ABB AC700F controller with direct S700 I/O
AlzChem GmbH in Trostberg, a subsidiary of Evonik IndustriesAG, produces specialty chemicals products with a wide range
of uses. These chemicals are used, for example, in the production of crop protection products, pigments, dyes, pharmaceuticals and polymers.
In the past, an inverted filter centrifuge in a system for extracting natural substances was PLC-controlled at AlzChem GmbH.
The program code for the PLC, a standard program from the
manufacturer, was not transparent and needed specialists to
make changes. The program was not intuitive and diagnostic
analyses were only available to a very limited extent. In order
to simplify programming and to optimize the process control,
AlzChem thus decided to use the AC 700F controller. This replaced the PLC and was integrated into the existing Freelance
800F system without any problems.
This offers several advantages for AlzChem: The use of one
single engineering tool to configure the entire system simplifies
engineering and saves a significant amount of time during
commissioning. After transferring the program the system is
easy to understand and maintenance is simpler.
During the operating and maintenance phase, the wide range
of diagnostic options (sequence control-, hardware -, interlock
diagnostics), the intuitive graphical user interface and mature
alarm and report management allow costs to be cut. This
reduces downtime of the application and cuts maintenance
Project: System for extracting natural substances,
AlzChem GmbH, Trostberg, Germany
Industry: Chemicals
expenditures. All this improves the efficiency of the entire
system and the slightly higher acquisition costs compared to
a PLC amortize within a very short time.
Hartmut Rohner, Head of Electrical Systems, Instrumentation
and Control at AlzChem, is particularly impressed by the simple
and clear handling of the AC 700F controller and the Freelance
800F system. “It is easy for anyone to learn how to operate
the software and hardware. In contrast, it was practically impossible to understand the standard program supplied by the
manufacturer together with the centrifuge.” Mr. Rohner also
sees clear advantages over other systems when it comes to
maintenance and faultfinding. Whereas with other manufacturers faultfinding is only possible using a handheld device in
the field, Freelance 800F provides extensive analysis options
right in the control room. “Now I look at the status and can
see straight away where the error is. That is not possible that
simply in other systems.” This makes fault finding and maintenance substantially easier.
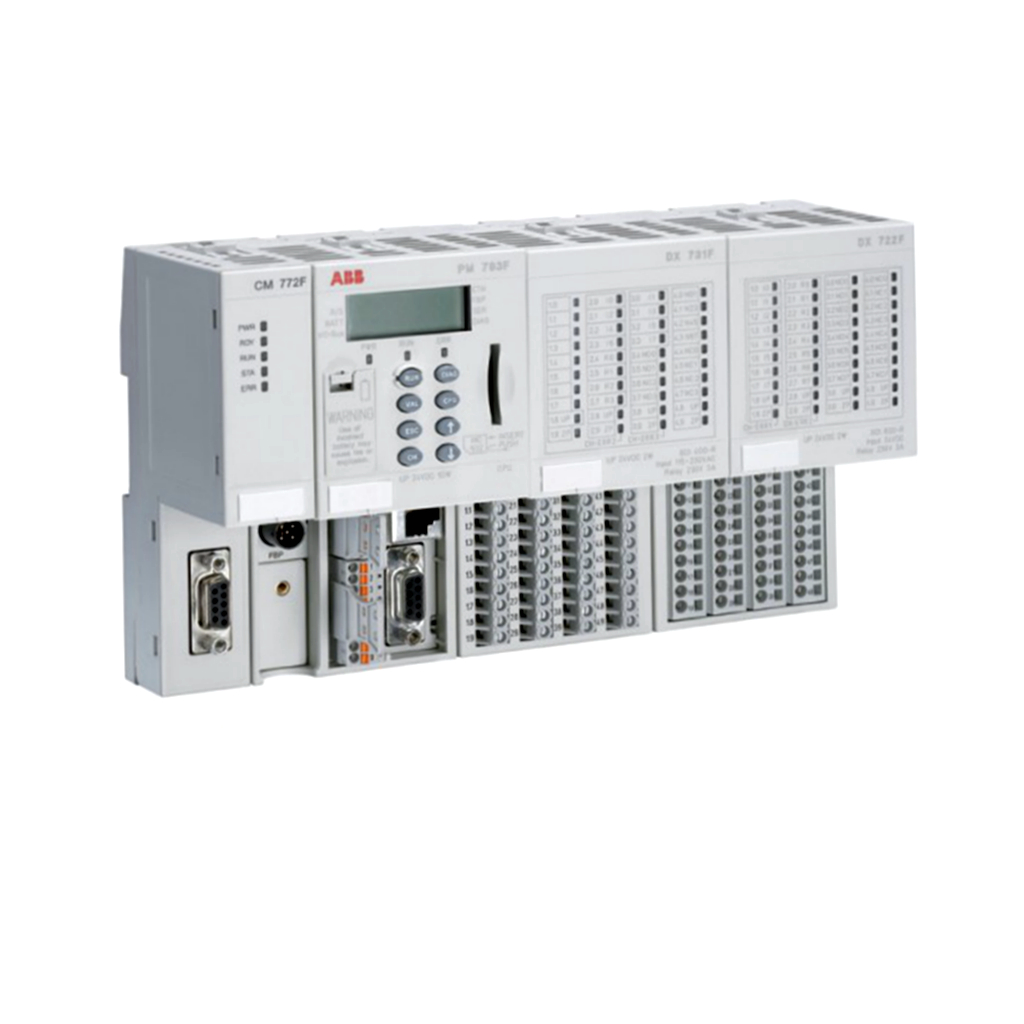
Northam Platinum Ltd. is based in Johannesburg, South Africa,
and mines and produces precious metals. Convertors are
used to extract platinum from ore. These convertors are driven
using electrical motors. Until now, a PLC controlled the motors’
direct motor starters. This operating mode was not reliable
and efficient enough for Northam, as the motors thus operate
constantly at full output. That reduces the lifespan of the components and causes higher repair and maintenance costs to
increase.
When the application was modernized and converted to frequency converters to increase energy efficiency, the outdated
PLCs were to be replaced. Customer requirements were a
more compact controller, an improved presentation of alarms
and results and an excellent cost/benefits ratio.
Northam opted for the new AC 700F controller when replacing
PLCs for the converters. Northam has been using the Freelance
800F system to control its smelting furnaces and other applications for many years and is convinced by the systems performance.
One AC 700F controller now regulates one variable-speed
drive. The motor output can be adjusted at any time to the
current operating requirements of the application, as frequency
converters can be simply driven by the controller. The adjustment allows up to 50% of energy savings and processes can
be better controlled. The increase in efficiency resulting from
the intelligent speed control can be used in two ways: to increase productivity or to keep production stable while simultaneously reducing energy consumption.
Integration of the AC 700F controller into the existing Freelance
800F system and the easy engineering with just one engineering tool, “Control Builder F” simplify commissioning and maintaining of the entire application. The configuration is particularly
simple as the visualization is also created with Control Builder
F. Separate tools for programming the PLCs and to create
operator images are no longer needed. Technicians now only
need to handle a uniform engineering tool system wide. Production data and information such as signal descriptions,
current and historical data, reports and detailed status information can be recorded over several years in the information
management tool PGIM 800F.
As a result of its positive experience, Northam will modernize
additional converters and other small plants using the AC 700F
controller in the near future.
Osby Parca produces high-performance boilers for hot water
and steam. The product range spans from electric boilers with
36 kW through to oil boilers with 16 MW. Osby Parca offers a
wide variety of solutions: for solid fuels, steam, gas, oil, electricity and heat recycling, flue gas cleaning and biomass systems. These boilers are delivered to both small customers and
key accounts - from sole proprietors for pipe installations to
industrial customers and distance heating plants.
In order to control the fully-automated solid fuel boiler Osby
PB2, Osby Parca has been using ABB’s compact Freelance
800F control system for several years. This boiler, with output
of 350 to 3000 kW is used to burn dry wood fuels such as
pellets and briquettes. The control adjusts the combustion to
the current load to ensure that there is a constant inlet temperature. Sensors and actuators regulate the draught in the
firing plant, the movement of the grate and the fuel supply.
Adjusting the draught in the firing plant controls the amount
of air for the combustion process. This allows continuous
control across the entire range of outputs. The combination
of the boiler and the control system allowed Osby Parca to
win several projects and it has equipped various power plants
in Sweden.
The Osby P500 model is a solid-fuel boiler for burning dry
wooden fuels such as pellets, briquettes, peat and wood
chips. The product range comprises four boilers with output
of 100 - 1000 kW. In the past, Osby Parca used a PLC to
control these boilers, as process control technology with
comprehensive features was too expensive for the smaller
models. In the majority of cases, the boilers were independent
sub-sections of a total plant and as a result they were controlled as a “standalone solution”. That is why many users often
decided to use the lowest-priced hardware/software solution
when selecting the automation systems to be used.
This clearly shows the advantages offered by the great scalability of the Freelance 800F system together with the new
AC 700F controller. Osby Parca can now use the wide-ranging
advantages offered by Freelance 800F at a price similar to
PLC + SCADA systems when controlling the smaller boilers.
Compared to PLC + SCADA, a process control system offers
more functionality, for example automatically generated diagnostic information and alarms as well as easy and fast online
optimizations of applications.
In addition, simplified remote diagnostics in central control
rooms is possible, as the control technology automatically
generates system alarms and system diagnostics, which are
available using PC technology.
Osby Parca is very pleased: “The AC 700F Controller combines
the functionality of a control system with the price level of a
PLC with a visualization solution. The uniform tool for configuring the controller and the operator station with automatically
generated faceplates (operator windows) saves time for engineering and commissioning. Time can also be saved in ongoing
operation and for maintaining the application thanks to advanced
diagnostics opportunities and improved alarm handling. This
cuts installation costs and significantly increases the plant’s
economic efficiency.”
Osby Parca is convinced of the opportunities offered by the
Freelance 800F control system and in future it will fit even
more boilers with AC 700F and AC 800F controllers.
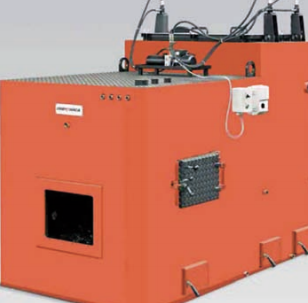
At Sasol in Brünsbüttel the AC 700F controller has been installed to control a pneumatic conveyor system for aluminum
oxide powder. This system was controlled using a PLC in the
past. Sasol is a convinced, long-standing user of the compact
control system Freelance 800Fand thus decided to use the
AC 700F Controller when replacing the PLCs. Customer requirements were the transfer of the existing application into
the new controller, the subsequent optimization of process
control through the use of diagnostic features and short setup
and installation times.
In addition, the system was to be configured by one of the
customer’s application engineers, who had never worked with
the Freelance 800F system before. After a short training period
and with ABB’s support during the start-up phase, it was possible to successfully put the project in operation in the shortest
timeframe. The easy-to-learn and intuitive configuration of
Freelance 800F was the crucial factor for Sasol when they
chose the control system.
Thanks to the compact footprint of the AC 700F controller,
the old PLC control could be exchanged without having to
modify the control cabinets - even the existing wiring in the
control cabinet remained unchanged. This allowed considerable advantages to be gained in respect of operation and fault
diagnostics but with minimal outlay. The main advantages of the
compact Freelance 800F system compared to a PLC solution
are the simple configuration, operating the plant from the
control room and the possibility of remote access for maintenance work.
A touch screen operator station replaces the switches and
lights at the control cabinet formerly used as operation elements. This makes it easier for plant operators to control the
equipment locally and also allows all of the other systems
connected to the process control system to be used.
At Sasol, other outdated control cabinets are to be modernized
with the new AC 700F controller in the near future