ABB UCD208A101 Programmable Control Module
GeneralIt is important to be thoroughly familiar with the description of operation in
2 Description before starting fault tracing.
6.2 Interchangeability
The load cells are factory calibrated and can be replaced directly with another load cell of the same
type. The only adjustment required after load cell replacement is zero adjustment in the control
unit.
6.3 Fault Tracing Procedure
The measuring equipment can be divided into four parts:
• The mechanical installation.
• The load cell.
• The junction boxes and the cabling.
• The control unit (see the control unit manual).
The fault symptoms indicate in which part the fault lies.
• Faults in the mechanical installation often result in an unstable zero point or incorrect sensitivity.
If a fault follows something else in the process, such as temperature, or can be linked
to a particular operation, it probably originates from something in the mechanical installation.
• Load cells are extremely robust and can withstand five times their nominal load in the measuring direction.
If a load cell has nevertheless been so overloaded that its data have been
altered, this is probably due to an event in the mill, such as web/strip breakage. On excessive
overload the first thing that happens is that the zero point shifts.
• Problems such as interference or unstable zero point may be caused by wiring faults. Some
malfunctions may be due to the proximity of cables that cause interference. Incorrect installation,
such as imbalance in a cable or screens earthed at more than one end may cause the
zero point to become unstable. Cables are subject to mechanical wear, and should be
checked regularly. The junction box should also be checked, especially if it is subject to
vibration.
• A fault in the control unit usually causes intermittent loss of a function. It is unusual for the
control unit to cause stability problems. Faults in connected units may affect the operation of
the control unit. For further details see the control unit manual.
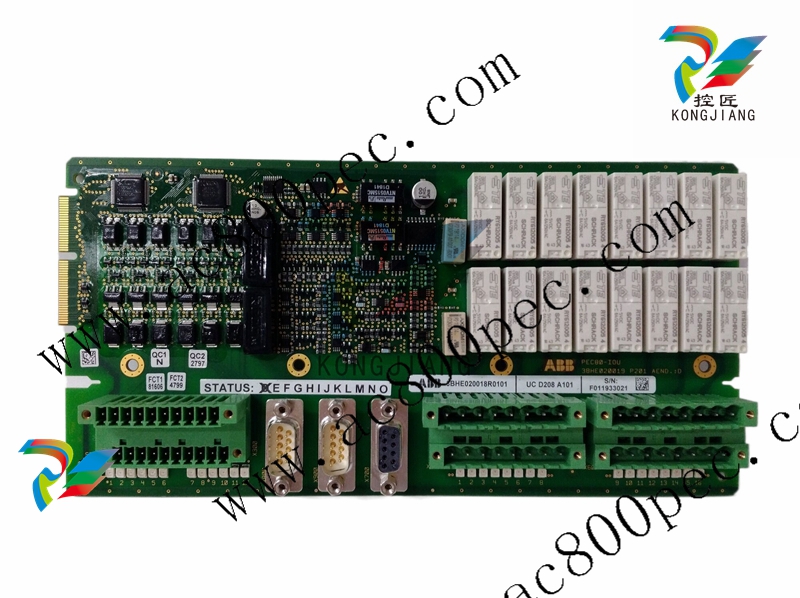
Fault Tracing in the Mechanical Installation
There are a number of parts in the mechanical arrangement that can cause faults. The extent to
which these faults are repeatable differs. Possible causes fall into the following groups.
• Defective mounting surface or adapter plates.
• Force shunting.
• (nsufficient mounting of load cell and adapter plates.
• Rolls and bearings.
• Driven roll.
6.4.1 Defective Mounting Surface, Support or Adapter Plates
An unmachined or poorly machined mounting surface, which is uneven, may cause bending or
twisting of the load cell. This may result in instability of the zero point.
6.4.2 Force Shunting
Force shunting means that some of the force is diverted past the load cell. This may be caused by
some kind of obstruction to the force through the load cell. The connecting cables, for example,
have been incorrectly installed and are preventing movement. Another possible cause is that the
roll is not free to move in the direction of measurement, possibly because something is mounted
too close to a bearing housing, or because an object has worked loose and become trapped
between the bearing housing and adjacent parts.
Force shunting causes the web/strip tension indication to be lower than the actual web/strip tension.
6.4.3 Fastening of Load cell and Adapter Plates
Screw joints that have not been properly tightened or have lost their pre-tightening force, cause
sliding at the mating surfaces. Fastening of the load cell is especially critical. If a load cell is not
properly secured, the zero point will be unstable. Sliding between other surfaces may cause the
same symptoms.
6.4.4 Rolls and Bearings
An incorrectly designed bearing arrangement may give rise to high axial forces. The roll should be
fixed at one end and free at the other.
If both ends are fixed there will be a high axial (thrust) force due to expansion of the shaft with
rising temperature.
Even a correctly designed bearing arrangement may deteriorate with time; bearings become worn,
and so on. This may give similar symptoms, such as slow zero point drift between cold and hot
machine, or sudden jumps in the signal.
6.4.5 Driven Roll
A source of error that is seldom suspected is the roll itself. The effect is especially critical when
measuring forces on the load cell are relatively low. Long drive shafts with their associated universal
joints may cause unstable signals if they are not properly maintained. It is important to lubricate