GE IC697MDL651 5 VDC (TTL) Input (32 Points)
Fault and No Fault contacts can be used to detect fault or lack of fault conditions on a
discrete (%I or %Q) or analog (%AI or %AQ) reference, or they can be programmed with
the Series 90-70’s built-in fault-locating references (see below). Unless they are used
ONLY with fault-locating references, fault memory for their use must be set up using
the CPU Configuration functions of the Logicmaster 90-70 software.
A Fault contact will detect a fault in a discrete or analog input or output, or a hardware
component of the system. The contact passes power flow if the reference has a fault.
Example:%AI0034 %M00053
When used with a %I, %Q, %AI, or %AQ reference, a fault associated with the
–[F AULT]– contact must be cleared to remove it from the fault table and stop the con tact passing power flow.
Clearing such a fault with a Hand–held Monitor does not remove it
from the fault table or stop the contact passing power flow.
No Fault Contacts will also detect faults in discrete or analog inputs and outputs. A No
Fault Contact passes power flow if its associated reference does not have a circuit fault.
Example:
%I00167 %Q00168
Fault Locating References
Both Fault and No Fault contacts can be programmed with fault–locating references to
identify faults associated with system hardware. These fault references are for informa tional purposes only.
The PLC does not halt execution if one of these reference faults
occurs. For a Genius device, the format of the fault–locating reference is M_rsbmm,
where r is the rack number 0 to 7, and s is the slot number of the Bus Controller; b is the
bus number, and mm is the Device Number (serial bus address) of the affected Genius
device (00 to 31). For example, M_46128 represents rack 4, slot 6, bus 1, module 28. For
more information about fault–locating references, please refer to the Logicmaster 90–70
Software User’s Manual.
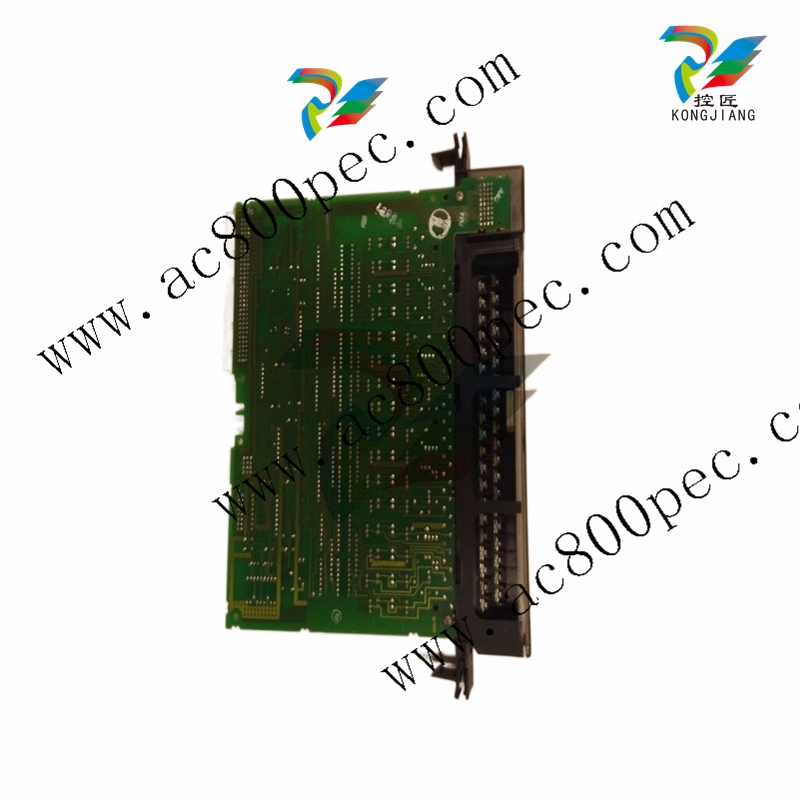
The I/O Fault Table can contain up to 32 faults. Additional faults cause the table to over flow, and faults are lost.
The system reference IO_FULL (%S00010) is set to indicate that
the fault table is full.
As faults occur, the first 16 are logged into the table and remain there until the table is
cleared again; none of these 16 faults will be dropped if the table overflows. For faults 17
through 32, the Fault Table operates as a First–In–F irst–Out stack. When fault 33 oc curs, fault 17 is dropped from the table.
Clearing the Fault Table removes all the fault
listings.
Fault 1
Fault 16
Fault 17
Fault 33
Faults overflow here
New faults are added here
Clearing Faults
You must clear the I/O Fault Table from Logicmaster 90 for the fault to be cleared in the
PLC CPU and for the associated fault contact to be cleared. Clearing faults with a Hand–
held Monitor alone does not remove them from the Fault Table, or cause any associated
–[F AULT]– contacts to stop passing power flow.
Clearing the Fault Table causes the Bus Controller to send a Clear All Circuit Faults back ground message to all blocks on the bus.
Faults can be cleared from the Fault Table ei ther from the programmer screen or by the application program.
Clearing the fault table removes the faults it contains; it does not clear fault conditions in
the system. If the condition that caused a fault still exists and is detected, the fault will
be reported again.
Removing I/O Force Messages from the I/O Fault Table
When a point is forced on a Genius block with a Hand–held Monitor, a fault is regis tered in the Series 90 I/O Fault Table.
Subsequent forces on the same block do not gen erate additional messages. Only when all forces are removed from the block does the
Bus Controller log an Unforce message in the I/O Fault Table.
Loss of Device Faults Caused by High Bus Error Rate
If the bus is experiencing a high error rate (possibly due to electrical interference or
damaged cable), Loss of Device faults may be logged into the Fault Table. Loss of Device
faults that are logged in conjunction with I/O Bus Faults can be usually be attributed to
the poor quality of the bus installation. The condition causing the bus errors should be
corrected as soon as possible.