GE MVME5500 VMEbus Single Board Computer
WARNING – Bodily injury. These symbols, and the signal word "WARNING", indicate apotentially dangerous situation. Failure to observe this safety information could result in death
or severe injury. The text may state the hazard, how to avoid the hazard, and the result if not
followed. The bolt is for electrical warnings; the exclamation point is for general warnings.
WARNING, HOT SURFACE – Bodily injury. This symbol indicates a potentially hot
surface. Avoid contact with a hot surface.
NOTICE – Equipment damage or loss of data or cybersecurity risk. This symbol
indicates a potential for equipment damage, loss of data or another unintended outcome.
Failure to observe this information may result in damage to or destruction of the product
and / or other system components.
IMPORTANT NOTE: This symbol indicates operator tips, particularly useful information, or
important information about the product or its further uses.
Potential safety hazards
Before beginning installation, repair, or maintenance on the analyzer, read the safety information
below and contact the local Safety Department to ensure that all safety guidelines, regulations, and
procedures are followed. This includes obtaining the proper work permits.
The user is responsible for being familiar and complying with all safety and health guidelines,
regulations, and procedures at the analyzer location. Consult Material Safety Data Sheets for safety
requirements.
Become familiar with the application specifications before working on the analyzer.
DANGER – Serious damage to health / risk to life. When working on the analyzer,
there is the possibility of exposure to hydrogen, nitrogen, and other compressed gases. All
appropriate precautions and extreme care should be taken when working with compressed
gases.
DANGER – Serious damage to health / risk to life. Before opening analyzer enclosure
doors, be sure the area is safe from hazardous gases and will remain so the entire time the
analyzer is open.
Ensure there is no hazardous atmosphere present when performing maintenance on the
unit. Do not separate components when energized. This applies to all connectors and
connections, cabling and wiring.
WARNING – Bodily injury. Wear protective clothing and equipment, such as rubber gloves
and goggles or safety glasses with side shields.
WARNING – Bodily injury. Apply power only after the procedures are complete. Technicians
must perform the procedures in order: plan, install, wire, verify the power-on sequence, and
configure.
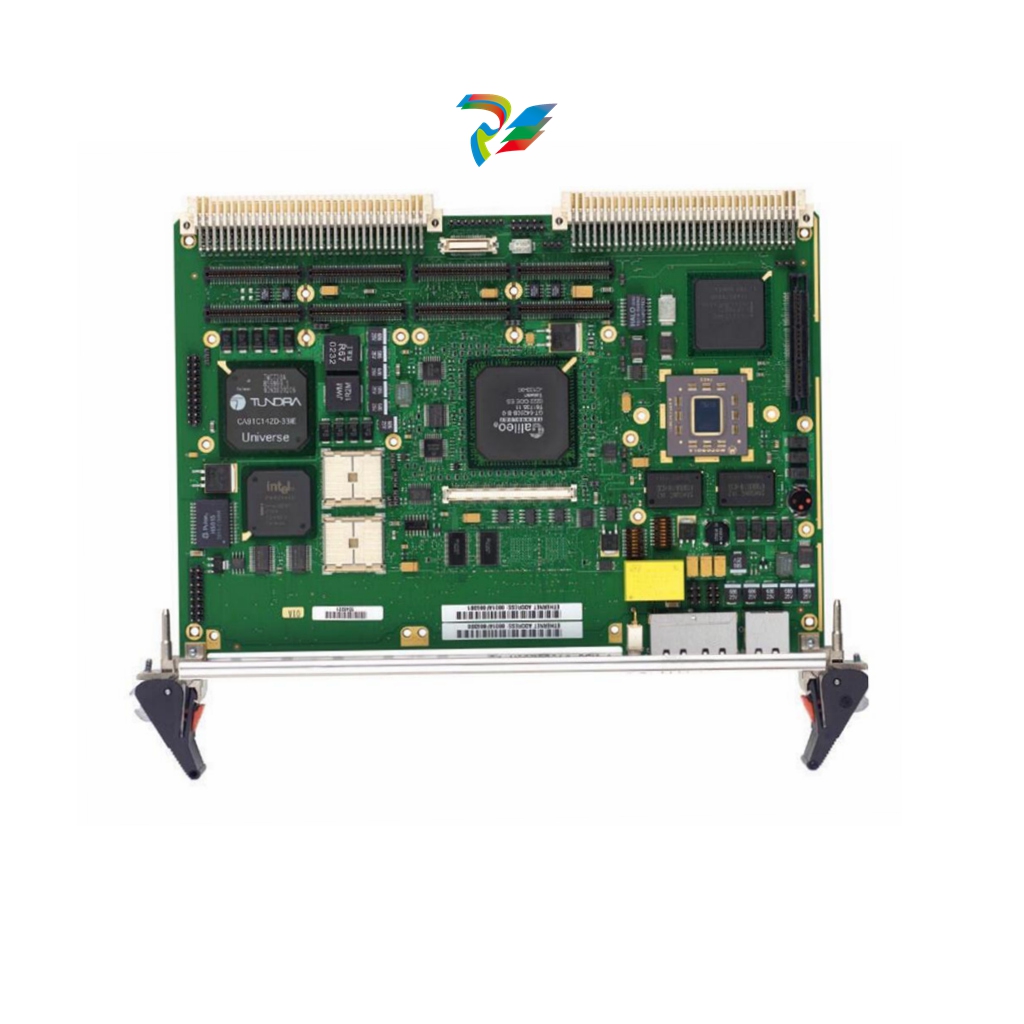
WARNING – Bodily injury. The device can be operated at high levels of pressure and with
aggressive media. Serious injury and/or considerable material damage can be caused if this
device is handled incorrectly.
NOTICE – Equipment damage or loss of data. When handling electronic parts and
assemblies, it is necessary that proper electrostatic discharge (ESD) precautions be taken
Wear an ESD wrist strap with a grounding cable and use an ESD shielded bag to protect
items removed. Clean only with a damp cloth.
1 Introduction
The PGC5000 Generation 2 Process Gas Chromatograph analyzer separates and measures the
individual components of gas or liquid samples. It automatically samples and analyzes process
streams using an appropriate interface to control analytical functions. This interface may be a Local
User Interface (LUI) that utilizes operational software located on the Master Controller, or it may be a
Remote User Interface (RUI) that has the same operational software on a PC. The term “user
interface” in this instruction refers to either the LUI or RUI, whichever applies to the system.
The PGC5000 Generation 2 analyzer is compatible with version 4.2.1 and later of the STAR Data
Management System.
Each analyzer has a temperature code (T-Rating) listed on the nameplate. This T-Rating indicates the
temperature classification of the area in which the analyzer has been designed to operate. T-Ratings
and area classifications for analyzer locations are determined and supplied by the customer.
The standard analyzer consists of a Master Controller and associated ovens. The configuration below
has the Master Controller connected to the ovens through an Ethernet switch.
Figure 1-1: Standard PGC5000 with ovens connected by switch