GE VMIVME-3113A_Scan motherboard
Burner air: ISA hydrocarbon-free grade with hydrocarbon content less than 1 ppm and dew
point less than -40 degrees C (FID and FPD applications only).
Carrier gases: varies with the application. The lower the levels of components being
measured, the higher the necessary carrier gas purity.
TCD: for percent level measurements, gases of 99.99% purity; for ppm measurement ranges,
99.995% purity.
FID: for measurements down to 5 ppm, gases of 99.995% purity; lower ranges require higher
levels of purity.
2.2.4 Calibration sample
A primary factor in determining the accuracy of the analyzer’s calibration is the quality and precision
of the calibration sample. Regardless of the sample composition or number of complete analysis
components, generally only measured components are in the calibration sample.
2.2.5 Purge air alarm
To meet Area Classification requirements, some analyzers are equipped with air purge. The analyzer
system detects the loss of purge at the Master Controller and/or oven(s) and generates alarm signals.
The customer has the responsibility to connect the purge alarm to a visual or audible enunciator
located in a constantly monitored area, in accordance with the conformity standard for purge and
pressurization protection.
2.3 Equipment mounting
WARNING – Bodily injury. Depending on the configuration of the oven, it can weigh 36 to 54
kg (80 to 120 pounds). Have one or more person help lift and move it.
Unpack the system near the installation site and move it with a transportation machine. Handle the
analyzer carefully so that it does not fall. For floor-mounted units, secure the Master Controller and
Oven dolly bolts. Secure wall-mounted units appropriately. Refer to the Outline and Mounting
Dimensions drawing in the Data Package for specific mounting information.
2.4 Connections
2.4.1 Tubing
Refer to the applicable drawings in your Data Package for specific tubing and connection information
while observing the following:
Do not remove the tube caps until immediately before making each connection. They are
provided at the analyzer tubing ports to prevent deterioration of the columns.
Ensure use of proper size tubing and pipe; refer to the Outline and Mounting Dimensions
Diagram contained in the Data Package included with your equipment.
Use tubing and fittings free of interior contamination from grease, oil or other substances.
Before connecting these lines, completely air-purge their interiors.
After connecting the tubing, perform a leak check as described in section 3.4.1.
2.4.2 Instrument air
The air supply is connected to the fitting marked Instrument Air Inlet.
2.4.3 Carrier gas
The carrier gas is connected to the fitting marked Carrier In.
IMPORTANT NOTE: Carrier gas dryer is recommended for capillary column applications.
2.4.4 Burner fuel
The burner fuel, when used, is connected to the fitting marked Burner Fuel.
2.4.5 Burner air
The burner air, when used, is connected to the fitting marked Burner Air.
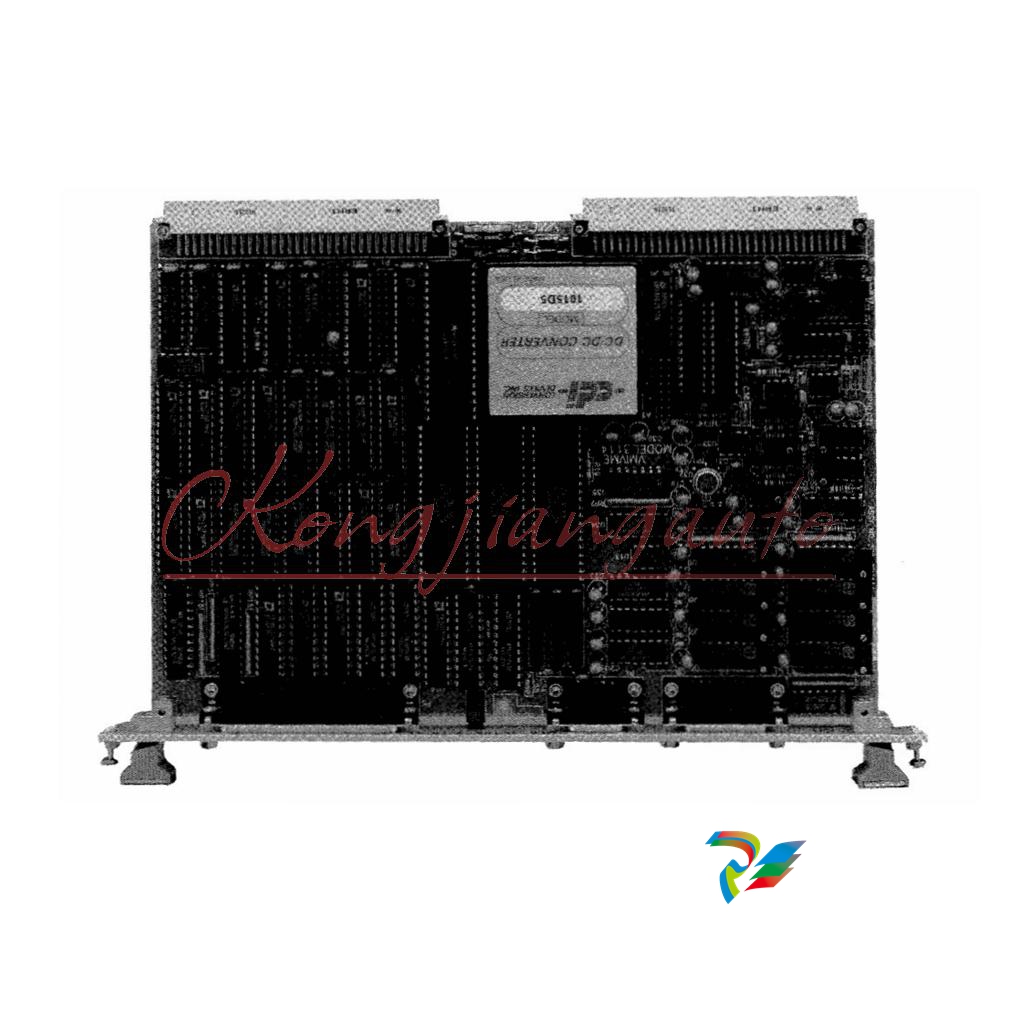
2.4.6 Sample
The methods used for transporting the sample from the process stream to the analyzer, or from the
calibration sample to the analyzer, are critical to the operation of the analyzer. Refer to the system
drawings in the Data Package for specific system connections.
2.4.7 Hydrogen gas
DANGER – Serious damage to health / risk to life. Hydrogen is highly explosive.
Follow applicable safety precautions and use extreme care in making connections.
The analyzer uses hydrogen gas as a burner fuel with flame cell detectors (FID or FPD) and
sometimes uses it as a carrier gas. Verify that the hydrogen gas meets the criteria of the gas
requirements listed in the Data Package. Also refer to the Data Package for specific connection
information.
2.4.8 Vents
All vent lines must be at atmospheric pressure unless otherwise specified in the Data Package. The
vent lines should slope down from the analyzer so that condensation will not collect in the analyzer or
cause backpressure in the external tubing. Refer to the Data Package for specific connection
information.
2.4.9 Liquid sample valve
The Liquid Sample Valve (LSV) is used only with liquid applications. The Oven Enclosure has sample
lines connected to a mounting plate attached to the LSVs mounting flange.
The LSV has the sample lines connected to the mounting plate attached to the LSVs mounting flange,
as shown in Figure 2-1.
Figure 2-1: Liquid Sample Valve
NOTICE – Equipment damage. Use two wrenches when tightening the sample line
connections at the LSV sample chamber. One wrench must be used to back up the force
applied to tighten the fitting (direct wrench force may bend the stem or damage the valve
seals).
IMPORTANT NOTE: To ensure the integrity of the components within the Liquid Sample Valve, use
the tools in LSV Tool Kit 791K009-1 when assembling of disassembling the LSV.
2.5 Electrical
The analyzer must be installed according to all applicable codes. If it is in a hazardous area, the wiring
method must conform to the applicable requirements.
Install signal wiring and power wiring in separate conduit pipes or cable trays to reduce noise and
crosstalk.