GE IS200TRLYS1B 12 Form C mechanical relays w
The following CPUs support a feature that permits an Ethernet LAN to be configured for use as a
PROFINET Controller:
• RX3i CPE400
• Rx3i CPE330 (firmware version 8.90 or later required)
• RSTi-EP CPE10010
If the Embedded PROFINET Controller feature is to be configured, it must be configured on LAN2 for
RX3i CPE400, CPE330 and RSTi-EP CPE100. In the case of RX3i CPE400 and RSTi-EP CPE100, which are
Standalone CPU’s, this will be its only PROFINET Controller. In the case of CPE330, the Embedded
PROFINET Controller can co-exist with any rack-mounted PROFINET Controllers (IC695PNC001)
present in its CPU rack.
To enable the Embedded PROFINET Controller in a project in Proficy Machine Edition11, select the RX3i
CPE400 (or CPE330) or RSTi-EP CPE100 target in the PME Navigator (Figure 1) and open the Hardware
Configuration. On the Settings tab, change the designated LAN Mode of the selected port to
PROFINET. The PROFINET Controller node description then displays that a PROFINET node exists on
the selected LAN. For further details, refer to the PACSystems RX3i & RSTi-EP PROFINET IO-Controller
User Manual, GFK-2571G or later.
Figure 1: Configuring an Embedded PROFINET Controller
A PROFINET configuration may be transferred between a PROFINET Controller module (IC695PNC001)
and the target Embedded PROFINET IO-Controller using the cut / copy / paste functions in Proficy
Machine Edition.
The Embedded PROFINET Controller may be configured as a Simplex PROFINET IO-Controller with
support for up to 32 I/O devices. For update rates, loading and other considerations, refer to the
PACSystems RX3i PROFINET IO Controller User Manual, GFK-2571F or later.
10 Proficy Machine Edition™ (PME) 9.50 SIM 4 or later is required in order to configure the MRP parameters for CPE100.
11 Proficy Machine Edition Logic Developer PLC 8.60 SIM 13 or 9.00 SIM 4 or later is required for configuration of the
Embedded PROFINET Controller function.
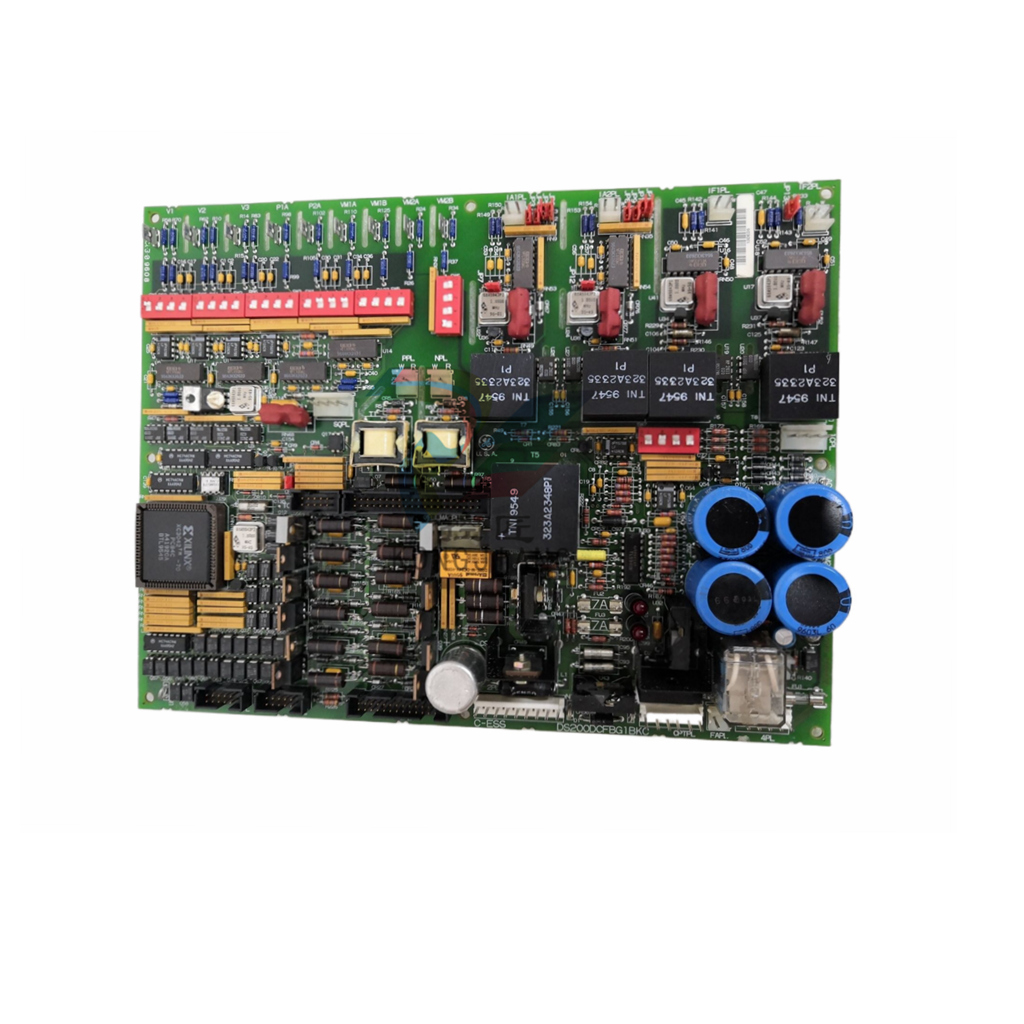
Each PACSystems CPE305/CPE310/CPE330/CPE400 supports Open Productivity and Connectivity
Unified Architecture (OPC UA) Server12 communications on the embedded Ethernet port only.
For more information on OPC UA support refer to PACSystems RX7i, RX3i and RSTi-EP TCP/IP Ethernet
Communications User Manual, GFK-2224 version M or higher (Chapter 10).
Note: Effective with CPE310/CPE305 Firmware Release 8.20, the CPE embedded Ethernet port
supports OPC UA Server.
Effective with CPE310/CPE305 Firmware Release 9.20 and CPE330 Firmware Release 9.21,
OPC UA Server is configurable through Proficy Machine Edition13
2.1.8 Removable Data Storage Devices (RDSDs)
The RX3i CPE305/CPE310/CPE330/CPE400 and RSTi-EP CPE100 CPUs14 provide the ability to transfer
applications to and from Removable Data Storage Devices (RDSD). Typically, these are
USB-compatible devices, such as a memory stick, smart phone, digital camera or an MP3 device.
Once the data is copied to the RDSD, it can be written to other RX3i / RSTi-EP CPUs of the same type.
In order to copy using RDSD, no PME programming software is needed. The RDSD interface requires a
user-supplied flash memory device that complies with the USB 2.0 Specification.
The USB port must be enabled in the RX3i / RSTi-EP configuration in order to transfer data between
the CPU and the RDSD. The compatible CPUs are shipped with the RDSD (USB) port enabled.
The RDSD load and store operations can include the following data:
▪ An entire application, including logic and configuration, reference table data, and cam files for
Motion applications. (Motion files and local logic for DSM motion applications are supported.)
Configuration can include Ethernet Global Data and Advanced User Parameters for the rack based Ethernet interface.
(Although a complete, unmodified application must be placed on the
RDSD, you can use an options.txt file to download selected components of the application to the
target CPU.)
▪ Passwords and OEM key, if any, are encrypted and written to the RDSD when the project is
loaded from the CPU. When the project is stored to a CPU that has no passwords or OEM key,
those are copied to the CPU.
Note: With Enhanced Security enabled, the RDSD update will fail if the RDSD source controller
has Level 4 password protection and the destination controller is password protected,
regardless of whether the passwords match.
With Legacy security, when the project is stored to a CPU that has passwords and/or
OEM key, the passwords must match or the store will fail.
▪ Fault tables are written to the RDSD before and after a load to or store from the RDSD.
▪ If a hardware configuration that disables the USB port is successfully stored to the CPU, the fault
tables will not be written to the RDSD at completion of the store operation.
Note: The USB port is for transfer of application data only. It is not intended for permanent
connection. Do not leave RDSD devices connected during normal operation.