GE 8522-EB-MT Ethernet Bus Interface
Wide choice of fieldbus optionsF8000 supports a number of popular fieldbus
protocols: Modbus® (RTU mode), Profibus–DP,
eDNP3 and Modbus TCP over Ethernet.
Redundancy options
8000 has been designed to increase availability and minimise downtime. Redundant
LAN channels and power supplies can be
specified as options to increase system availability. All Controllers can be used in redundant
configurations, as can the 8507-BI-DP BIM for
Profibus DP remote IO. Possible downtime is
further reduced by ensuring that the system
components using active circuitry can be
removed and replaced quickly and easily. Even
the field terminals can be replaced without
interrupting the operation of adjacent I/O
modules. Carriers have no active circuitry and
are unlikely to need replacement.
System power supplies
The system power supply at an 8000 node
converts the local DC supply to power the
node and can also provide field power for
I/O modules with low-level field circuits.
Where heavy-current or AC mains circuits
are handled by the I/O modules, 8000’s
innovative Bussed Field Power scheme for
distributing field power avoids complex
wiring at the field terminal and minimizes the
backplane/carrier wiring.
Hazardous area applications
The 8000 is a truly field mountable system
even in areas where flammable gases are
present. It is available in versions to suit
different area classification schemes:
a) Reduced commissioning time and cost
b) Reduced process downtime through status
monitoring
c) Lower loop maintenance costs by using
field device diagnostics
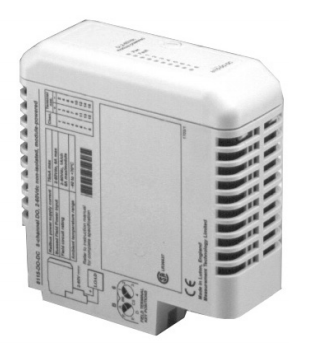
PAC8000 with general purpose field wiring
The PAC8000 2/2 IO module range is used
for general purpose and Zone 2 / Division
2 applications (where the node or the field
instrumentation are sited in the hazardous
area). See Figure 2. PAC8000 supports a full
range of I/O module types covering inputs
and outputs for both analog and discrete
circuits. The node can be mounted on the
plant with a suitable enclosure providing
protection against the environment. Figure 3
shows a node containing all the key compo nents: a Bus Interface Module or Controller,
I/O modules on carriers and a pair of carrier extenders linked with an extension cable.
Power supplies are not shown, but arrows
indicated the location of the BFP connectors.
PAC8000 with intrinsic safety field wiring
The PAC8000 Process I/O System is capable
of supporting I/O modules with intrinsic safety
(IS) field wiring, for connection to certified or
‘simple apparatus’ field devices in Division 1
or Zone 0 hazardous areas (see Figures 2 and
4). A range of I/O module types with IS field
circuits for industry standard DI, DO, AI and
AO applications is supported. (Note, there is
no concept of Bussed Field Power with 2/1
IO modules, all field power is sourced from
internal power supply connections, via the IO
module power supply, see below).
I/O modules with built-in protection
All voltage and current-limiting components
required for IS protection are incorporated
within the I/O module housings, so no
external, add-on zener barriers or galvanic
isolators are necessary. IS field terminals
are distinguished from other types by blue
coloring of the housing. A unique and sophis ticated mechanical keying mechanism helps
to prevent modules with different protection
techniques from being interchanged, so that
potentially explosive or damaging conditions
cannot occur.
Integrated power supplies
Power for IS I/O modules is derived from
integrated, modular power supply units. Each
power unit is capable of supplying between
eight and twenty I/O modules, depending on
the I/O type and mix. Optional power supply
redundancy is supported by means of an
additional, redundant supply unit connected
in an ‘n+1’ arrangement. In applications with
mixed IS and non-IS field wiring, the full facili ties of the ‘Bussed Field Power’ regime are
retained for the non-IS part of the system.