ABB Ability™ Symphony® Plus MR Series (Melody Rack)
Traditionally, production facilities maintainedmany controller subsystems, each of which
had to meet specific plant needs. However,
as business goals have changed, using a scalable
controller platform that possesses multi functional capabilities, adapts to changing
requirements, and maximizes openness and
availability, is paramount to success.
ABB Ability Symphony Plus MR Series (Melody
Rack) controllers, communication interfaces
and I/O modules meet the most challenging
requirements in each of these areas.
Thanks to their modular design, MR Series
controllers can be adapted to a wide variety
of plant types and sizes. Supported by an
efficient engineering workbench, MR Series
control based solutions contribute to a higher
return on assets by improving overall production
control, maximizing process availability, and
minimizing maintenance.
Features and benefits
Flexible, cost-effective assembly
Decentralized, DIN rail-mounted controller
assembly can be combined with local or
remote I/Os.
Comprehensive I/O system
A wide range of local and remote I/O is available
with integrated intrinsic safety design and
transmitter power supply options. Features
such as sequence of events (SOE) time stamping
(1 ms resolution), monitoring, filtering, as well
as HART, PROFIBUS, Modbus RTU and TCP
communication are supported with a wide range
of I/Os such as Melody Rack local I/O, ABB’s S800
and S900, and other remote PROFIBUS I/Os.
Distributed capability
ABB’s S800 and S900 remote I/O and Melody
Rack local I/O are connected via high-speed serial
communication buses. Local I/O offers a high
packing density to reduce mounting space to
a minimum, whereas remote I/O fully supports
distributed system configurations.
Efficient field device integration
Standardized field device tool/device type
manager (FDT/DTM) interfaces enable plug and-play integration of field devices.
Easy to configure
Module configuration and service is executed
using S+ Engineering for Melody and its unrivaled
library of fully tested and field-proven powerful
function blocks.
Inherent redundancy design
System-integrated redundancy options for power
supply, hardware and communication networks
provide the highest level of availability.
High performance modular network
Symphony Plus MR Series based control systems
uses a redundant, high-speed serial communi cation network with inherent capability for
remote communication. The network is
easy to expand without requiring routing
configuration.
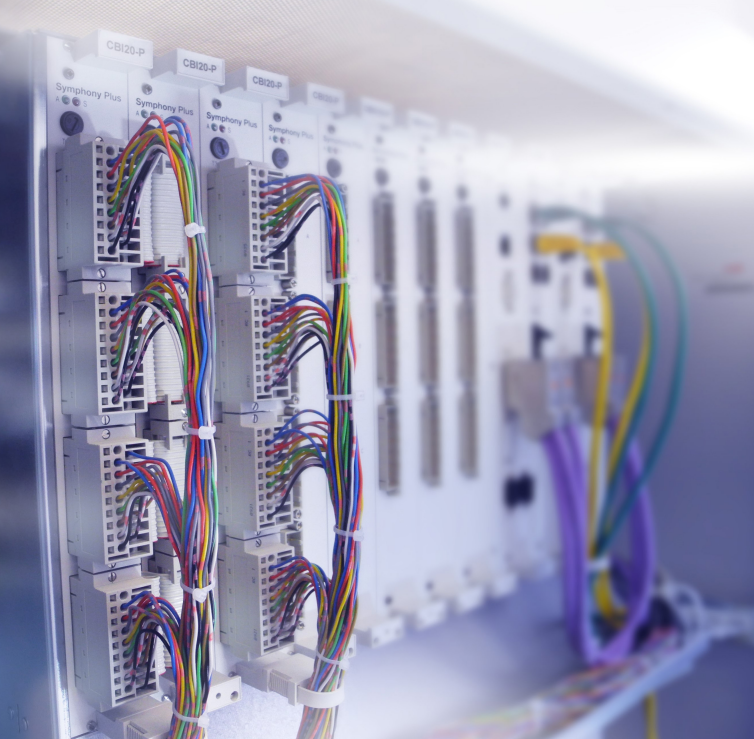
Overview
The MR Series includes a series of compact DIN
rail mounted controllers, a wide range of I/O
modules and modern, standardized fieldbus
interfaces. These modules offer all the
functions required for data acquisition and signal
conditioning, as well as powerful open loop
and closed loop control, sequence control and
monitoring. All process management
tasks are executed on the basis of integrated
complex control strategies. Without the need
for configuration, The MR Series inherent
redundancy design – including integrated
redundancy concepts for power supply,
communication and I/O – provides the highest
level of availability.
Key features include:
• A wide range of I/O interfaces with optionally
integrated intrinsic safety (Ex i) design and
transmitter power supply. Features such as
time stamping with a 1 ms resolution,
monitoring, filtering and HART communication
are implemented directly in the I/O modules
• PROFIBUS interfaces provide connections to
ABB’s S800 and S900 remote I/O stations in
Ex and non-Ex versions, as well as other
PROFIBUS devices
• IEC 61850 interface to intelligent electronic
devices (IEDs) for the integration of electrical
subsystems
• Modbus RTU and TCP interfaces provide
connections to 3rd party devices
—
02 Functional overview of MR Series capabilities
• The MR Series control network uses a
redundant, high-speed serial communication
network with inherent capability for remote
communication. The network is easy to handle,
without requiring routing configuration
• Flexible mounting alternatives such as cabinet,
DIN rail or 19” rack mounting. All three can be
combined in one project. This allows optimal
adaptation to all plant structures and supports
flexible upgrades of existing installations
• An unrivaled high packing density in the
system cabinets saves installation space
• Controller time synchronization based on
a time precision of 0.5 msec
• Sequence of events (SOE) time stamping
with a resolution of 1 ms is implemented
in the controller and local I/O module level
The control subsystem includes flexible
communication options to I/O and intelligent
field devices via system buses. HART as well as
PROFIBUS information, including configuration
and diagnostic information, is communicated
via the control network. This information is
available to system controllers and system
level applications such as asset optimization
and device management. The comprehensive
bus concept of the system controller allows
for the easy integration of HART, PROFIBUS,
Modbus RTU and TCP field devices as well as
of PROFIBUS and IEC 61850 electrical assets.
The MR Series functional capabilities are
summarized in figure 2.
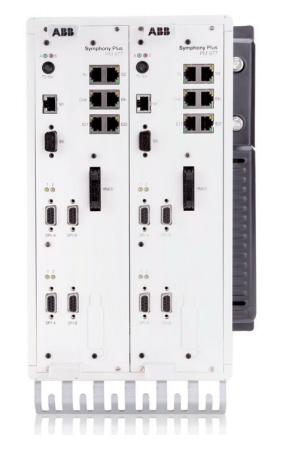
Scalable control stations
MR Series control stations are conveniently
set up according to project needs and are made
up of modular controllers and I/Os. Depending on
the scope of the automation task, the controller
is extended with I/O modules or communication
interfaces.
The controllers are connected via the control
network to ensure reliable, high speed and
system wide real-time signal exchange with
other control stations, with S+ Operations,
with system level applications and with
S+ Engineering for Melody.
Each node on the control network operates
autonomously. Acting as its own communication
manager, the system requires no traffic directors.
The controller’s associated I/O modules are
connected using the high-speed redundant serial
field network or PROFIBUS DP (DPV1 as well as
DPV2).
MR Series controllers
Melody controllers are designed for maximum
computing power and modular scalability.
Each controller can handle up to 2,000 analog
and/or digital I/O points from the local I/O, and
additionally 6,000 analog and/or digital I/O
points connected via PROFIBUS DP. In addition
to the standard tasks such as signal processing,
loop and logic control, the MR Series controller
also performs complex computations such as
sequential, batch and advanced controls.
Diagnostic routines periodically check the
hardware and firmware integrity. Any abnormal
conditions are automatically routed to the HMI
or other alarm or message collecting software.
The redundant design provides an automatic
one- to-one backup, thus ensuring high system
availability. If the primary controller is faulty, the
hot standby controller, executing the same
control strategy and process data, immediately
takes over control.
MR Series controller key features include:
• Large variety of powerful functions available
in tested libraries
• Easy configuration, service and commissioning
with S+ Engineering
• Inherent redundancy without configuration/
wiring costs
• Real-time multitasking operating system
• Up to 16 different cycle times
• Comprehensive monitoring and diagnostic
functions
• Interface for radio clock connection
• Bumpless downloadable firmware and
application programs (no EPROMs)
• Cyber security proven
• PM 877 without battery
The range of available function blocks extends
from simple control and individual drive functions
to complex recipes based on S88 and NAMUR
using sequential function charts based on IEC
61131-3.
Function blocks may also be used to set up
customer-specific libraries in S+ Engineering
for Melody
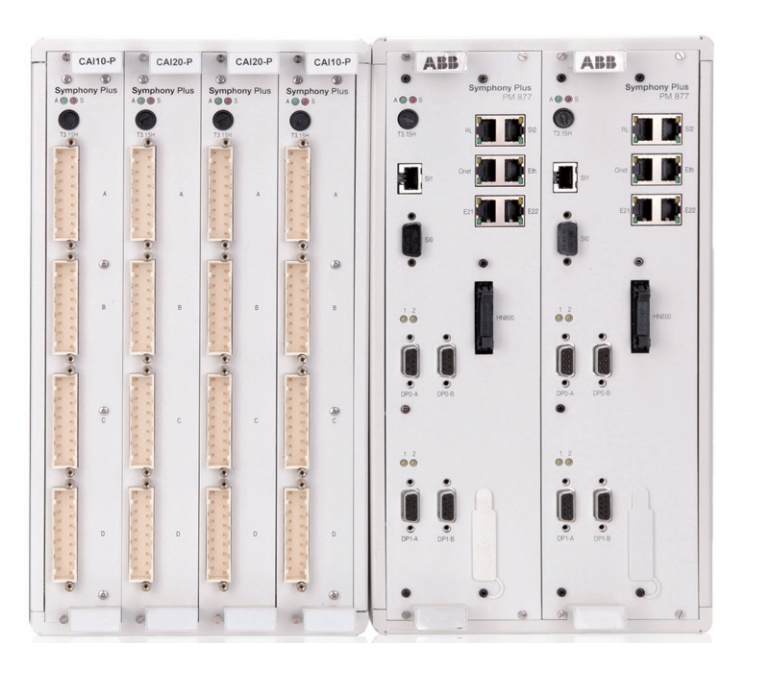
MR Series process interface
modules
The controller sets new standards for user
convenience with industrial process interface
modules. A large variety of I/O modules can
be combined to form an optimal automation
solution.
Main components of the MR Series control
station are the I/O modules and a high-speed,
redundant serial field network. Together they
operate as a subsystem dedicated to the
controller.
Local I/O types
The following local I/O types are available:
• Analog input (CAI) Ex and non-Ex
• Temperature input (CTI)
• Analog output (CAO) Ex and non-Ex
• Digital input (CBI) Ex and non-Ex
• Digital output (CBO)
• Control modules (CAC/CBC)
• Frequency input (CFI)
• Serial communication interfaces (CCF)
Redundant modular power supply is an option.
All process signals are accessible from the front
panel. The field cables are connected to cable
termination units. For I/O redundancy, associated
termination units are used. With these
termination units, it is possible to replace
defective modules without disconnecting the
field cable and without field interruption, thus
providing maximum availability.
Local I/O features
• A processor in each I/O module provides
advanced functions such as event detection
and alarm generation, time stamping with 1 ms
resolution and system diagnostics
• Downloadable firmware
• Local I/O modules provide integrated
transmitter power supply, integrated intrinsic
safety and HART communication
• HART variables can be used like the analog
values within function plans
• Distribution of I/O modules reduces cable
and installation costs. A high-speed serial
communication bus (Fnet) that is designed
for long distances combined with flexible
cabinet mounting options enables both
centralized and remote I/O locations
• Simplified user configuration eliminates
the need for calibration or onboard jumper
settings
• Maximum availability through inherent
redundancy design including redundant
communications via Fnet and optionally
redundant I/O modules
• All local I/O can be reconfigured and extended
online with new I/O module while in full normal
operation
• Each input or output can go to a pre-defined
value in case of disturbed values or
communication loss
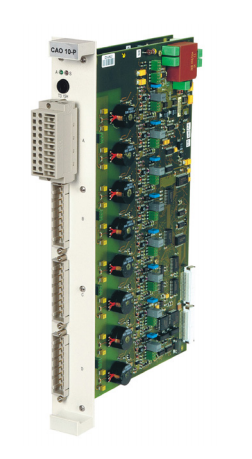
Control modules
The following control I/O modules are used for
closed loop and open loop control especially in
the power generation industry.
The drive control (CBC 11-P) modules are used for:
• On/off actuators
• Motor drives
• Solenoid valves
• Hardwired individual control stations
The closed loop output (CAC 10-P) is used for:
• Continuous controller
• PI step controller
• Current signal output to I/P converter for
pneumatic actuators
• Three-position step controller with PI behavior
• Three-point switch as positioning circuit, or
• Hardwired individual control station
Both modules operate independently of the
controller.
PROFIBUS interface
The MR Series controller integrates PROFIBUS-DP
communication, thus enabling system level
engineering of devices and device communications. In addition to communication with the
system engineering environment, fault and
diagnostic messages are displayed at the
S+ Operations workplace or other ABB operator
console.
Features include:
• PROFIBUS-DP (DPV0, DPV1 and DPV2)
• Two PROFIBUS lines per controller
• Redundancy of each PROFIBUS line
• Transfer rate adjustable in steps from
9.6 kbit/s to 12 Mbit/s
• PROFIBUS-DP/PA converter
Modbus RTU and TCP interface
A local interface card provides Modbus RTU
where the MR Series controller provides Modbus
TCP on board.
Features of Modbus TCP:
• 128 Modbus TCP server per controller
• 16 Mobus TCP slaves per controller
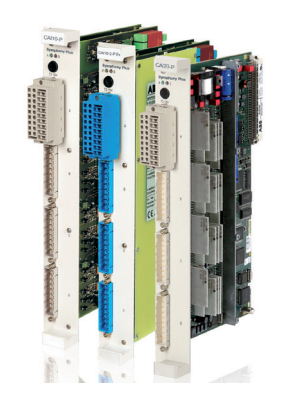