ABB DSBB110A 57330001-Y shielding plate
RLM 01 converts one simple, non-redundant Profibus line into two reciprocally
redundant lines A/B. The module works bidirectionally, which means that all three
interfaces can receive and transmit data.
You can position the module directly after a master, before a bus segment with
several slaves or before an individual slave. PROFIBUS stations with redundant
couplers [K] can be directly connected to the PROFIBUS set redundant by RLM 01.
Stations with only one interface can be optionally assigned to the A or B line. Each
RLM 01 PROFIBUS interface can serve up to 31 PROFIBUS stations. Using
repeaters [R] and media converters [O/E] makes it possible to increase the length of
the PROFIBUS lines and the number of stations.
• Conversion: Line M <=> Lines A/B
• Use on PROFIBUS DP/FMS lines
• Automatic line selection
• Transmission rate 9.6 kBit/s .... 12
MBit/s
• Monitoring of communication
• Repeater functionality
• Redundant power supply
• Status and error display
• Monitoring of the power supply
• Potential-free alarm contact
• Simple assembly on DIN mounting
rail
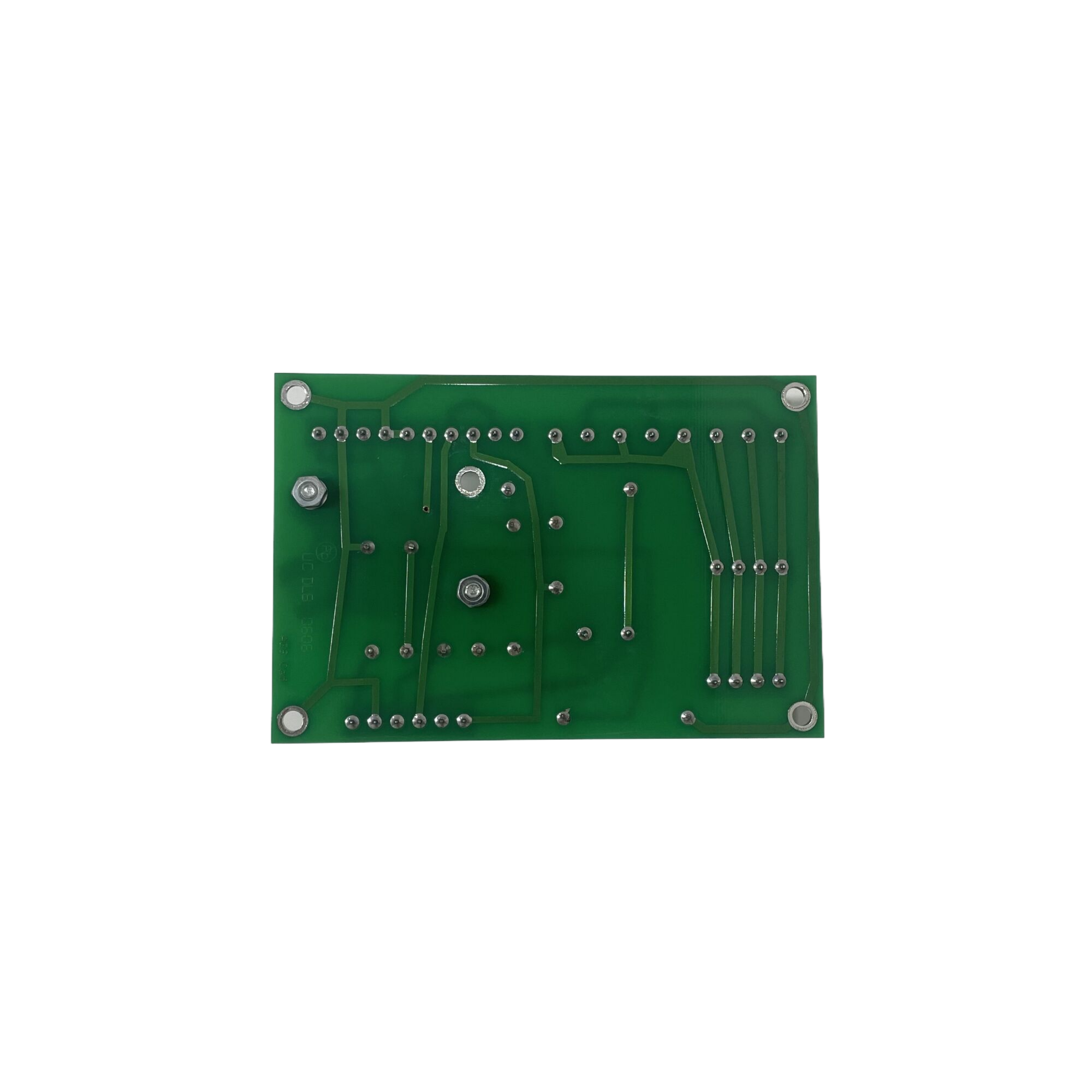
RLM01 does not support master redundancy where one master only runs line A
and the other one only line B. The bus communication is asynchronous, even if
both masters balance their program modules against each other on the
applicational level. A Melody central unit CMC 60/70 offers clock synchronous
communication because of redundant PROFIBUS terminals (A & B).
Network devices like repeater, FOC coupler,DP/PA converter as well asRLM01
cause aN x bit time delay of data telegrams. The delay time (see technical data) is
device specific and depends upon the selected baud rate
The three RS 485 interfaces of the module support all transmission rates specified in
DIN 19245 for the PROFIBUS from 9.6 kBit/s to 12 MBit/s. The module has
repeater functionality, i.e., it regenerates the signal shape and the amplitude of
received data. RLM 01 monitors all three lines A, B and M for activity and error
states. Detected errors are signalled by lit diodes on the front panel. The potential free alarm contact activated in parallel to this can be polled for diagnostic purposes
by the process control system PCS or by a programmable logic control PLC. The
three serial RS 485 interfaces are potential-free relative to each other and to the
power supply. This is a functional electrical isolation.
The first data coming in over line A or line B with a correct telegram start are routed
to terminal M. With simultaneity, either line A or line B is selected at random.
Testing and selection is always based on the first character. In the case of a telegram
start with error on A, the control logic switches to the redundant line B. The same
procedure applies vice-versa for line B.
Data coming in over line M with a correct telegram start are routed in parallel to the
two terminals A and B. The test for data is always based on the first character. In the
case of a telegram start with error, the control logic does not output any data to A
and B.
Either a single or a redundant power supply with 24 VDC is possible. The
distribution of load across L1+ and L2+ is based on the level of the voltages applied.
If a voltage source fails, the switch to the redundant supply source is made without
interruption. A monitoring logic circuit tests whether both voltages are present.