ABB AI625 3BHT300036R1 16-point analog input unit
Protecting the relay output contacts and attenuating disturbances in case
of inductive loads
Inductive loads (relays, contactors, motors) cause voltage transients when switched
off.
The relay contacts on the RMIO board are protected with varistors (250 V) against
overvoltage peaks. In spite of this, it is highly recommended to equip inductive loads
with noise attenuating circuits [varistors, RC filters (AC) or diodes (DC)] in order to
minimize the EMC emission at switch-off. If not suppressed, the disturbances may
connect capacitively or inductively to other conductors in the control cable and form
a risk of malfunction in other parts of the system.
Install the protective component as close to the inductive load as possible. Do not
install protective components at the RMIO board terminal block.
Selecting the control cables
All control cables must be shielded.
Use a double-shielded twisted pair cable (Figure a below) for analogue signals. This
type of cable is recommended for the pulse encoder signals also. Employ one
individually shielded pair for each signal. Do not use common return for different
analogue signals.
A double-shielded cable is the best alternative for low-voltage digital signals but
single-shielded twisted pair cable (Figure b) is also usable.
Run analogue and digital signals in separate, shielded cables.
Relay-controlled signals, providing their voltage does not exceed 48 V, can be run in
the same cables as digital input signals. It is recommended that the relay-controlled
signals be run as twisted pairs.
Never mix 24 VDC and 115/230 V AC signals in the same cable.
Relay cable
The cable type with braided metallic screen (e.g. ÖLFLEX by LAPPKABEL,
Germany) has been tested and approved by ABB.
Control panel cable
In remote use, the cable connecting the control panel to the drive must not exceed 3
metres (10 ft). The cable type tested and approved by ABB is used in control panel
option kits.
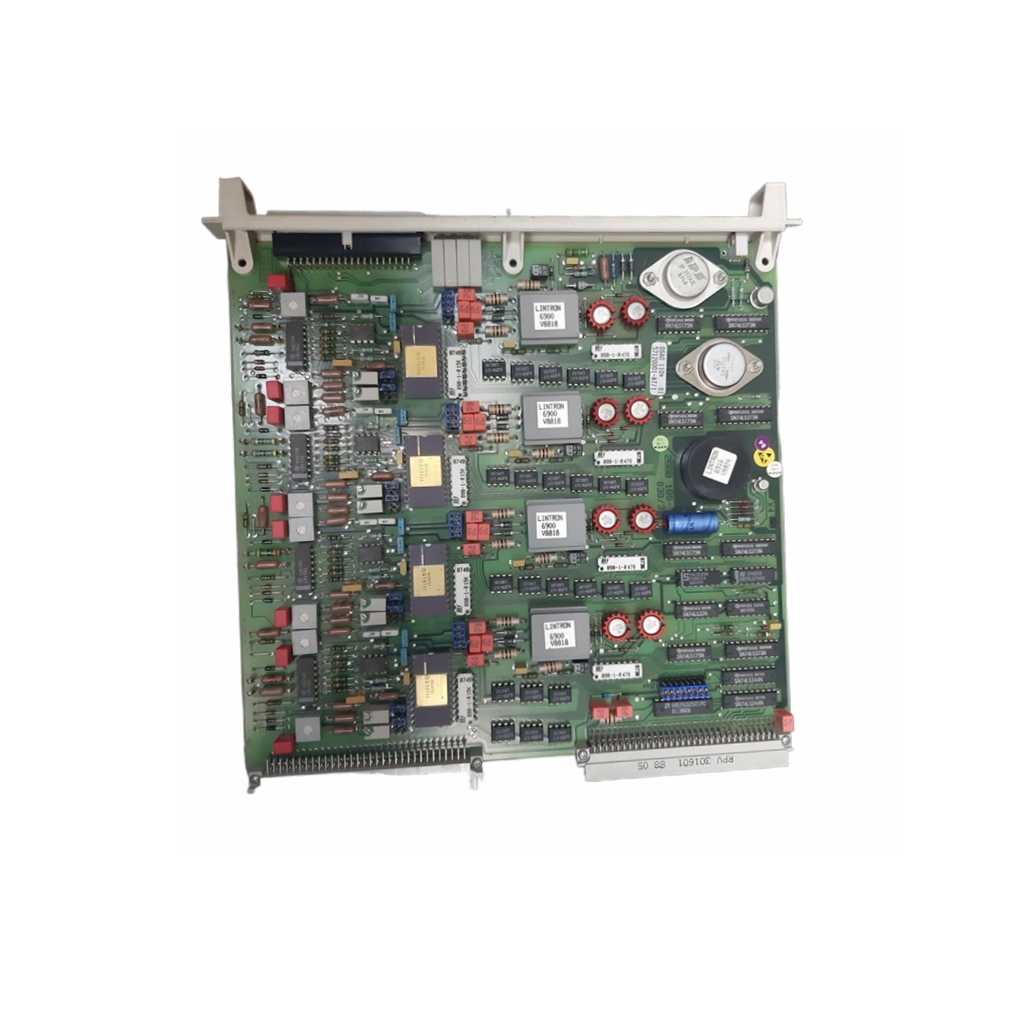
WARNING! IEC 60664 requires double or reinforced insulation between live parts
and the surface of accessible parts of electrical equipment which are either nonconductive or conductive but not connected to the protective earth.
To fulfil this requirement, the connection of a thermistor (and other similar
components) to the digital inputs of the drive can be implemented in three alternate
ways:
1. There is double or reinforced insulation between the thermistor and live parts of
the motor.
2. Circuits connected to all digital and analogue inputs of the drive are protected
against contact and insulated with basic insulation (the same voltage level as the
drive main circuit) from other low voltage circuits.
3. An external thermistor relay is used. The insulation of the relay must be rated for
the same voltage level as the main circuit of the drive. For connection, see the
appropriate ACS800 firmware manual.
Installation sites above 2000 metres (6562 feet)
WARNING! Protect against direct contact when installing, operating and servicing
the RMIO board wiring and optional modules attached to the board. The Protective
Extra Low Voltage (PELV) requirements stated in EN 50178:1997 are not fulfilled at
altitudes above 2000 m (6562 ft).
Routing the cables
Route the motor cable away from other cable routes. Motor cables of several drives
can be run in parallel installed next to each other. It is recommended that the motor
cable, input power cable and control cables be installed on separate trays. Avoid
long parallel runs of motor cables with other cables in order to decrease
electromagnetic interference caused by the rapid changes in the drive output
voltage.
Where control cables must cross power cables make sure they are arranged at an
angle as near to 90 degrees as possible. Do not run extra cables through the drive.
The cable trays must have good electrical bonding to each other and to the
grounding electrodes. Aluminium tray systems can be used to improve local
equalizing of potential.