterministic access
procedure (CSMA/CD with Ethernet)
Addressing
Each device, connected to a PROFIBUS network, needs an unique address for
selectively identify a field device. For this purpose, PROFIBUS device addresses are
assigned either by an address switch (hard addresses) or by parameter assignment
during commissioning (soft addresses).
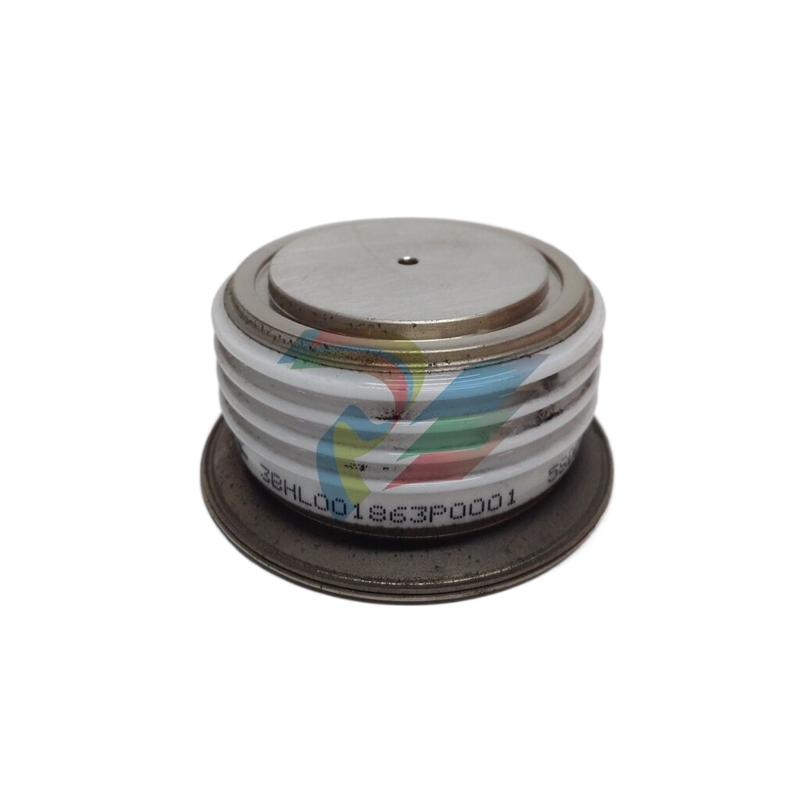
A 7-bit device address serves to identify the bus participants in the network. The
addresses range from 0 to 127, and the following are reserved:
• Address 126: default for automatic address assignment via the master;
• Address 127: sending broadcast telegrams.
If the address 0 is used for the class-1 master, the addresses 1 to 125 are available for
addressing the field devices. Therefore up to 126 DP or PA field devices (master and
slaves) can be addressed. Each address can only be used once in a single
PROFIBUS network.
Communication Protocols
At the protocol level, PROFIBUS offers a broad spectrum of options, which enables
optimum communication between different applications. PROFIBUS DP is a fast
and deterministic process data exchange between a PROFIBUS master and the
assigned slave devices.
Presently the basic and extended functions supported with AC 800M/CI854(A) are:
• Basic function (V0):
– Cyclic data transfer
– Diagnostic
– Configuration via GSD files
• Extended function V1:
– Acyclic data transfer
– Alarm handling (planned, but not supported yet)
– FDT/DTM device management
– Function blocks acc. IEC 61131-3