ABB BSD Series
ABB Sace S.p.A. presents its new BSD servo system, a
compact, high-performance and easy product.
The BSD servo drive meets the needs of engineers, loo king for high-performance, easy and reliable products, and
buyers, who have lower and lower budgets to make their
products competitive in today’s selective market.
ABB: A “made in Europe” brand, worldwide identified as a
synonymous of reliability, quality and security. New BSD
servo system by ABB Sace: the perfect partner for any of
your application needs.
Range from 100 watt to 2 Kw
●Anti-vibration filter (patent pending)
Supply: 220 Vac
●Auto-tuning
.Compact servo system and high performances
●Automatic off-set adjustment
.Analog speed command +/-10 Volt
●Notch filters
Analog torque command +/-10 Volt
●Configurable simulated encoder output
Pulse train command up to 1 Mhz
●Software windows: BSD Configurator.
·Serial encoders from 131.072 pulses/turn (standard)
New serial encoders from
131.072 pulses/turn (standard)
Maximum accuracy, high performances and rotation linearity even at
minimum speed.
Anti-vibration filter
A complex algorithm (patent pending) which reduces vibrations to
the minimum.
Autotuning
Easy and automatic tuning of
the drive. A piece of cake!
Integrated brake chopper
BSD Configurator
Easy and straightforward software for servo drive control with
digitizing oscilloscope function.
Special input for torque
control
To make electric screwdrivers,
unwinders, test machines, etc.
Motor control is now improved thanks to the more than 131,000
pulses generated by the new-generation serial encoder. Accuracy in
positioning and interpolation are outstanding.
Encoder at 8192 pulses
Encoder at 131,072 pulses
Vibration
Steady
Positioning is faster because the axis do not swing during the stop
phase. This also improves the interpolation phase because axis and
machine structure are more stable.
Encoder from 131,072 pulses/turn:
great accuracy
Vibrations are reduced by means of
the inbuilt filter
New BSD Series A complete range, reliable and easy to use; guaranteed by ABB.
• Jog Function through keyboard: useful to test the wiring
and mechanical coupling
• Notch filter for the elimination of resonances.
• Side by side mounting: no mandatory space between the
drives (size1)
• Possible pulse train command: technology shift from
step-by-step to brushless motor
• Power and electronic supplies are separated
• Compliant with CE, UL, cUL and Rhos
Drive BSD General Specifications
Code BSD0100 BSD0200 BSD0400 BSD0750 BSD1000 BSD1500 BSD2000
Power [W] 100 200 400 750 1000 1500 2000
Weight [Kg] 1 1,5 2,5
Power supply Method Single-phase Single-phase/
3-phase 3-phase
Tension from 170 to 253 [Vac] (3-phase) - from 180 to 253 [Vac] (single-phase)
Frequency 50 / 60 [Hz]
Electronic supply Method Single-phase
Tension from 170 to 253 [Vac]
Frequency 50 / 60 [Hz]
Control method IGBT PWM sinusoidal
Feedback Serial encoder in 17 bits - 131.072 actual pulses
Digital input functions
(1) Servo drive ON (2) Positive Overrun (3) Negative Overrun (4) Emergency stop (5) P - Action (6)
Freewheel stop (7) Notch filter selection 1 (8) Notch filter selection 2 (9) Control system change (10)
External resistor overheating (11) Alarm reset
Digital output functions
(1) Servo drive ready (2) Positioning process completed (3) Servo drive in alarm state for external contact [A]
(4) Servo drive in alarm state for external contact [B] (5) Dynamic braking in progress (6) Overrun Security
Action (7) Servo drive stopped for emergency (8) Deviation zero (9) Speed Zero
(10) Achieved Current limit (11) Brake Timing
Simulated encoder Selectable range Free configuration of output pulses from 16 to 32768 pulses/turn
Signal type (1) 5 Volt TTL line drive fase A - Fase B e fase Z - (2) 24 Vdc open collector fase Z
Analog speed command Control range From 1 to 5000
Command signal Analog command with reference +/- 10 Volt : maximum value at 10 volt can be set by a specific parameter
Preselectable speed 3 preselectable speeds can be set, operated by digital inputs
Analog control command Command signal Analog command with reference +/- 10 Volt : maximum value at 10 volt can be set by a specific parameter
Toque limit CW / CCW A clockwise torque limit and a counterclockwise torque limit can be set by a specific parameter
Pulse train command Command max. frequency 1Mhz 5volt ttl line drive , 200 khz 24 volt open collector
Signal form Rs 422 line drive and 24 volt open collector
Command type (1) step and direction , (2) CW direction and CCW direction, (3) 2 channels shifted 90° in phase
Product compliances Standards Compliant with UL /cUL (UL508c) and CE (Low voltage directive EN50178)
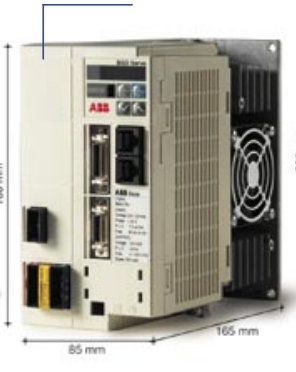
Technical specifications for servomotors BSM without brake
Low inertia 3000 Rpm Medium inertia 2000 Rpm
Motor type BSM0100CN00 BSM0200CN00 BSM0400CN00 BSM0750CN00 BSM1000CN01 BSM1500CN01 BSM2000CN01
Power [Watt] 100 200 400 750 1000 1500 2000
Rated torque [Nm] 0,32 0,64 1,27 2,39 4,77 7,16 9,55
Max. torque [Nm] 0,96 1,91 3,82 7,17 14,3 21,5 28,6
Rated speed [r/min] 3000 2000
Max speed [r/min] 5000 3000
Torque [Kg*cm2] 0,037 0,13 0,24 0,85 15,14 22,33 29,51
Rated current [A] 0,85 1,5 2,7 4,8 6,4 10 12,3
Max current [A] 2,55 4,5 8,1 14,4 19,2 30 36,9
Motor shaft Equipped with key
Feedback Incremental Serial Encoder from 131.072 pulses/tour - 17 bits
Vibration resistance 5 g = 49 m/s2
Weight [Kg] 0,55 1,2 1,8 3,4 7,5 9,8 12
Technical specifications for BSM servomotors with brake
Low inertia 3000 Rpm Medium inertia 2000 Rpm
Motor type BSM0100CB00 BSM0200CB00 BSM0400CB00 BSM0750CB00 BSM1000CB01 BSM1500CB01 BSM2000CB01
Braking torque [Nm] 0,34 1,27 2,45 17
Torque [Kg*cm2] 0,04 0,34 0,45 1,2 17,2 24,4 31,6
Excitation voltage[V] 24 Vdc
Attraction time [ms] 35 40 60 120
Release time [ms] 10 20 25 30
Brake power [Watt]] 6,1 7,3 8,5 14
Weight [Kg 0,7 1,7 2,3 4,2 10,5 12,8 15