GE IC697VDR151 Relay Output, Non-latching
Note: A given feature may not be implemented on all PACSystems CPUs. To determine whether afeature is available on a given CPU model and firmware version, please refer to the Important
Product Information (IPI) document provided for the CPU version that you are using.
Rev Date Description
U Nov-14 New Appendix (A-3.6) EGD Sweep Impact for Embedded Eternet Interface on
RX3i CPE 305 and 310.
T Oct-14 Support for OPC UA using embedded Ethernet port in CPE305/CPE310 with CPU
firmware 8.20.
Support for Ethernet Global Data (EGD Class 1) using embedded Ethernet port in
CPE305/CPE310 with CPU firmware 8.30 Sweep impact of EGD on Embedded
Ethernet interface. Direct replacement for S90-30 IC693CPU374.
New communications capabilities provided by:
o IC695PNS001 – PROFINET Scanner Module
o IC695GCG001 – Genius Communications Gateway via PROFINET
o IC695EDS001 – Ethernet based DNP3 Outstation
S July-13 Support for Modbus/TCP Server, SRTP channels and Modbus/TCP client channels
on RX3i CPE305/CPE310 embedded Ethernet interface – Chapter 2 & Chapter 12
Support for Access Control List – Chapter 3and Chapter 14
Modbus TCP/IP mapping for CPE305/CPE310 – Chapter 3
Enhanced Security Passwords and OEM Protection – Chapter 4
Serial I/O protocol enhancements (Data Set Ready, Ring Indicator, and Data
Carrier Detect) – Chapter 13
Diagnostics for PROFINET alarms and PROFINET network faults, including
#PNIO_ALARM, SA0030 – Chapter 6 and Chapter 14
Instruction executions times measured for RX3i CPU320/CRU320 – Appendix A
Sweep impact times for new modules: IC694MDL758, IC694APU300-CA and
later, IC695PNS001, IC694ALG442, IC694ALG220, IC694MDL645 and
IC694MDL740 – Appendix A
earlier Added instructions for replacing the RX3i CPE305/CPE310 real-time clock
battery: Chapter 2
Corrected definitions of reverse acting and direct acting modes for PID functions
– Chapter 10
Expanded data for Boolean execution measurements – Appendix A
Re-instated instruction times for RX7i CPE/CRE030/040 release 6.0 as published
in version Q of the manual (unintentionally omitted from version R) – Appendix A
Compatibility information for volatile memory backup batteries has been
consolidated in the PACSystems Battery and Energy Pack Manual – throughout
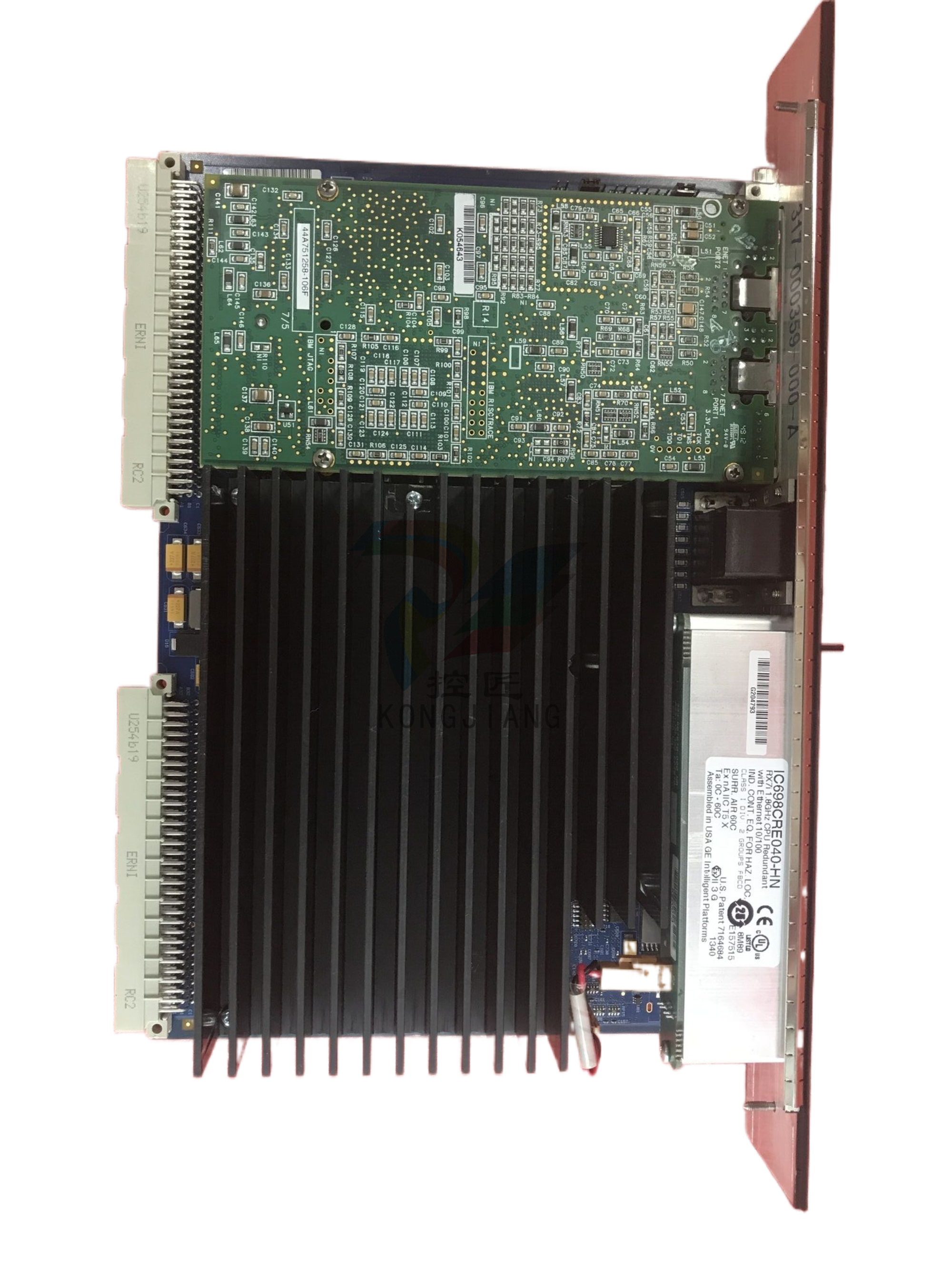
1.2. PACSystems Control System Overview
The PACSystems controller environment combines performance, productivity, openness and
flexibility. The PACSystems control system integrates advanced technology with existing systems. The
result is seamless migration that protects your investment in I/O and application development.
1.2.1 Programming and Configuration
Proficy* Machine Edition programming software provides a universal engineering development
environment for all programming, configuration and diagnostics of PACSystems. A PACSystems CPU
is programmed and configured using the programming software to perform process and discrete
automation for various applications. The CPU communicates with I/O and smart option modules
through a rack-mounted backplane. It communicates with the programmer and/or HMI devices via
the Ethernet ports or via the serial ports 1 and 2 using Serial I/O, or Modbus RTU slave protocols.
1.2.2 Process Systems
PACSystems CPUs with firmware version 5.0 and later support Proficy Process Systems (PPS). PPS is a
complete, tightly integrated, seamless process control system using PACSystems, Proficy HMI/SCADA,
and Proficy Production Management Software to provide control, optimization, and performance
management to manage and monitor batch or continuous manufacturing. It delivers the tools
required to design, implement, document, and maintain an automated process. For information
about purchasing PPS software, refer to the Support website