GE IC697MDL241 240 VAC Isolated Input (16 Points)
12. The bus configuration screen, as shown asright, includes two Bus Controllers. One, in
this example the one at Bus Address 31, is
the internal Bus Controller that was just
configured. The second, here the one at
Bus Address 30, is the Bus Controller in the
other PLC.
13. If the two Bus Controllers will exchange
Global Data, select the other Bus Controller
and press F10 (zoom) A configuration
screen appears. Enter the Global Data parameters on the configuration screen.
Press ESC to return to this bus configuration screen.
14. Configure the other Bus Addresses. Here,
discrete blocks have been located at Bus
Addresses 28 and 29.
15. Press ESC again to return to the rack display.
16. From the rack configuration screen, select
the other Bus Controller. Press F10 (zoom)
to display its bus configuration screen.
17. Notice that this Bus Controller has the
same Bus Address (31 in this example) as
the other internal Bus Controller. The second Bus Controller shown here is the external Bus Controller.
18. Notice also that the redundant devices
have been copied to this bus. If the Bus
Controllers will exchange Global Data,
zoom into the Bus Address of the external
Bus Controller and enter its parameters.
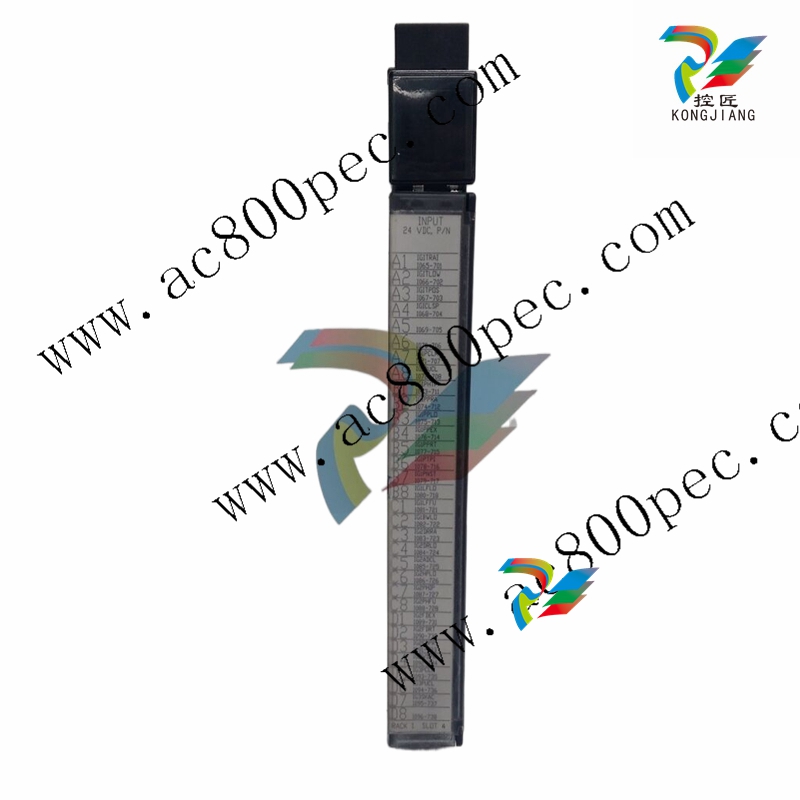
This chapter describes the following diagnostics capabilities of interest in Series 90–70
PLC systems that use Genius I/O and communications:
Relevant system status references.
Fault and No Fault Contacts, which can be used with program references or with the
built–in fault–locating references.
High Alarm and Low Alarm Contacts, which will indicate when an analog reference
has reached one of its alarm limits.
Display and clearing of Genius faults from the programmer I/O Fault Table. I/O Table
faults related to the Bus Controller and Genius devices are listed at the end of the
chapter.
For Additional Information, Also See:
Chapter 1 for an overview of Genius fault reporting.
Chapter 5, which describes the use of Read Diagnostics, Clear Circuit Faults, and Clear
All Circuit Faults COMREQs (Communication Requests).
Chapter 6 to learn how the Bus Controller’s redundancy capabilities can optionally be
utilized to check its I/O and diagnostics data memory when it is not used with a dual bus
or as a dual controller.
System status references are pre–defined locations and nicknames. They can be in cluded in an application program to check for fault–related conditions. The following
system status references are of special interest for a system with a Bus Controller:
Reference Nickname Conditions Indicated When Set
CFG_MM
LOS_RCK
LOS_IOC
LOS_IOM
ADD_RCK
ADD_IOC
ADD_IOM
IOC_FLT
IOM_FLT
SFT_IOC
MAX_IOC
IO_FLT
IO_PRES
IO_FULL
System Configuration Mismatch
Loss of Rack
Loss of Bus Controller
Loss of I/O module
Addition of Rack
Addition of Bus Controller
Addition of I/O module
Bus fault or Bus Controller fault
I/O module fault
Bus Controller software failure
Too many Bus Controllers (maximum is 31)
I/O fault occurred
Fault logged into I/O Fault Table
I/O Fault Table is full
These references and their Nicknames can be used like any other type of reference. For
more information, see the Logicmaster 90 Software Reference Manual.
Example:
A PLC system includes one Bus Controller. During CPU configuration, the system status
fault LOS_IOC has been designated a diagnostic (rather than fatal) fault. LOS_IOC rep resents loss of the Bus Controller;
if this occurs, the Loss of IOC fault will be placed in the
I/O Fault Table. In this example, the application program also monitors the LOS_IOC
reference. If this reference is set, the contact passes power flow to an output coil, which
energizes a warning light on an operator panel.