ABB PP836A 3BSE042237R2 HMITouch Screen
To read more about AC 800M's INFI 90 evolutionary library, please refer to the
INFI90 Function Code Library for AC 800M-Application Overview, 3BUS094839.
S800 I/O-Harmony Termination Unit(TU)prefabricated cables. To minimize
the risk and costs of re-terminating field wires, ABB has created a family of cables
that preserves the investments made in standard Harmony field wiring terminations.
These prefabricated cables allow for the I/O module upgrade to S800 I/O without
ever touching the field wires. The cables are used in place of the traditional NKTU
cables. They connect the existing TU to S800 I/O modules via standard cable plug-ins.
S800 I/O cables exist for 24 VDC Digital I/O, 4-20 mADC Analog I/O, TC, mV, RTD I/O
(ASM01, ASM02, and ASM03) termination units. Similar solutions exist for Harmony
Block bases (AIN, AOT, DIN, and DOT).
Whether replacing aging PLCs or incrementally upgrading older Network 90/INFI 90
based controllers, especially AMM, LMM, COM, and MFC modules, these control evolution
products allow for seamless evolution to AC800M-S800I/O without the costs and risks
associated with “rip-and-replace" controller upgrade methods (summarized in Table 5).
Traditional"Rip and Replace" Upgrades
ABB INFI90FCLib for AC 800M upgrades
Re-engineering or translation of control
Minimal to no engineering required
applications
New algorithms result in new process
Process control is same as before
control behaviors
Long commissioning and start-up periods
Minimal commissioning and start-up
(re-configuration and re-tuning of loops)
(no re-tuning of loops)
Create new documentation
Documentation converted and enhanced
Results in:
Results in:
Greater loss of production
· Minimal loss of production
Increased risk
●Minimal risk
.Higher project costs
●Lower project costs
Table 5.By avoiding high project costs and production risks, ABB control evolution upgrades
cost 60-80% less than *rip-and-replace" altematives
System 800xA's Device Management features (Figure 23) lower lifecycle costs through
significant savings in the design, implementation, and operation of field equipment.
The harnessing of untapped potential from the substantial installed base of HART
devices conforms with the ARC Advisory Group analysis that: “Users can employ many
of their HART field devices with new generation automation architectures, making the
migration to a new process automation system more economical while increasing the
availability of intelligent data that has long been under utilized."
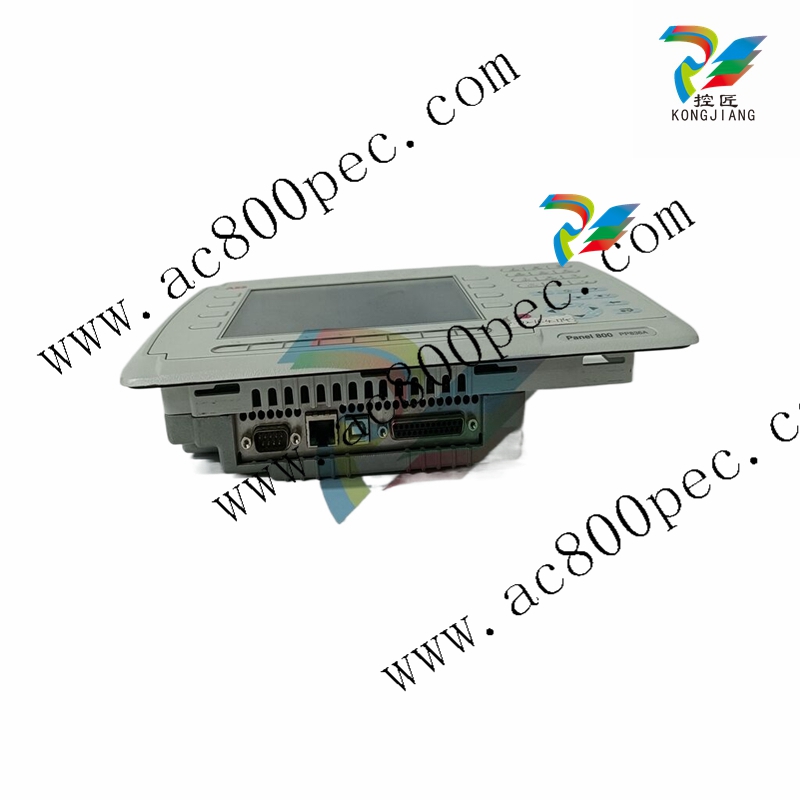
Digital information from HART devices is accessed by the System800xA Fieldbus
Management tools that physically connect to HART multiplexer units. These
multiplexers receive HART device data by cable connections from standard Harmony
Termination Units (Figure 24). ABB's HART solution supports device parameterization
and remote monitoring of signal status and process variables. It also supports
diagnostic information through use of device specific Device Type Managers (DTMs),
which are supplied by the respective device manufacturers. In addition, the tight
integration of HART devices within Harmony enables improved device maintainability
through asset monitoring and optimization.
HART muhiplexer
Harmony HART
Concentanor
-nason um
Existing leid wiring
VOMadule
Existing Harmony
Figure 24. Simple Cable Connections Provide Access to System's Smart Device's HART Data
FoUNDATION Fieldbus and Profibus interfaces are available through the System800xA AC
800M controller.
For more details, please refer to the System800xA Device Management Overview,
3BDD013081.
With access to installed HART field device information, Harmony system owners
can take full advantage of System 800xA's Asset Optimization features. The application
(Figure 25) exploits the wealth of field resident information accessible through
HART/ Fieldbus and higher-level systems to access and document equipment
conditions in real-time. In addition to field devices, System 800xA asset monitoring
features inspect the health and status of the operations network, including networking
equipment such as PCs, routers, printers, etc. These functions enable personnel to
implement proactive and predictive maintenance services. Additionally, the software
seam lessly integrates plant maintenance and calibration management systems to
greatly reduce the time to repair through streamlined work processes.