ABB AI801 3BSE020512R1 DCS programming analog input unit
What this chapter containsThis chapter instructs in the cabling of the drive.
Warnings
WARNING! Only qualified electricians are allowed to carry out the work described in
this chapter. Follow the Safety instructions on the first pages of this manual. Ignoring
the safety instructions can cause injury or death.
Checking the insulation of the assembly
Drive
Do not make any voltage tolerance or insulation resistance tests on any part of the
drive as testing can damage the drive. Every drive has been tested for insulation
between the main circuit and the chassis at the factory. Also, there are voltage limiting circuits inside the drive which cut down the testing voltage automatically.
Supply cable
Check the insulation of the supply (input) cable according to local regulations before
connecting to the drive.
Motor and motor cable
Check the insulation of the motor and motor cable as follows:
1. Check that the motor cable is connected to the motor, and disconnected from the
drive output terminals U2, V2 and W2.
2. Measure the insulation resistance between each phase conductor and the
Protective Earth conductor using a measuring voltage of 1000 V DC. The
insulation resistance of an ABB motor must exceed 100 Mohm (reference value
at 25 °C or 77 °F). For the insulation resistance of other motors, please consult
the manufacturer’s instructions. Note: Moisture inside the motor casing will
reduce the insulation resistance. If moisture is suspected, dry the motor and
repeat the measurement
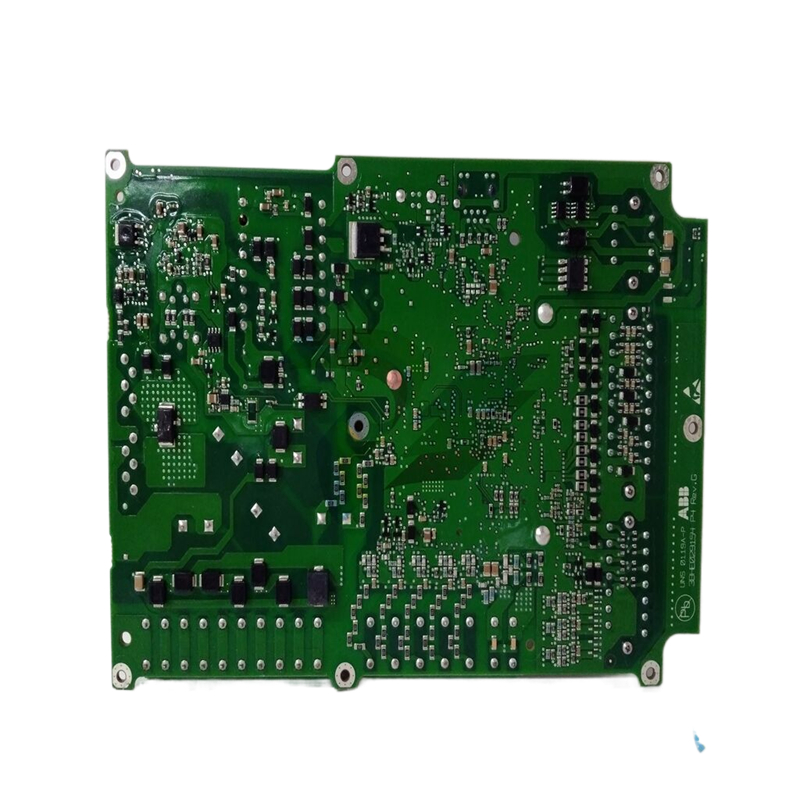
A drive equipped with no EMC filter or with EMC filter +E210 is suitable for IT
(ungrounded systems).
Note: You cannot disconnect an EMC filter from the drive.
WARNING! If a drive with EMC filter +E202 is installed on an IT system [an
ungrounded power system or a high-resistance-grounded (over 30 ohms) power
system], the system will be connected to earth potential through the EMC filter
capacitors of the drive. This may cause danger or damage the unit.
If shielded cable is used (not required but
recommended) and the conductivity of the shield is
< 50% of the conductivity of the phase conductor,
use a separate PE cable (1) or a cable with a
grounding conductor (2).
Ground the other end of the input cable shield or PE
conductor at the distribution board.
3) 360 degrees grounding recommended at the cabinet
entry if shielded cable
4) 360 degrees grounding required at the cabinet entry
in first environment installations **
5) Use a separate grounding cable if the conductivity of
the cable shield is < 50% of the conductivity of the
phase conductor and there is no symmetrically
constructed grounding conductor in the cable (see
Planning the electrical installation: Selecting the
power cables).
Note:
If there is a symmetrically constructed grounding
conductor in the motor cable in addition to the
conductive shield, connect the grounding conductor to
the grounding terminal at the drive and motor ends.
Do not use an asymmetrically constructed motor cable.
Connecting its fourth conductor at the motor end
increases bearing currents and causes extra wear.