ABB ASTAT Crane motion controller
ASTAT, with slip-ring motors, has become the
leading technology for new heavy industrial
cranes in the growth regions of the world.
In Europe, ASTAT is mostly used for retrofit
installations or when normal industrial drives
are unable to fulfil the requirements.
We supply ASTAT solutions for applications up
to 4000 A or 4700 kVA.
The ASTAT Digital Crane Motion Controller has
better control and information properties
compared to earlier controllers. Equally
important is the focus on quality of hardware
components. The digital controller can be
mounted on a steel plant crane in hot countries
such as India without extra cooling or air
conditioning. This capability provides additional
benefits to worldwide industrial crane users.
i.e. The crane control system must withstand
dirty, hot and cold environments in addition to
difficult power supply systems. This has forced
us to integrate functions like brake control, time
relays, logic control and thermistor relays into
the ASTAT controller. Generic products with the
same robustness as the ASTAT controller are
difficult to find. With this level of integration we
offer a complete, fully tested motion control
system.
Slip-ring motors may be produced with small
internal rotor losses. This is important in crane
applications with multiple motors and a high
demand for good motion control. As well as
being ideal for crane applications, slip-ring
motors are low on maintenance with brushes
being exchanged only every 5 to 10 years.
ASTAT uses the slip-rings for measurement of
the rotor frequency and from this calculates the
speed. In most cases no tachometer or pulse
encoder is necessary.
The operator controls the crane motion, while
all rotor contactors are optimized by ASTAT, as
an integrated part of the current control. This
results in dramatically reduced wear of
contactors and crane mechanical parts. Crane
maintenance costs will therefore be reduced.
Advantages with ASTAT®:
• Fewer and better components result in more up-time.
• Operational diagnostics will speed-up fault tracing.
• Multipurpose spares will reduce parts in stock.
• The PC-program for maintenance can be installed in
a ground level computer. Nobody has to visit the crane
first to find the problem.
Digital ASTAT motion control is superior to other
techniques and it increases the operational results to the
limits of the crane itself. For you as a user it will create:
• Increased productivity. The operator moves the
crane without jogging, i.e. with one single movement.
• Prolonged lifetime. Smooth acceleration and
retardation decreases torque peaks.
• Special functions reduce rope and brake wear.
• Satisfied operators. Motion control is possible down
to increments of only one cm. Try to do such a small step
without the ASTAT system!
• Excellent control features permit higher speed
during automatic control.
When to select ASTAT® ?
ASTAT is suitable for crane control in demanding
environments, when larger motor powers must be
handled, for retrofits or when automating one or more
cranes.
Hardware
1) New thyristor module DASD 145, 600 V - 500 A
2) Improved speed control with incremental encoder at very low speed with new firmware PU_APP12 in DAPU
100 board (from May 2007)
3) Start of replacement of semiconductor fuses from higher voltage to 690 V with higher current rating in DASD
146, 147, 156, 157 based on the technical development.
4) Control sequence for output relays and safety brake lifter contactor for DARA 200 supervision system.
Software functions
5) Display of DAPC 100 shows "54" when there is no Fault. "54 indicates 10_05, revision 4.
6) A large number of parameters fixed to constants for quicker parameterisation.
7) Acceleration control of travel motions as alternative to speed control developed and included.
8) Torque control with DARA 1001 is removed as acceleration control is better. SW release 10_053 shall be
asked for when ordering spare part board DAPC 100.
9) Positioning "Soft limit switch" is removed as positioning on incremental encoder no more is recommended due
to the development of absolute encoders. SW release 10_053 shall be asked for when ordering spare part
board DAPC 100.
10) Firing angle can be modified in regenerative mode. Extremely loaded motors with high CosFi that else can operate in two-phase mode with heavy mechanical vibrations.
11) Correction of execution time to prevent a 10 ms long brake opening when trying to lift a load with load above
the mechanical overload level.
12) Supervision time of MF-link and Remote I/O-link set to 500 ms time.
13) Fast stop function included; an active or passive signal can force the motion controller to sop also in healthy
mode with master switch in driving position.
14) Speed dependent gain improved by separate break points for stand still (0% reference) in addition to existing
10%, 25%, 50% and 100% speed reference.
15) A step reference can be optimised for light motions (travel or hoist) by setting 08.01 to 5. With value 5 over
shooting is prevented as the integral part of the speed regulator is set to zero each time the ramp output value
coincides with the step reference. By setting 08.01 to 6 the integral part is not reset, which minimises load
droop for hoists and is more suitable for fine positioning of heavy travel motions.
16) Standard value for switch to super synchronous speed changed from 85% to 95% speed.
17) Better function to enter in open control with light load. Full motor voltage is no longer required.
18) Contactor K3 will always close in super synchronous mode, if installed.
19) Function "Adoption to low line voltage with longer ramp times" is fixed, and cannot be deselected.
20) DO 6 can be used off-delayed to control, as example, lubrication pumps or rail cleaning blowers.
21) DI 15 can be used to switch between parameter sets 1 and 2 in installations without any remote I/0.
10_055
Software functions
22) Display of DAPC 100 shows "55" when there is no Fault. "55 indicates 10_05, revision 5.
23) Bypass functions as rescue operation with one of two (large) motors, and for E-room/cubicle loss reduction
24) Faults for operation are as before reset by crane on command. Fault indication codes are reset by activation of
DI 2, and not automatically cleared as before.
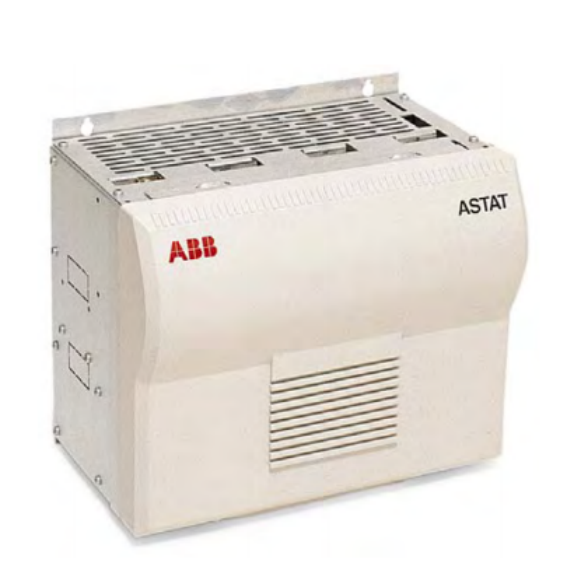
Hardware
25) Increased voltage range to 1000 V rated rotor voltage for EH rotor contactors.
Software functions
26) Display of DAPC 100 shows "53" when there is no Fault. "53 indicates 10_05, revision 3.
27) User does not have to contact ABB to modify a hidden parameter from its standard value to use MasterFollower. If that was not done,
the Followers brake was directly released when Masters Direction signals (A or
B) was removed.
28) Correction of logic for dynamic Master-Follower partner selection. Master-Follower partner is now fully selectable by macro-change.
29) Correction of very occasional trips in 60 Hz networks due to collision between current regulator execution and
communication links.
30) Rotor contactors do not open during acceleration in case reverse thyristor bridge is commended by speed regulator.
31) Rotor contactors K2 and K3 do not close during acceleration if the stator current is larger than parameter 12.10
for hoists and 12.11 for Travel motions. The system is less sensitive for line voltage dips and low class power
system design. The standard values should only be modified for macros used for temporary overload.
32) Standard values of parameter for rotor contactor closing time modified:
12.29 from 80 ms to 60 ms
33) Standard values of parameters related to thyristor bridge reversal have been modified; these are not modified
by most users:
11.44 from 30 ms to 20 ms
11.46 from 200 ms to 50 ms
34) Standard value of parameter 08.18 changed from 0 to 1. Standard is 1 meaning active function for line voltage
adopted ramp times.
Tool program
35) For Monitor and View recording, the gridlines can be turned on and off.
36) For Monitor and View recording, two lines for each of six signals can be displayed.
37) For View recording, a vertical time-line can be moved in the chart, and the signal values at this time are presented.
38) Possible to add comments to record files, ∗.asg.
10_053A, ex works from 2006-08-01
Software functions
39) The additional brake setting based on speed reference has been corrected. The normal brake setting has worked and works without any remark.
40) The associated timer function for brake setting based on speed reference, parameter 06.08, has incorrectly
been implemented as an ON-delay of reference coming to zero instead as an OFF-delay. Well working installations should not be modified.
41) A Follower in a MF-configuration is changed to use the uncorrected Masters speed reference for brake set-ting
instead of the Followers lively speed reference. The action is more predictable. Well working installations should not be modified.
42) The slow down and stop limit switches in Master-Follower are corrected according to the existing specification
to a true OR-action between the Masters and Followers limit switches.
10_053B, ex works from 2006-09-03
Software functions
43) For Master-Follower such states in Follower that cause fault codes in Follower, but not requires the Master to
stop are not causing Master-Follower links faults any more.
44) Master-Follower link supervision corrected. Permitted down time was always zero (un-delayed trip), what-ever
parameter value was set. After correction the trip is delayed with value in milliseconds of parameter 30.01.
45) Automatic resynchronization of Electrical Shaft after reactivation of the mode (in practice at first CRANE ON after changing
from single drive to Master-Follower) restored after having been removed by mistake in Release
10_03A.
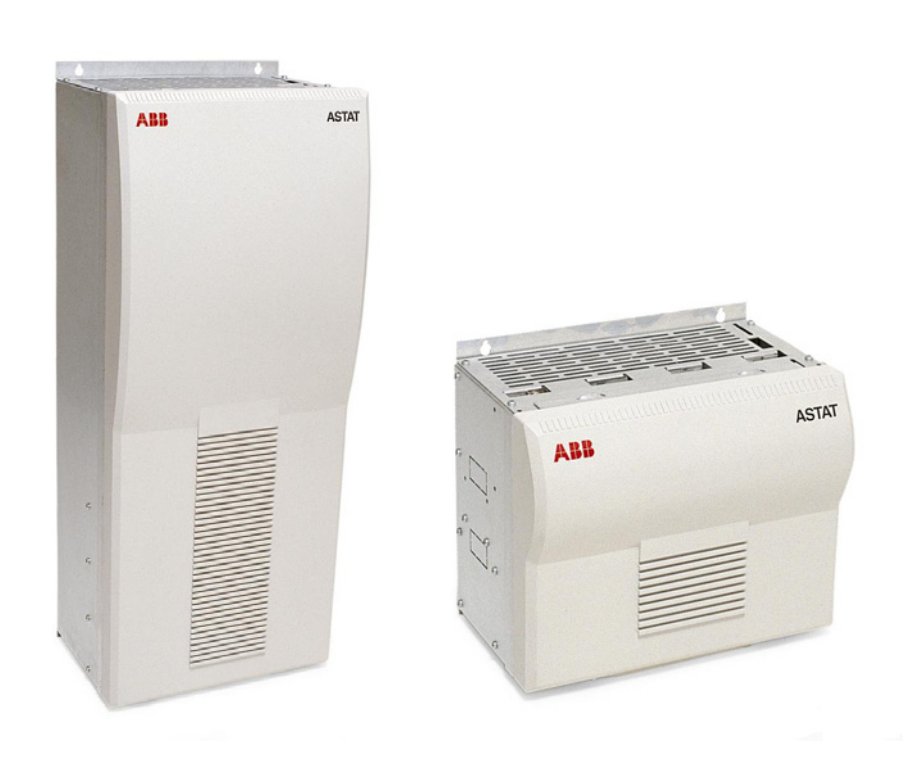
3ASC25H204 DAPU100,3ASC25H214DATX130,3ASC25H219B DATX133