GE IC698CHS117 RX7i 18 VME Slot Rack, Front Mount
Only one diagnostic message can be sent during any bus scan. If a fault message hasalready been sent (by another device) during that scan, a device saves its own diagnostic
message until the next available bus scan. For example, if the communications token is
currently at device 2, and faults occur at devices 3 and 4 at the same time, device 3 can
send its diagnostic message if another message has not already been sent. Device 4 must
wait at least one more bus scan to send its diagnostic message.
The Bus Controller stores any diagnostic messages it receives. They are read automati cally by the Series 90–70 CPU.
Faults may then be displayed in the fault table using the
Logicmaster 90–70 software and cleared from the programmer. Details are in chapter 4.
A Genius Hand–held Monitor can also be used for diagnostics and fault clearing.
In addition the built–in diagnostics capabilities of Genius devices, the Logicmaster
90–70 application program can make use of additional diagnostics mechanisms pro vided by the Series 90–70 PLC:
System Status References that have been defined for Genius use.
Fault and No Fault contacts that can be used to detect fault and lack of fault condi tions.
Alarm contacts that can be used to indicate when an analog value has reached an
assigned alarm limit.
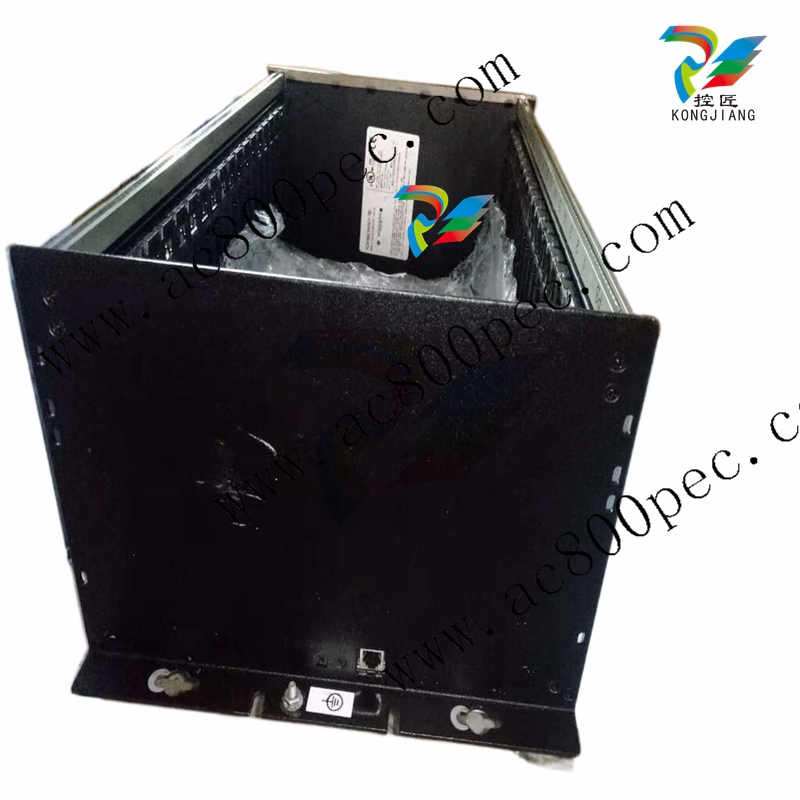
Datagram Type Type Description
Read ID Requests identifying information from a device on the bus.
Read ID Reply The automatic response to a Read ID datagram.
Read Configuration Requests configuration data from a device on the bus.
Read Configuration Reply The automatic response to a Read Configuration datagram.
Write Configuration Sends configuration data to a device on the bus.
Assign Monitor Commands a device on the bus to direct an extra copy of each Fault
Report to another device on the bus.
Read Diagnostics Requests diagnostics data from a device on the bus.
Read Diagnostics Reply The automatic response to a Read Diagnostics datagram.
Write Point Sends up to 1 word of bit data to a Series Six or Series Five PLC, or
to a host computer.
Read Block I/O Requests I/O data from some types of Genius blocks.
Read Block I/O Reply The automatic response to a Read Block I/O datagram.
Report Fault An automatic diagnostic message received from a device on the bus.
Pulse Test Commands a discrete block to pulse its outputs.
Pulse Test Complete Automatic indication that outputs have been pulsed.
Clear Circuit Fault Clears one specific circuit fault.
Clear All Circuit Faults Clears all circuit faults on bus devices.
Switch BSM Causes a Bus Switching Module to switch to alternate bus, if operational.
Read Device Reads up to 128 bytes of CPU data via another Bus Controller.
Read Device Reply The response to a Read Device datagram.
Write Device Sends up to 128 bytes of data to a CPU, via its Bus Controller.
Read Data Requests temporary data from a High–speed Counter block.
Read Data Reply The automatic reply to a Read Data datagram.
Write Data Sends temporary data to a High–speed Counter block.
Read Map Requests the I/O map configuration of a Remote I/O Scanner.
Read Map Reply Automatic response to a Read Map datagram.
Write Map Sends I/O map configuration to a Remote I/O Scanner.
Additional datagrams, not listed above, are sent as system messages; they do not involve
any application programming. The Genius I/O System User’s Manual explains datagrams
in detail. It also shows the formats of the data that is transferred by datagrams.
In the application program, COMREQ instructions are used to send datagrams and to
read any unsolicited datagrams that have been received. See chapter 5 for instructions.