ABB SNAT602TAC DCF1001395P0001 Control Unit
1.1 Data PackageAll important documents for the sales order are saved in a folder on a SharePoint site using a custom
shared link. Included in the sales order documents are the drawings, manuals, replacement parts list
and test data needed to support installation and operation of the analyzer(s). This manual refers to
these resources as the “Data Package.”
1.2 Drawings
Since analyzer configuration depends on the application, this manual does not contain generic
engineering drawings and diagrams. Utilize the drawings, diagrams and replacement parts lists
provided in the Data Package for your analyzer to ensure you are using the correct ones for your
system.
1.3 Master controller
The Master Controller can support up to four ovens in any combination of Class B and Class C ovens,
depending on detector configurations. If internal I/O modules are utilized, the maximum number of
ovens per Master Controller is three.
The Master Controller contains a Mounting Plate with a Single Board Computer (SBC) PCB, a Power
Supply, one or more SBC CAN Interface Cards, and optional Wago input/output modules. The front
panel assembly has a touchscreen, liquid crystal display (LCD), keypad, and front panel board.
No Master Controller is required for the Oven with Integrated Controller. The Oven with Integrated
Controller can support up to four ovens in any combination of Class B and Class C Ovens, depending
on detector configurations. The user interface is accessed remotely, as described in Section 3.7.
The PGC5000 Generation 2 Master Controller can also act as a stand-alone RUI. In this configuration,
the Master controller will not be connected to an oven, and it will not contain SBC CAN Interface Cards
or Wago input/output modules. It will be connected to the analyzer network via Ethernet and can
connect to any PGC5000 Generation 2 device that is supported.
1.4 Class B oven
The Class B oven, which comes in liquid and vapor versions, houses an isothermal oven which
contains the analytical columns, detector, detector amplifier, temperature controller, control valves,
and sample valve. The Class B oven has one detector and a maximum of four valves.
1.4.1 Liquid version
The liquid version incorporates a liquid sample valve (LSV) as the input to the analysis. The duration
of an analysis depends on the application and consists of the following:
The liquid sample valve injects a fixed volume of sample into a vaporizing chamber.
“Sweep gas” transports the sample out of the vaporizing chamber.
Carrier transports the vaporized sample into the column.
The column then separates the components and passes them into the detector.
The detector measures the sample across the range of high to low concentration.
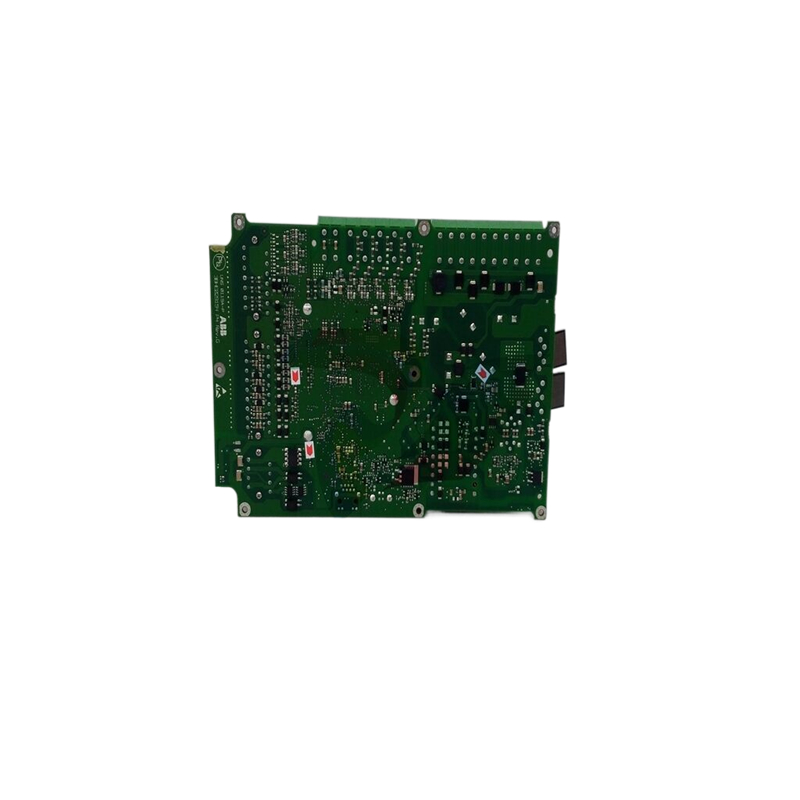
The liquid sample valve is externally mounted on the right side of the Oven Compartment and extends
through the isothermal oven, allowing direct injection. It is actuated by a solenoid valve located in the
Oven Electronics Compartment. The liquid sample valve captures a specific volume of liquid sample
below its bubble point, injects it into a temperature controlled (vaporizing) chamber of the LSV, which
then sends the vaporized sample into the oven.
1.4.2 Vapor version
The vapor version has a vapor input to the analysis, so it does not require a liquid sample valve. The
duration of an analysis cycle depends on the applications and consists of the following:
Carrier gas transports the vaporized sample through the columns.
The column then separates the components and passes them into the detector.
The detector measures the sample across the range of high to low concentration.
1.5 Class C oven
The Class C oven contains the same components as the Class B oven, but it has the capability to
handle more oven components. The Class C oven has a maximum of two detectors and a maximum of
six valves.
1.6 Oven with integrated controller
The oven with integrated controller can be either a Class B oven or a Class C oven. The distinguishing
feature is that an oven with integrated controller has the Single Board Computer (SBC) PCB installed
in the oven’s electronics compartment.
1.7 Air purge systems
The analyzer is suitable for a Class 1 Division 2 hazardous location, or an Ex Zone 2 area, without
purge and pressurization protection. Purge and pressurization protection of the electronics enclosure is
required for a Class 1 Division 1 location, or an Ex Zone 1 area. Refer to the analyzer nameplate for
purge and pressurization specifications.
1.8 System variations
This manual supports the basic PGC5000 Generation 2 analyzer. Section 9 presents additional
instruction for the PGC5000TPGC (temperature programmed GC). Section 10 includes information
about using the PGC5000A as a CAC replacement. For PGC5007 (fuel sulfur GC) and PGC5009 (fast
GC) information, see their respective manuals linked in the Additional information section.
2 Installation
WARNING – Bodily injury.
Before beginning installation, repair, or maintenance on the analyzer, contact the local Safety
Department to ensure that all safety guidelines, regulations and procedures are followed. This
includes obtaining the proper work permits.
The user is responsible for being familiar and complying with all safety and health guidelines,
regulations and procedures at the analyzer location. Consult Material Safety Data Sheets for
safety requirements.
When working on the analyzer, there is the possibility of exposure to hydrogen, nitrogen, and
other compressed gases. All appropriate precautions and extreme care should be taken when
working with all compressed gases.
Become familiar with the application specifications before working on the analyzer.
Wear protective clothing and equipment, such as rubber gloves and goggles or safety glasses
with side shields. Avoid contact with a hot surface during maintenance work on the analyzer
oven.
Before opening analyzer enclosure doors, be sure the area is safe from hazardous gases and
will remain so the entire time the analyzer is open.