ABB AC 800PEC High Performance Control System
That is why we have designed the AC 800PEC,extending the capabilities of ABB’s well-known automation technology to handle the high-speed algorithms of processes such as power electronic applications.
Taking the technology a step further it is a dual core processor unit that combines these high speed controls with the low-speed process control tasks usually carried out by separate PLC(programmable logic controller) units. Embed into a robust and flexible system structure with integrated standard communication, the AC 800PEC is unique in the field of industrial process controllers. The AC 800PEC is the ultimate approach for high demands.
The AC 800PEC has a unique combination of features for demanding applications:
• Short cycle times, down to 100 μs
• High processing power
• Fast communication and I/O via optical links
• Programming tools:- System engineering with IEC61131-3 languages using ABB’s Control Builder, both Compact and Professional versions available- Product and control development using MATLAB®/Simulink® for model-based design,easily bridging the gap from simulation to implementation
• Full integration into ABB Ability™ System 800xA
• Innovative and flexible use of FPGAs to include protocols and application functionality in the devices without creating additional processor load
• Optical communication
• Industrial grade hardware with no moving parts
• Long life cycle, easy upgrading
• Robust reliance file system, insusceptible post power loss
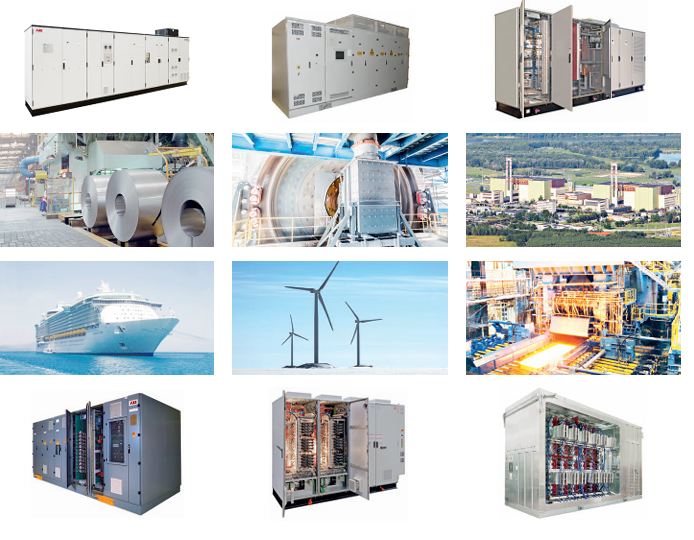
Built to control power in Process Industries
ABB has global expertise and technical know-how in processes for industrial, marine and other applications. As a result, the AC 800PEC is a key controller for ABB’s industrial applications, and also for third-party products and systems
The AC 800PEC is an efficient and flexible controller family. The benefits of short cycle times,fast (input/output) I/O, high-processing power and advanced control using MATLAB®/Simulink®:
• Increases process quality and output
• Saves development and engineering costs
• Reduces the energy consumption of you products
• Shortens time-to-market for your development project
• Saves headcount and resources in engineering and software development
• Enhances Return on Assets (ROA)
• Hardware backup trip integrated with fast
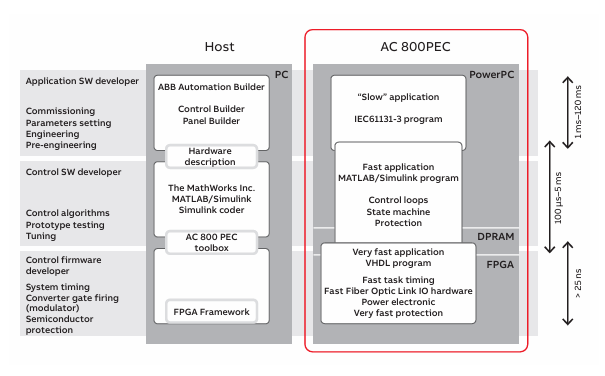
COMBI I/O
The modular structure of the AC 800PEC control system means it can adapt to any application size, from the largest industrial plants and pro pulsion systems down to very compact products,where space and cost are critical. All over the world, thousands of processors are now proving their worth in a wide variety of extremely de manding applications.
Powerful hardware for efficient, high-speed processing
The AC 800PEC combines the floating-point computing performance of the CPU with the flexibility and high-speed capability of a FPGA.
The system is separated into three performance levels covering different cycle times. Control tasks are allocated depending on their speed requirements:
• Very fast tasks down to 25 ns (nanoseconds for FPGA tasks)
• Fast tasks down to 100 μs (microseconds for Matlab/Simulink tasks)
• Slow tasks down to 1 ms (miliseconds for control tasks)
The hardware architecture of the AC 800PEC is an ideal match to the three-level software structure.
To support the short processing cycle times, the AC 800PEC provides a fast I/O system.
Depending on the speed of the I/O connection, it is possible to achieve data throughput times below 100 μs, including the time required to read, process,write and transmit the signal.
Implementation of the AC 800PEC software on the three performance levels provides an exceptional range of control and communication functionality.
The following software packages have been developed to support each of our specific high power rectifier applications.
Aluminium applications
• AC 800PEC Unit controller ↔ AC 800PEC Master controller communication via PEC - PEC fiber optical link (100 μs)
• Units can be controlled independent from master
• Allows emergency operation (full smooth current control, in emergency mode, without AC 800PEC, available only in combination with DCS800 pre magnetization)
• Predictive maintenance features can be included
• Open circuit-, over current-, under voltage-, over voltage protection packages included in software- A newly developed OPC (open circuit protection) stand-alone PLC (programmable logic controller), working in combination with the
AC 800PEC Master controller functions or as standalone protection, in case of the master panel maintenance
• Controlled shutdown in an event, not needing an immediate trip → less disturbance for your processes
• Potline load swing detection and load shedding function integrated in application software
• On Load Tap Changer fast tapping function in order to prevent DC current overload during disturbances
• A special potline-to-earth resistance measure ment system based on an AC 800PEC family available (PERMS)
• Maximum power regulation- To prevent over-shooting of power consumption and to support your power generators
• Maximum DC voltage regulation for stabilizing your process
Electrical arc furnace applications
• Stable arc detection
• Different control modes (constant current,constant power or constant resistance)
• Fast link to power quality system (PQS)ELREG (electrode regulation; anode hydraulic system control) features included:
• Electrode manual control (analog or digital)
• Electrode fast lift function (with or without separate fast up valve)
• Automatic arc strike function
• Automatic arc restrike function
• Adaptive electrode control according to furnace behavior or heat stage
• Superimposed integral control circuit
• Voltage fluctuation measurement (stability index calculation)
• Arc-to-roof detection/protection
• Arc-to-roof protection during arc strike sequence
• Hydraulic oil pressure supervision and electrode protection
• Cave-in detection
• High-voltage detection
• Counter pressure valve control logic
• Voltage-to-ground supervision
• Roof voltage monitoring
• Electrode auto raise function after furnace off command (distance or position selectable)
• Blocking valve control
• Electrode speed limitation for electrode and arm protection
• Future features- Automatic proportional valve linearization check- Automatic proportional valve linearization- Dynamic voltage setpoint control for a stable melting process
Chemical applications:
• OLTC step compensation for smooth process control- IDC current step compensation for smooth current change when stepping up
• Power factor compensation by OLTC
• Predictive maintenance features can be included
• Software protection packages including:- DC over current protection- AC over- and undervoltage protection- AC phase unbalance protection- System unbalance protection for 12 pulse systems
• DC earth fault detection available by 3 voltmeter method
• Process pulse block loop with SIL 3 level
• Voltage ride-through in case of incoming voltage dips
Electrowinning industries (copper & zinc):
• IDC current step compensation for smooth current change when stepping up
• Power factor compensation by OLTC
• Predictive maintenance features can be included
• DC overcurrent protection
• AC over- and undervoltage protection
• AC phase unbalance protection
• System unbalance protection for 12 pulse systems
• Master DC current control for parallel rectifier units
• DC open loop detection during start-up
• DC open loop protection during operation
DC power supplies for graphite electrode plants
The graphitisation process demands a large variation of voltage and current from the DC power supply.
• Constant DC power suppy for the process irrespective of changing process resistance - Possible due to the very fast cycle times of AC 800PEC controller.
• Customer tailed process recipes can be added and modified from the operator panel in order to meet the specific customer requirements.
• After adding the corresponding recipes, the rectifier follows the predefined DC current, DC voltage and maximum allowed power set points, including all necessary graphitisation specific protection functions.
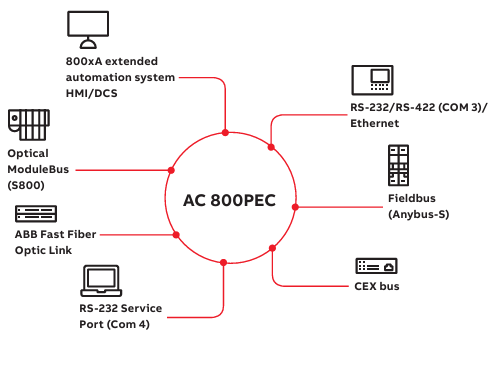