GE VMIVME-2510B_64_Bit IO board
NOTICE – Equipment damage. When handling electronic parts and assemblies, it isnecessary that proper electrostatic discharge (ESD) precautions be taken (i.e., wear an ESD
wrist strap with a grounding cable and use an ESD shielded bag to protect items removed).
2.1 Analyzer location
The analyzer should be located as close to the sample stream as practical. The analyzer must be
installed in a shelter or area protected from direct sunlight and harsh weather. It is recommended that
a minimum clearance of six inches be allowed on each side of the analyzer panel to allow for making
the necessary connections.
The analyzer must be mounted so that it is level.
The analyzer should be adequately supported during mounting since its approximate weight is 90 kg
(200 pounds). Connections should not be made to the analyzer until it is mounted securely in place.
The atmospheric exhaust (detector cell vent) must be an atmospheric vent.
2.1.1 Master controller
The Master Controller contains a Mounting Plate with a Single Board Computer (SBC), a Power Supply,
one or more SBC CAN Interface Cards, and optional Wago input/output modules. The front panel
assembly has a liquid crystal display (LCD), keypad, and front panel board.
The Master Controller can be located up to 100 meters (328 feet) from the associated oven. The
Master Controller communicates with the oven through a fiber optic cable. The customer is responsible
for locating the Master Controller in accordance with the customer-specified area classification
indicated on the nameplate.
When determining where to install the Master Controller, consider the following location criteria:
Installation must be a pollution degree 2 environment or better
Electromagnetic compatibility
Area classification indicated on the nameplate
Equipment ingress protection is IP54
Protection from rain, direct sunlight, temperature extremes
Ambient operating temperature is 0 to 50 degrees C (32 to 122 degrees F)
Avoid exposure to corrosive gas
Not intended for a combustible dust environment
Not intended for below surface mining applications
Free from dust and static electricity
Space of at least 152 mm (6 inches) to the right side of the Master Controller if purge
equipped
Space of at least 610 mm (24 inches) in front of the Master Controller for servicing
Space of at least 279 mm (11 inches) above the Master Controller if x-purge is utilized
2.1.2 Master controller as an RUI
The Master Controller as an RUI contains a Mounting Plate with a Single Board Computer (SBC) and a
Power Supply, with no SBC CAN Interface Cards and no Wago input/output modules. The front panel
assembly has a liquid crystal display (LCD), keypad, and front panel board.
The Master Controller as an RUI can be located anywhere that has access to an Ethernet connection.
The customer is responsible for locating the Master Controller in accordance with the customerspecified area
classification indicated on the nameplate. When determining where to install the Master
Controller as an RUI, use the same location criteria as a regular Master Controller.
2.1.3 Ovens
Locate the ovens as close to the stream to be sampled as practical. The customer is responsible for
locating oven(s) in accordance with the customer-specified area classification indicated on the
nameplate.
When determining where to install the oven, include the following location criteria:
Installation must be a pollution degree 2 environment or better
Electromagnetic compatibility
Area classification indicated on the nameplate
Equipment ingress protection is IP54
Protection from rain, direct sunlight, temperature extremes
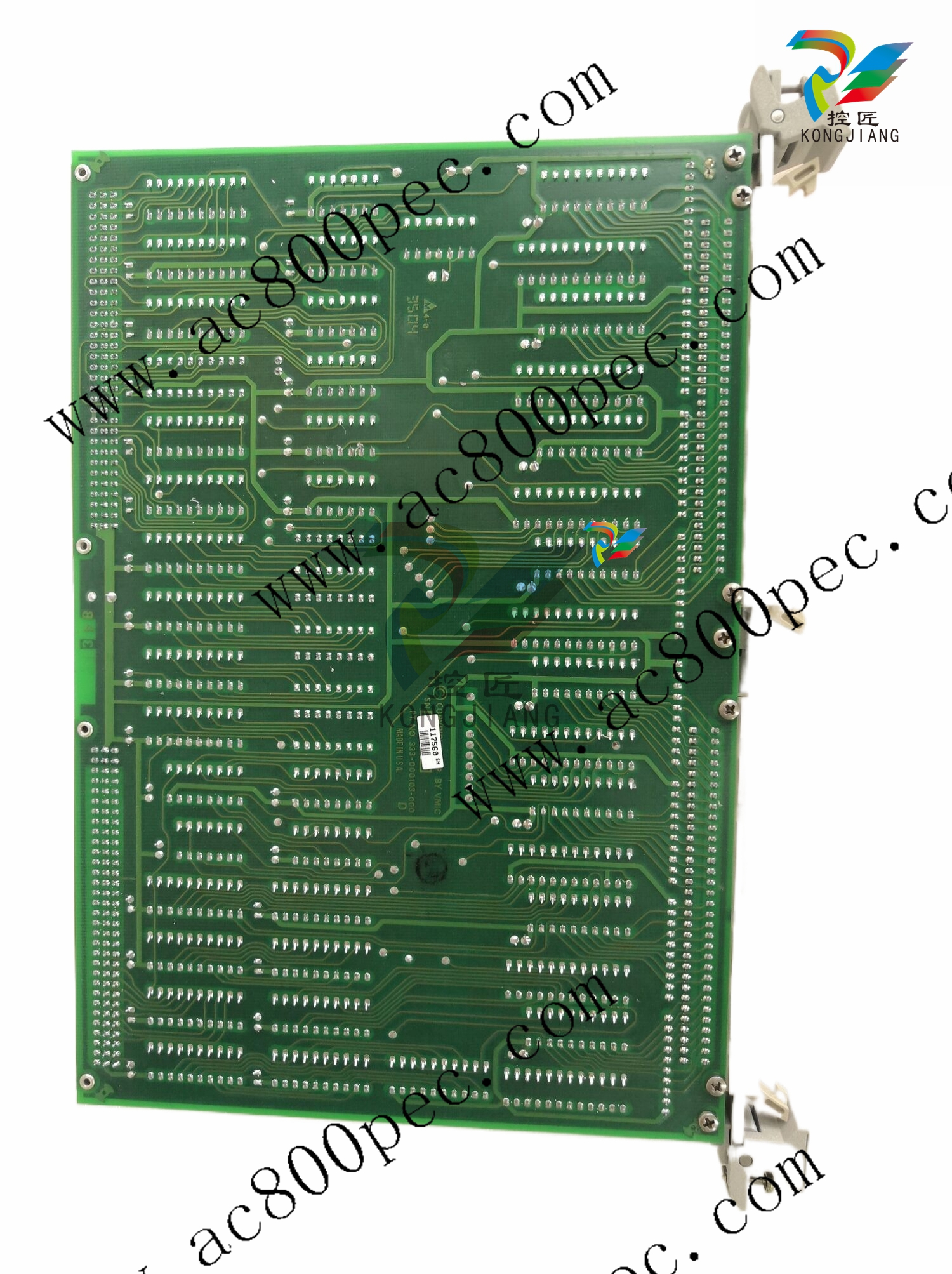
Ambient operating temperature is 0 to 50 degrees C (32 to 122 degrees F)
Avoid exposure to corrosive gas
Not intended for a combustible dust environment
Not intended for below surface mining applications
Free from dust and static electricity
Space of at least 450 mm (18 inches) to each side of the oven for various customer
connections and servicing
Space of at least 406 mm (16 inches) in front of the oven, for servicing
The Oven with Integrated Controller can be located up to 100 meters (328 feet) from any associated
oven. The Oven with Integrated Controller communicates with associated ovens through fiber optic
cables.
2.1.4 Precautions
Review the following precautions during installation and before starting the analyzer. Observe and
take note of all caution tags attached to the analyzer.
NOTICE – Equipment damage. Temperature of protective air for purge/pressurization
must not exceed 40 degrees C (104 degrees F).
Inspection required for accumulated dust before applying electric power.
Clean display with damp cloth only.
Conduit entries not used must be sealed with an approved blanking plug.
Main power supply must not exceed ±10% of the equipment rated voltage.
2.2 Prepare for installation
Since Analyzer configuration depends on the application, this manual contains only generic
engineering drawings and diagrams. Utilize the drawings, diagrams and replacement parts lists
provided in the Data Package supplied with your analyzer to ensure they are the correct ones for your
system.
After unpacking the analyzer, inspect it for damage. Also check the packing list provided with the
analyzer to make sure all equipment is included. The packing list, which is taped on the box or crate,
contains a list showing how many cartons were shipped and what each box or crate contains.
2.2.1 Installation tools and equipment
The recommended standard tools and equipment for installation are:
5/32 inch hex key wrench (supplied)
5/16 inch hex key wrench (supplied)
7/16 inch open end wrench (2)
6 inch flat blade screwdriver
9/16 inch wrench
5/8 inch wrench
8 inch adjustable wrench
Wire strippers
Digital flow meter
Leak detection solution
2.2.2 Plumbing installation
All plumbing connections enter at the right side of the Oven and Master Controller cabinets. Be careful
to avoid damaging fittings and to ensure tight connections. Refer to the Data Package for specific
plumbing information.
For brass and stainless steel pipe fittings, wrap the threads with PTFE tape or a suitable thread
sealant. Make all connections and then tighten them appropriately. Leak check each connection as
described in section 3.4.1.
2.2.3 Gas requirements
The following information represents general gas requirements for the PGC5000. Due to differences in
applications, refer to the Data Package for application-specific requirements for each analyzer.
Instrument air: instrument grade air