ABB SNAT-7261-INT module
2.4.6 SampleThe methods used for transporting the sample from the process stream to the analyzer, or from the
calibration sample to the analyzer, are critical to the operation of the analyzer. Refer to the system
drawings in the Data Package for specific system connections.
2.4.7 Hydrogen gas
DANGER – Serious damage to health / risk to life. Hydrogen is highly explosive.
Follow applicable safety precautions and use extreme care in making connections.
The analyzer uses hydrogen gas as a burner fuel with flame cell detectors (FID or FPD) and
sometimes uses it as a carrier gas. Verify that the hydrogen gas meets the criteria of the gas
requirements listed in the Data Package. Also refer to the Data Package for specific connection
information.
2.4.8 Vents
All vent lines must be at atmospheric pressure unless otherwise specified in the Data Package. The
vent lines should slope down from the analyzer so that condensation will not collect in the analyzer or
cause backpressure in the external tubing. Refer to the Data Package for specific connection
information.
2.4.9 Liquid sample valve
The Liquid Sample Valve (LSV) is used only with liquid applications. The Oven Enclosure has sample
lines connected to a mounting plate attached to the LSVs mounting flange.
The LSV has the sample lines connected to the mounting plate attached to the LSVs mounting flange,
as shown in Figure 2-1.
Figure 2-1: Liquid Sample Valve
NOTICE – Equipment damage. Use two wrenches when tightening the sample line
connections at the LSV sample chamber. One wrench must be used to back up the force
applied to tighten the fitting (direct wrench force may bend the stem or damage the valve
seals).
IMPORTANT NOTE: To ensure the integrity of the components within the Liquid Sample Valve, use
the tools in LSV Tool Kit 791K009-1 when assembling of disassembling the LSV.
2.5 Electrical
The analyzer must be installed according to all applicable codes. If it is in a hazardous area, the wiring
method must conform to the applicable requirements.
Install signal wiring and power wiring in separate conduit pipes or cable trays to reduce noise and
crosstalk.
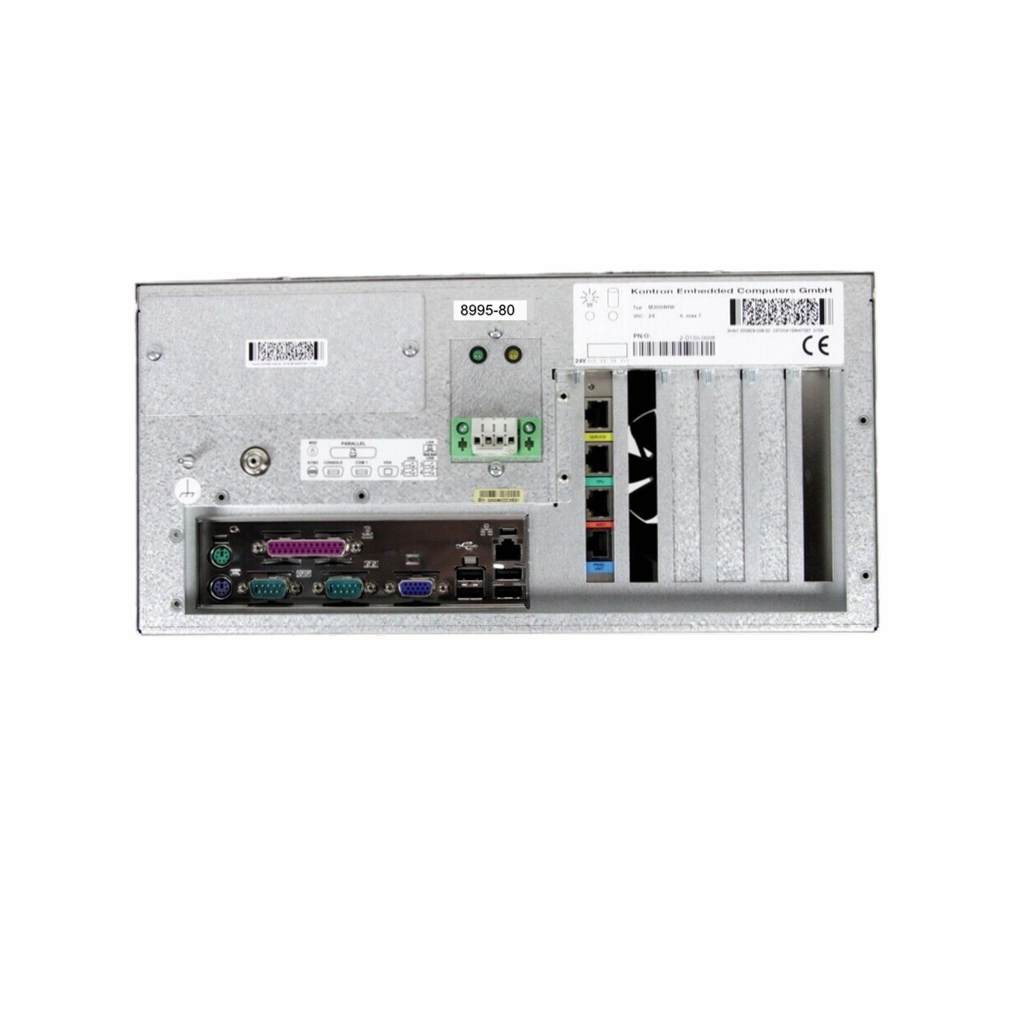
A grounding (earthing) connection is required. Connect minimum 12 gauge (3.31 mm2) ground wire
to the Earthing Connection on the Oven Compartment and on the Master Controller.
WARNING – Bodily injury. The Neutral and Ground (earth) connections to the PGC5000
series Master Controller and B class oven must be at earth (0 volts) potential. Failure to
maintain earth (0 volts) potential at these connections points constitutes a serious safety
hazard.
2.6 Set up the Master Controller
The Master Controller (see Figure 2-2) must be installed according to all applicable codes. If it will be
in a hazardous area, the wiring method must conform to the applicable requirements. General Master
Controller connections include:
Power wiring (circuit breaker protection must be supplied by the customer); refer to the
installation wiring drawing provided in the Data Package for details.
Signal fiber between the Master Controller and the Oven(s).
Alarm contact outputs; refer to the installation drawing in the Data Package for details.
Neutral and Ground (earth) connections must be at earth (0 volts) potential.
WARNING – Bodily injury. Failure to maintain earth (0 volts) potential at Neutral and Ground
connection points constitutes a serious safety hazard. There could be damage to equipment.
Figure 2-2: Inside the Master Controller
Refer to the applicable drawings in your Data Package for specific interconnection wiring information.
2.6.1 Single board computer PCB
The Master Controller and the Oven with Controller contain a Single Board Computer (SBC). The SBC
has built in redundant Ethernet Network Interface Connections (NICs) located at the top center of the
SBC, labeled J6 and J8. Note that Ethernet 1 is to the right and Ethernet 2 is to the left.
The SBC has an SBC CAN Interface Card for each oven, labeled 1 through 4 from left to right. This
module communicates with the oven via fiber optic cables attached to the board by two connectors.
The fiber optic cables utilize two type ST connectors. The customer is required to install all fiber optic
connections.
NOTICE – Equipment damage. Sharp bends in a fiber optic cable can cause signal
attenuation or the optical fiber to break.
The ST connectors have a bayonet mount and a long cylindrical 2.5 mm ceramic or polymer ferrule to
hold the fiber. They are spring-loaded and keyed with slots and alignment nubs. Always “stab and
twist” to make sure the ST connectors seat properly.