ABB PFSK151 3BSE018876R1 Flatness measurement processing unit
1.7 Maintenance and troubleshooting
1.7.1 Introduction to maintenance and trouble shooting
General
The robot requires only a minimum of maintenance during operation. It has been
designed to make it as easy to service as possible:
• Maintenance-free AC motors are used.
• Grease used for all gearboxes.
• The cabling is routed for longevity, and in the unlikely event of a failure, its
modular design makes it easy to change.
Maintenance
The maintenance intervals depend on the use of the robot, the required maintenance
activitiesalso depends on selected options. For detailed information on maintenance
procedures, see Maintenance section in the Product Manual - IRB 1200.
1.8 Robot motion
1.8.1 Working range and type of motion
Robot motion
IRB 1200-5/0.9 IRB 1200-7/0.7 Type of motion Location of
motion
+170° to -170° +170° to -170° Rotation motion Axis 1
+130° to -100° +135° to -100° Arm motion Axis 2
+70° to -200° +70° to -200° Arm motion Axis 3
+270° to -270° +270° to -270° Wrist motion Axis 4
+130° to -130° +130° to -130° Bend motion Axis 5
Default: +400° to -400°
Maximum revolution: ±242i
Default: +400° to -400°
Maximum revolution: ±242i
Turn motion Axis 6
i The default working range for axis 6 can be extended by changing parameter values in the software.
Option 610-1 Independent axis can be used for resetting the revolution counter after the axis has
been rotated (no need for "rewinding" the axis).
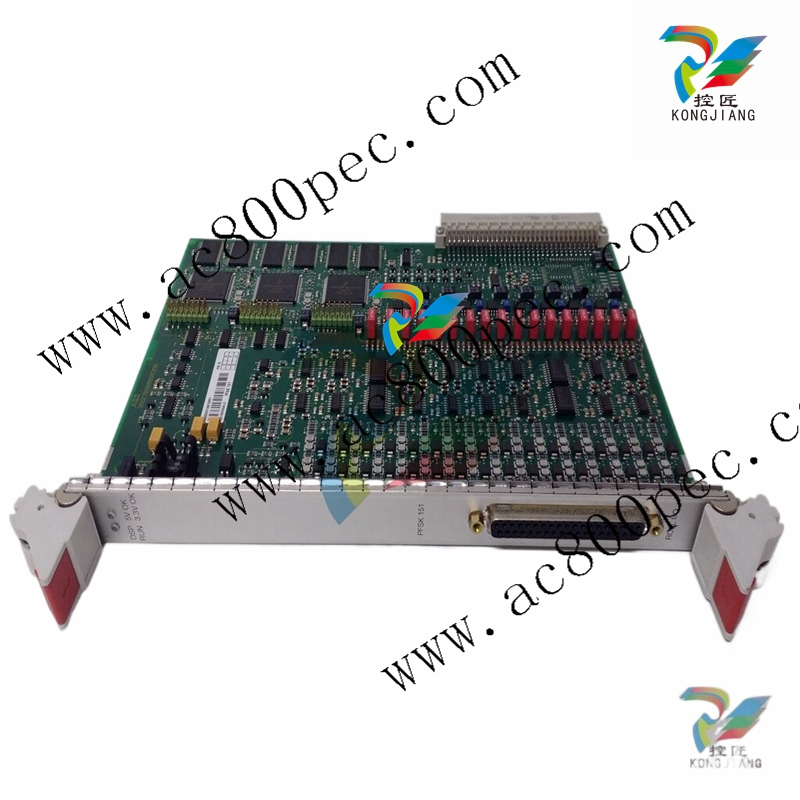
At rated maximum load, maximum offset and 1.6 m/s velocity on the inclined ISO
test plane, with all six axes in motion. Values in the table below are the average
result of measurements on a small number of robots. The result may differ
depending on where in the working range the robot is positioning, velocity, arm
configuration, from which direction the position is approached, the load direction
of the arm system. Backlashes in gearboxes also affect the result.
The figures for AP, RP, AT and RT are measured according to figure below.
xx0800000424
Description Position Description Position
Programmed path E Programmed position A
Actual path at program execution D Mean position at program
execution
B
Max deviation from E to average path AT Mean distance from pro grammed position
AP
Tolerance of the path at repeated
program execution
Tolerance of position B at re- RT
peated positioning
RP
Values Description
IRB 1200-7/0.7 IRB 1200 - 5/0.9
0.02 0.025 Pose repeatability, RP (mm)
0.02 0.02 Pose accuracy, AP (mm)
0.02 0.07 Linear path repeatability, RT (mm)
0.77 0.53 Linear path accuracy, AT (mm)
0.057 Pose stabilization time, Pst (s) within 0.1 mm of the 0.113
position