ABB Advant Controller 31
The AC 31 brings accessibility to beginners and experienced automation users alike, for anyapplication with 14 to 1000 inputs / outputs and more, using the same set of basic
components.
From a compact machine fitted with a few automated functions to large installations spread
over hundreds of meter, and even kilometers, the AC 31 can fit your requirements.
It is therefore possible to realize distributed applications throughout a site, a workshop, or a
machine where each component (input / output unit, central unit) is close to the sensors /
actuators. The whole setup is connected by a single twisted pair over which all information
from the sensors is sent after processing by the central unit to the actuators, as well as
distributed intelligent units. The following communication interfaces are available, to extend the
AC 31’s possibilities and integration with the company's other automation systems:
MODBUS , ASCII, ARCNET , RCOM, AF100. The developments in this field are continual.
Many users on all the continents have realized numerous applications such as:
Machine control
Manufacture of floor boards
Assembly of electrical contactors
Manufacture of ceramic products
Metallic pipe welding, etc.
Controlling-commanding installations
Wharf cranes
Water treatment
Ski lifts
Wind power machines, etc.
Systems management
Climatic management
Building power management
Tunnel ventilation
Alarms in hospital environments
Greenhouse lighting / humidity, etc.
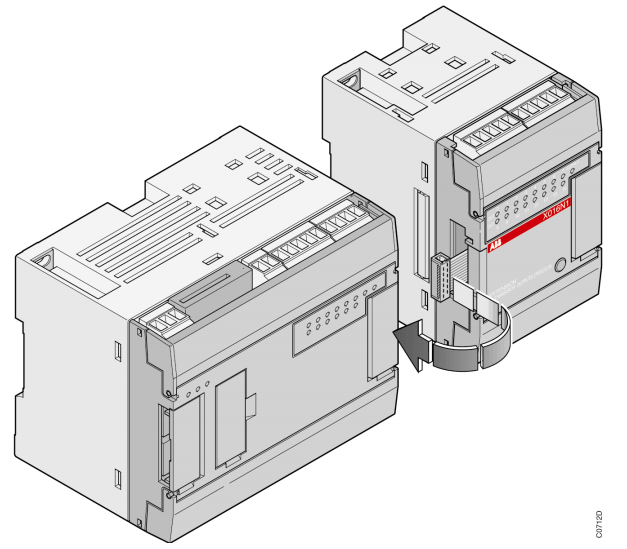
An ABB AC 31 system always includes an AC 31 central unit. There are three types of central
units:
- The 40 series central unit, with a local inputs / outputs extensions interface
- The 50 series central unit, with a local inputs / outputs extensions interface
and a CS 31 bus interface
- The 90 series central unit, with a CS 31 bus interface
Each central unit incorporates a specific number of binary inputs / outputs and occasionally
analog. It is possible, depending on the central unit, to increase the number of inputs / outputs,
to add input / output extensions connected directly to the central units or remote input / output
units via the CS 31 twisted pair.
The 40 and 50 series. It’s possible to increase the number of inputs / outputs of the basic
central unit by adding up to 6 local extension units of either type, binary or analog (Figure 1-1).
2.2. Central units with CS 31 bus
The 50 and 90 series. It’s possible to increase the number of inputs / outputs of the basic
central unit by adding remote units. The central unit controlling the system is called the
MASTER central unit. The maximum bus length is 500 m without an amplifier and 2000 m with
3 amplifiers (1 NCB or NCBR unit enables bus amplification for 500 m).
The master central unit can manage up to 31 connection points called SLAVES, such as:
- A remote unit with extension possibilities: a maximum of 6 extension units comprising of a
maximum of 8 analog input channels and 8 analog output channels
- A simple remote unit (without extension) with analog or binary inputs / outputs
- A remote TCAD display
- An ABB NCSA-01 variable speed drive interface
- A high speed counter unit
- A central unit (50 series with extension possibilities, 90 series and the previous 30 series)
- Or any other device which disposes of a CS 31 communication (see Figure 1-2).
Comment:
A slave fitted solely with binary channels occupies 1 connection point.
A slave fitted with binary and analog channels occupies 2 connection points of the available
31.
The maximum number of remote ANALOG units depends on the MASTER central unit:
- 50 series: - a maximum of 31 remote analog input units
- a maximum of 31 remote analog output units
- a maximum of 15 extensible remote units (ICMK14F1) with analog input / output
extensions + 1 remote analog input / output unit (15 x 2 + 1 = 31)
- or a mixed binary / analog configuration within the previous limits
- 90 series: - a maximum of 12 remote analog input units
- a maximum of 12 remote analog output units
- or a maximum of 12 slaves with analog extensions
Other Option: You have a possibility to use and configure the CS31 bus in Modbus® slave or
master see chapter 7 communication Modbus®
2.3. Cabling techniques
Connecting a central unit without a remote unit is simple and corresponds to normal electrical
standards. The electrical connections of a AC 31 system which consists of remote units,
notably where there are numerous electrical cubicles, should adhere to the obligatory rules.
These rules are presented in chapter 4.
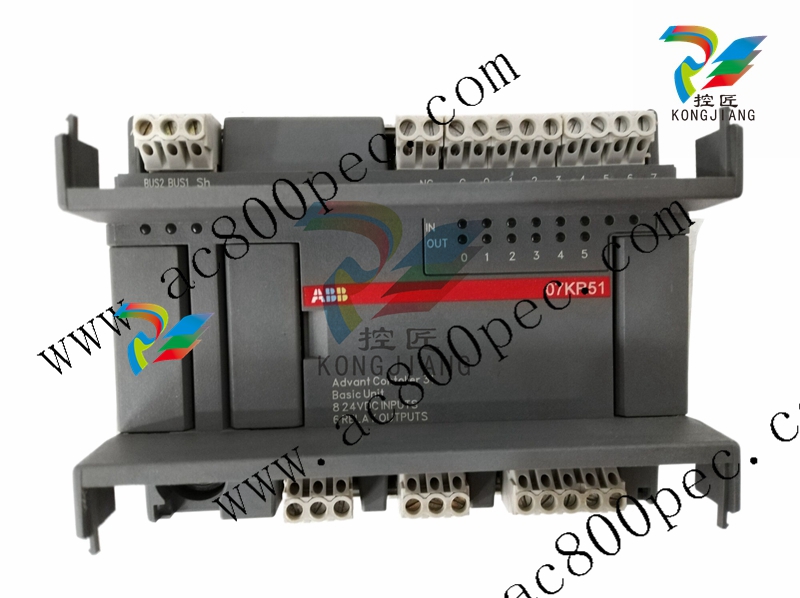
The 40 and 50 series central units memory is composed of two distinct areas:
- A SRAM memory where the user program and data is loaded.
- A Flash EPROM memory which contains:
- a backup of the user program with the program constants,
- the configuration data,
- and the system program protected against access from the user program.
An incorporated battery, which is available only in the 50 series, also enables the backup of
internal variables.
The user program is a set of universal functions conceived by the constructor to cover all
applications and ensure all the basic PLC functions. It is developed with the AC31GRAF
software. After being translated into instructions understable by the central unit it is loaded in
RUN or STOP mode into the SRAM and then saved from the SRAM to the Flash EPROM.
Thereby, at each program launch the user program, saved in the Flash EPROM, is copied to
the SRAM for processing by the microprocessor (Figure 1-3).
The structure of the system program memory, the user program, the inputs / outputs and
internal variables are described in the annex (mapping).
07CR41,24 V直流1SBP260020R1001
07CR41 120/230VAC1SBP260021R1001
07CT41 24VDC1SBP260022R1001
07KR51 24VDC 1SBP260010R1001
07KR51 120/230VAC1SBP260011R1001
07KT51 24VDC1SBP260012R1001
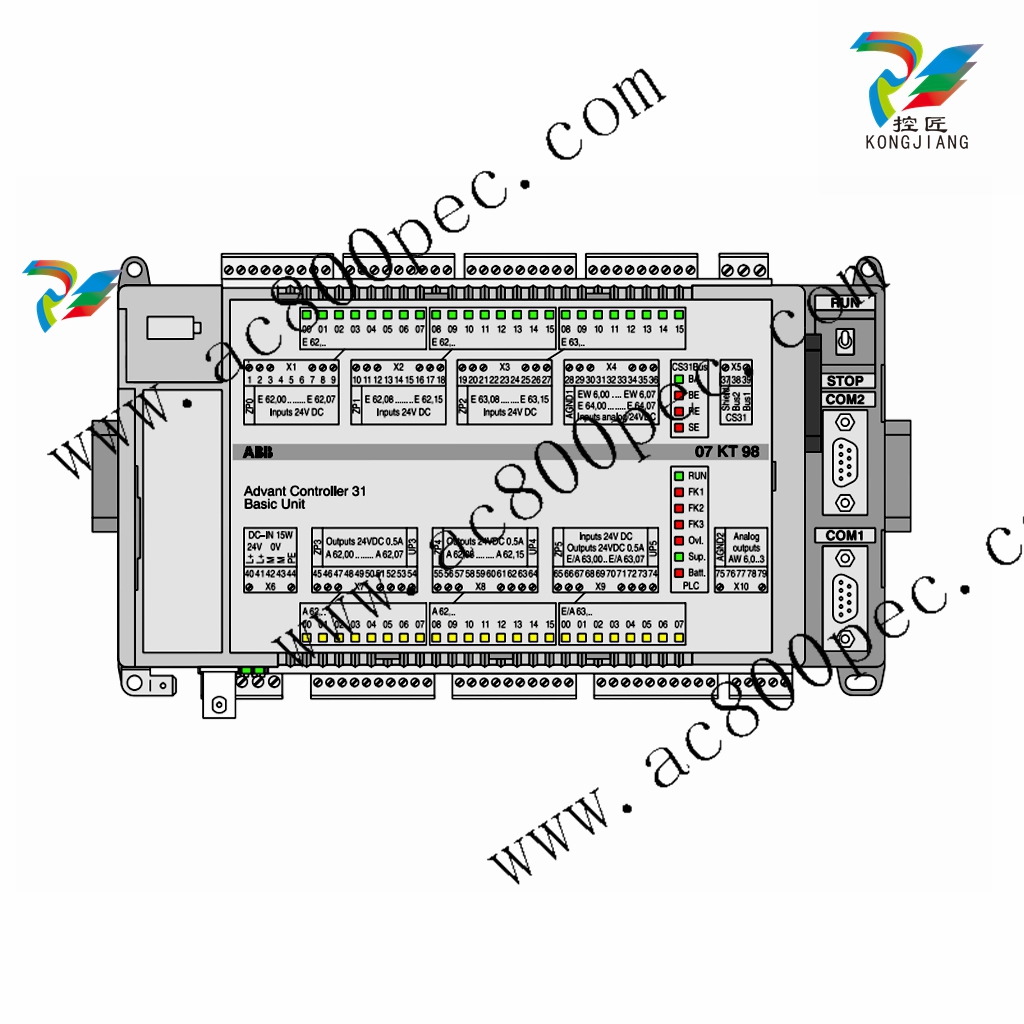
The central unit microprocessor ensures the cyclic execution of the system as shown in
Figure 1-4.
The internal processing:
- PLC monitoring and control
- and processing requests from the terminal operator,
is executed in parallel with the previously described cycle.
The main program is processed sequentially. It may call up to a maximum of 12 sub-programs.
Each sub-program may be called numerous times in the main program.
Three types of interruptions may be executed parallel to the main program:
- A cyclic interruption
- A warning interruption triggered by an event on the I 62.03 input
- A warning interruption triggered by an event on the I 62.02 input
The interruptions have priority over the main program execution. If all three interruptions are
triggered simultaneously then the interruption triggered by I 62.03 has priority over the I 62.02
input interruption which in turn has priority over the cyclic interruption. Once an interruption has
been launched it cannot be interrupted by another (Figure 1-5).
The execution duration of a cycle (bus cycle + program cycle) is controlled by the central unit.
Any excess of the cycle time defined by the user in AC31GRAF is signaled by the ERR Led, at
the front of the central unit, as of the first program cycle.
3.3. Bus transmission
The master central unit manages the transmission of messages to the various slaves over a
RS485 serial liaison.
The messages are transmitted under the following format:
- Request from the master central unit:
address data CRC8
- Request from the remote units:
start data CRC8
The messages always end with an end of frame control: checksum CRC8.
The length of the exchanged frames depends on the type of unit. Frames exchanged with an
analog unit are the longest.