ABB 3HAC17326-1/02 M26 motor
Selecting the power cables
General rules
– Select the input power and motor cables according to local regulations.
– Select a cable capable of carrying the drive nominal current. See chapter Current ratings.
– Select a cable rated for at least 60°C maximum permissible temperature of conductor in continuous use.
– The inductance and impedance of the PE conductor/cable (grounding wire) must be rated according to
permissible touch voltage appearing under fault conditions (so that the fault point voltage will not rise
excessively when a ground fault occurs).
– A 600 VAC cable is accepted for up to 500 VAC.
– A 750 VAC cable is accepted for up to 600 VAC.
– For 690 VAC rated equipment, the rated voltage between the conductors (L1, L2, L3) of the cable should be at
least 1 kV.
– For mains voltages exceeding 690 VAC and DC voltages exceeding 850 VDC select power cables which comply
with local regulations.
It is recommended to select following cables:
– UL: 2 kV voltage class.
– EN: Rated voltage conductor to earth 1000 VAC/1500 VDC and rated voltage conductor to conductor
1600 VAC/3000 VDC.
– The protective conductor must always have an adequate conductivity.
Unless local wiring regulations state otherwise, the cross-sectional area of the protective conductor must
agree with the conditions that require automatic disconnection of the supply required in 411.3.2. of IEC
60364-4-41:2005 and be capable of withstanding the prospective fault current during the disconnection time
of the protective device. The cross-sectional area of the protective conductor can either be selected from the
table below or calculated according to 543.1 of IEC 60364-5-54.
The table below shows the minimum cross-sectional area related to the phase conductor size according to
IEC 61800-5-1 when the phase conductor and the protective conductor are made of the same metal. If this is
not so, the cross-sectional area of the protective earthing conductor shall be determined in a manner which
produces a conductance equivalent to that which results from the application of this table.
Additional US requirements
Use type MC continuous corrugated aluminum armor cable with symmetrical grounds or shielded power cable
for the motor cables if metallic conduit is not used. For the North American market, 600 VAC cable is accepted
for up to 500 VAC. 1000 VAC cable is required above 500 VAC (below 600 VAC). For drives rated over 100 amperes,
the power cables must be rated for 75°C (167°F).
Conduit
Couple separate parts of a conduit together. Bridge the joints with a ground conductor bonded to the conduit
on each side of the joint. Also bond the conduits to the drive enclosure and motor frame. Use separate conduits
for input power, motor, brake resistor and control wiring. When a conduit is employed, type MC continuous
corrugated aluminum armor cable or shielded cable is not required. A dedicated ground cable is always
required.
Note:
Do not run motor wiring from more than one drive in the same conduit.
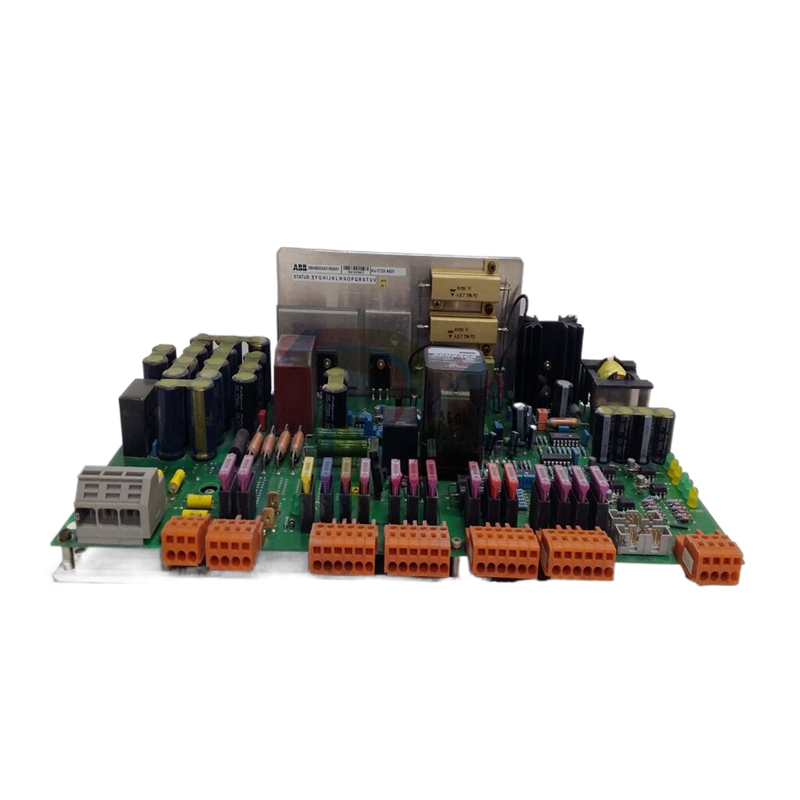
Armored cable/shielded power cable
Six conductor (3 phases and 3 ground) type MC continuous corrugated aluminum armor cable with symmetrical
grounds is available from the following suppliers (trade names in parentheses):
– Anixter Wire & Cable (Philsheath).
– BICC General Corp (Philsheath).
– Rockbestos Co. (Gardex).
– Oaknite (CLX).
Shielded power cables are available from Belden, LAPPKABEL (ÖLFLEX) and Pirelli.
Selecting the control cables
Shielding
All control cables must be shielded.
Use a double-shielded twisted pair cable (figure A below) for analog signals. This type of cable is also
recommended for the pulse encoder signals. Employ one individually shielded pair for each signal. Do not use
common return for different analog signals.
A double-shielded twisted pair cable (figure A below) is the best alternative for low-voltage digital signals but a
single-shielded twisted pair cable (figure B below) is also acceptable.
A: Double-shielded twisted pair cable. B: Single-shielded twisted multi pair cable
The pairs should be twisted as close to the terminals as possible.
Signals in separate cables
Run analog and digital signals in separate, shielded cables. Never mix 24 VDC and 115/230 VAC signals in the
same cable.
Signals allowed to be run in the same cable
Relay-controlled signals, providing their voltage does not exceed 48 V, can be run in the same cables as digital
input signals. The relay-controlled signals should be run as twisted pairs too.
Relay cable type
The cable type with braided metallic screen (for example ÖLFLEX by LAPPKABEL, Germany) has been tested and
approved by ABB.
Control Panel cable length and type
In remote use, the cable connecting the control panel to the drive must not exceed three meters (10 ft).
Cable type: Shielded CAT 5e or better Ethernet patch cable with RJ-45 ends.