ABB 3HAC14550-2/09A single servo drive unit
Implementing thermal overload and short-circuit protectionProtecting drive and input power cables in case of short-circuits
Protect drive and input cables using fuses as follows:
Size the fuses at the distribution board according to instructions given in chapter Technical data. The fuses will
protect the input cables in short-circuit situations, restrict drive damage and prevent damage to adjoining
equipment in case of a short-circuit inside the drive.
Circuit breakers
The protective characteristics of circuit breakers depend on their type, construction and settings. There are
also limitations regarding to the short-circuit capacity of the supply network. Your local ABB representative can
help you in selecting the breaker type when the supply network characteristics are known.
WARNING
Due to the inherent operating principle and construction of circuit breakers, independent of the manufacturer,
hot ionized gases can escape from the breaker enclosure in case of a short-circuit. To ensure safe use, pay
special attention to the installation and placement of the breakers. Obey the manufacturer’s instructions.
Protecting the motor and motor cable in case of short-circuits
The drive protects the motor cables and motor in a short-circuit situation when the motor cables are sized
according to the nominal current of the drive. No additional protection devices are needed.
Protecting the drive and the input power and motor cables against thermal overload
The drive protects itself, its mains- and the motor cables against thermal overload when the cables are sized
according to the nominal current of the drive. No additional thermal protection devices are needed.
WARNING
If the drive is connected to multiple motors, use a separate circuit breaker or fuses for protecting each motor
cable and motor against overload. The drive overload protection is set to the total motor load. It may not trip
due to an overload in one motor circuit only.
Protecting the motor against thermal overload
According to regulations, the motor must be protected against thermal overload and the current must be
switched off when overload is detected. The drive includes a measured motor temperature function and a
motor thermal model function. They protect the motor and switch off the current when necessary.
Measured motor temperature:
For safety, the actual temperature indication is given by motor temperature sensors. The most common
temperature sensors are:
– Motor sizes IEC180 … 225: Thermal switch, e.g. klixon.
– Motor sizes IEC200 … 250 and larger: PTC or PT100.
See the DCS880 Firmware Manual for more information on the connection and use of the temperature sensors.
Motor thermal model:
Additionally, depending on drive parameter settings, an implemented function monitors a calculated
temperature value (based on a motor thermal model). The user can tune the thermal model by feeding in
additional motor and load data.
See the DCS880 Firmware Manual for more information on the motor thermal model.
WARNING
The motor thermal model function shall not be used solely as electronic motor overload protection safety
function.
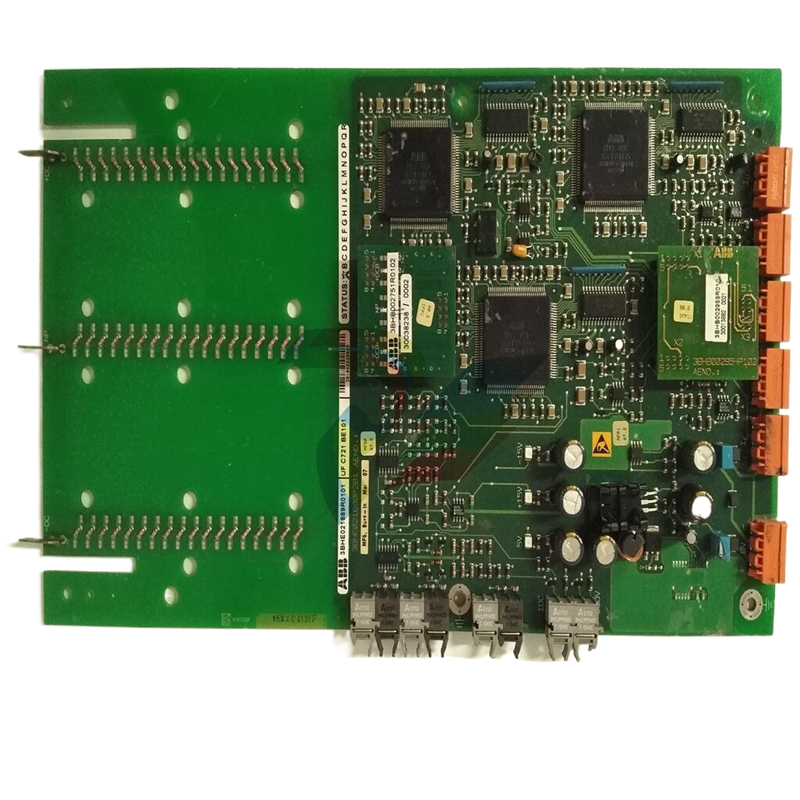
Cross-sectional areas - Tightening torques
Recommended cross-sectional area according to DINVDE 0276-1000 and DINVDE 0100-540 (PE) in a trefoil
arrangement, up to 50°C ambient temperature. The necessary wire torque at 60°C wire temperature is the same
as recommended in the following table.
Armature:
Reduced ambient temperature 40°C.
You will find instructions on how to calculate the PE conductor’s cross-sectional area in VDE 0100 or in
equivalent national standards. We would remind you that power converters may have a current-limiting effect.
Excitation:
Converter type C1, D1 U1, V1, W1 PE
[Nm] IDC
[A-]
1
[mm²]
(2.)
[mm²] Iv
[A~] [mm²] [mm²]
DCS880-S0b-0025-0d 25 1 x 6 - 21 1 x 4 1 x 10 1 x M6 6
DCS880-S0b-0050-0d 50 1 x 10 - 41 1 x 6 1 x 10 1 x M6 6
DCS880-S0b-0075-0d 75 1 x 25 - 61 1 x 25 1 x 16 1 x M6 6
DCS880-S0b-0100-0d 100 1 x 25 - 82 1 x 25 1 x 16 1 x M6 6
DCS880-S0b-0150-0d 150 1 x 35 - 114 1 x 35 1 x 16 1 x M10 25
DCS880-S0b-0200-0d 200 2 x 35 1 x 95 163 2 x 25 1 x 25 1 x M10 25
DCS880-S0b-0250-0d 250 2 x 35 1 x 95 204 2 x 25 1 x 25 1 x M10 25
DCS880-S0b-0300-0d 300 2 x 70 1 x 95 220 2 x 50 1 x 50 1 x M10 25
DCS880-S0b-0320-0d 320 2 x 70 1 x 95 220 2 x 50 1 x 50 1 x M10 25
DCS880-S0b-0350-0d 350 2 x 70 - 286 2 x 50 1 x 50 1 x M10 25
DCS880-S0b-0450-0d 450 2 x 95 - 367 2 x 95 1 x 95 1 x M10 25
DCS880-S0b-0520-0d 520 2 x 95 - 424 2 x 95 1 x 95 1 x M10 25
DCS880-S0b-0650-0d 650 2 x 120 - 555 2 x 120 1 x 120 1 x M12 50
DCS880-S0b-0680-0d 680 2 x 120 - 555 2 x 120 1 x 120 1 x M12 50
DCS880-S0b-0820-0d 820 2 x 150 - 669 2 x 120 1 x 120 1 x M12 50
DCS880-S0b-0900-06/07 900 4 x 95 3 x 150 734 4 x 70 1 x 150 2 x M12 50
DCS880-S0b-1000-0d 1000 2 x 185 - 816 2 x 150 1 x 150 1 x M12 50
DCS880-S0b-1190-0d 1190 4 x 120 - 971 4 x 95 2 x 95 2 x M12 50
DCS880-S0b-1200-0d 1200 4 x 120 - 979 4 x 95 2 x 95 2 x M12 50
DCS880-S0b-1500-0d 1500 4 x 185 - 1224 4 x 150 2 x 150 2 x M12 50
DCS880-S0b-2000-0d 2000 8 x 120 6 x 185 1632 4 x 240 2 x 240 2 x M12 50
DCS880-S0b-1900-0d 1900 8 x 120 6 x 185 1550 4 x 240 2 x 240 4 x M12 50
DCS880-S0b-2050-dd 2050 8 x 120 6 x 185 1673 6 x 120 3 x 120 4 x M12 50
DCS880-S0b-2500-0d 2500 7 x 185 - 2040 8 x 120 4 x 120 4 x M12 50
DCS880-S0b-2600-dd 2600 7 x 185 - 2122 8 x 120 4 x 120 4 x M12 50
DCS880-S0b-3000-0d 3000 8 x 185 - 2448 7 x 185 4 x 185 4 x M12 50
DCS880-S0b-3300-dd 3300 8 x 185 - 2693 7 x 185 4 x 185 4 x M12 50
DCS880-S0b-4000-dd 4000 7 x 300 - 3264 8 x 240 4 x 240 4 x M12 50
DCS880-S0b-4800-0d 4800 8 x 300 - 3876 6 x 300 3 x 300 4 x M12 50
DCS880-S0b-5200-0d 5200 8 x 300 - 4202 6 x 300 3 x 300 4 x M12 50
Size H1 H1 H2 H3, H5, H6 H4 DCF803-0035
DC output current 6 A 12 A 18 A 25 A 30 A 35 A
max. cross sectional area 6 mm²/ AWG 10 6 mm²/ AWG 10 6 mm²/ AWG 10 6 mm²/ AWG 10 6 mm²/ AWG 10 6 mm²/ AWG 10
min. cross sectional area 1 mm²/ AWG 16 2.5 mm²/ AWG 13 4 mm²/ AWG 11 6 mm²/ AWG 10 6 mm²/ AWG 10 6 mm²/ AWG 10