ABB ACS850-04 drive modules
What this chapter contains
This chapter contains the safety instructions which you must follow when installing,
operating and servicing the drive. If ignored, physical injury or death may follow, or
damage may occur to the drive, motor or driven equipment. Read the safety
instructions before you work on the unit.
Use of warnings
Warnings caution you about conditions which can result in serious injury or death
and/or damage to the equipment and advise on how to avoid the danger. The
following warning symbols are used in this manual:
Electricity warning warns of hazards from electricity which can cause
physical injury and/or damage to the equipment.
General warning warns about conditions, other than those caused by
electricity which can result in physical injury and/or damage to the
equipment.
Electrostatic sensitive devices warning warns of electrostatic
discharge which can damage the equipment.
Hot surface warning warns of component surfaces that may become
hot enough to cause burns if touched.
Electrical safety
These warnings are intended for all who work on the drive, motor cable or motor.
WARNING! Ignoring the following instructions can cause physical injury or death, or
damage to the equipment:
• Only qualified electricians are allowed to install and maintain the drive.
• Never work on the drive, motor cable or motor when main power is applied.
After disconnecting the input power, always wait for 5 min to let the intermediate
circuit capacitors discharge before you start working on the drive, motor or
motor cable.
Always ensure by measuring with a multimeter (impedance at least 1 Mohm)
that:
1. voltage between drive input phases U1, V1 and W1 and the frame is close to
0 V.
2. voltage between terminals UDC+ and UDC- and the frame is close to 0 V.
• Do not work on the control cables when power is applied to the drive or to the
external control circuits. Externally supplied control circuits may cause
dangerous voltages inside the drive even when the main power on the drive is
switched off.
• Do not make any insulation or voltage withstand tests on the drive or drive
modules.
Note:
• The motor cable terminals on the drive are at a dangerously high voltage when
the input power is on, regardless of whether the motor is running or not.
• The brake control terminals (UDC+, UDC-, R+ and R- terminals) carry a
dangerous DC voltage (over 500 V).
• Depending on the external wiring, dangerous voltages (115 V, 220 V or 230 V)
may be present on the terminals of relay outputs (X2) or Safe torque off (X6).
• The Safe torque off function does not remove the voltage from the main and
auxiliary circuits
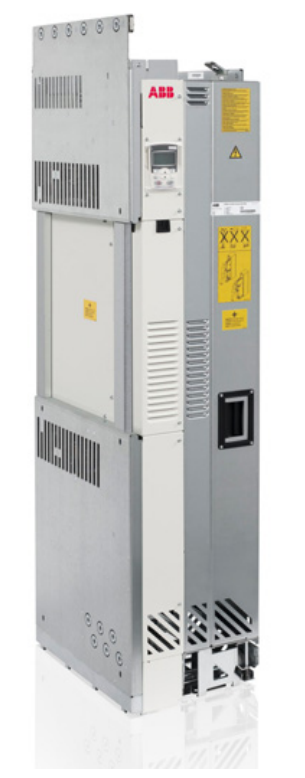
Grounding
These instructions are intended for all who are responsible for the grounding of the
drive.
WARNING! Ignoring the following instructions can cause physical injury, death,
increased electromagnetic interference and equipment malfunction:
• Ground the drive, motor and adjoining equipment to ensure personnel safety in
all circumstances, and to reduce electromagnetic emission and interference.
• Make sure that grounding conductors are adequately sized as required by
safety regulations.
• In a multiple-drive installation, connect each drive separately to protective
earth (PE).
• Where EMC emissions must be minimized, make a 360° high frequency
grounding of cable entries at the cabinet lead-through in order to suppress
electromagnetic disturbances. In addition, connect the cable shields to
protective earth (PE) in order to meet safety regulations.
Note:
• Power cable shields are suitable for equipment grounding conductors only
when adequately sized to meet safety regulations.
• As the normal leakage current of the drive is higher than 3.5 mA AC or 10 mA
DC, a fixed protective earth connection is required by EN 61800-5-1, 4.3.5.5.2.
Permanent magnet motor drives
These are additional warnings concerning permanent magnet motor drives.
WARNING! Ignoring the instructions can cause physical injury or death, or damage
to the equipment.
• Do not work on the drive when the permanent magnet motor is rotating. Also,
when the supply power is switched off and the drive is stopped, a rotating
permanent magnet motor feeds power to the intermediate circuit of the drive and
the supply connections become live.
Before installation and maintenance work on the drive:
• Stop the motor.
• Ensure that there is no voltage on the drive power terminals according to step 1 or
2, or if possible, according to the both steps.
1. Disconnect the motor from the drive with a safety switch or by other means.
Measure that there is no voltage present on the drive input, output or DC
terminals (U1, V1, W1, U2, V2, W2, UDC+, UDC-).
2. Ensure that the motor cannot rotate during work. Make sure that no other system,
like hydraulic crawling drives, is able to rotate the motor directly or through any
mechanical connection like felt, nip, rope, etc. Measure that there is no voltage
present on the drive input, output or DC terminals (U1, V1, W1, U2, V2, W2,
UDC+, UDC-). Ground the drive output terminals temporarily by connecting them
together as well as to the PE.
These instructions are intended for all who install and service the drive.
WARNING! Ignoring the following instructions can cause physical injury or death,
or damage to the equipment:
• - Lift the drive module using the lifting lugs attached to the top and base of the
unit.
- Handle the drive module carefully. Make sure that the module does not fall
down when moving it on the floor and during installation and maintenance
work: Open the support legs by pressing each leg a little down (1, 2) and
turning it aside. When ever possible secure the module also with chains.
- Do not tilt the drive module (A). It is heavy (over 160 kg [350 lb]) and its
center of gravity is high. The module will overturn from a sideways tilt of 5
degrees. Do not leave the module unattended on a sloping floor.
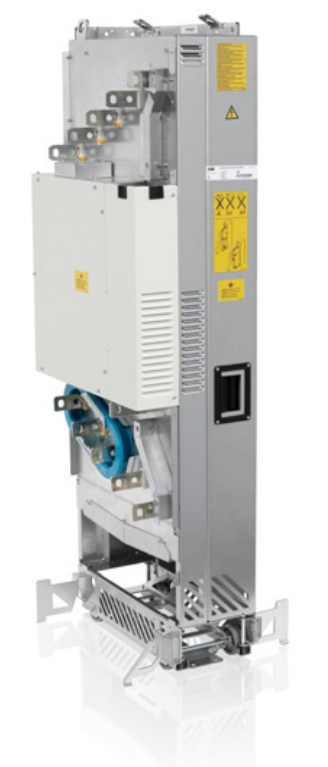
Push the drive module into the cabinet and pull it from the cabinet carefully
preferably with help from another person as shown below. Keep a constant
pressure with one foot on the base of the module to prevent the module from
falling on its back. Use safety shoes with metal toe cap to avoid foot injury.
Do not use the ramp with plinth heights which exceed the maximum height
marked on the ramp next to the fastening screw. (The maximum plinth height
is 50 mm when the telescopic ramp is shortest and 150 mm when the ramp is
longest.) Tighten the two fastening bolts of the ramp carefully.
• Beware of hot surfaces. Some parts, such as heatsinks of power
semiconductors, remain hot for a while after disconnection of the electrical
supply.
• Make sure that dust from borings and grindings does not enter the drive when
installing. Electrically conductive dust inside the unit may cause damage or
malfunctioning.
• Ensure sufficient cooling.
• Do not fasten the drive by riveting or welding.
WARNING! Ignoring the following instructions can cause equipment malfunction
and damage to the fiber optic cables:
• Handle the fiber optic cables with care. When unplugging optic cables, always
grab the connector, not the cable itself. Do not touch the ends of the fibers with
bare hands as the fiber is extremely sensitive to dirt. The minimum allowed
bend radius is 35 mm (1.4 in.).
Printed circuit boards
WARNING! lgnoring the following instructions can cause damage to the printed
circuit boards:
Wear a grounding wrist band when handling the boards. Do not touch the
boards unnecessarily. The printed circuit boards contain components sensitive
to electrostatic discharge.
Safe start-up and operation
General safety
These warnings are intended for all who plan the operation of the drive or operate
the drive.
WARNING! Ignoring the following instructions can cause physical injury or death,
or damage to the equipment:
Before adjusting the drive and putting it into service, make sure that the motor
and all driven equipment are suitable for operation throughout the speed range
provided by the drive. The drive can be adjusted to operate the motor at
speeds above and below the speed provided by connecting the motor directly
to the power line.
Do not activate any automatic fault reset functions of the drive control program
if dangerous situations can occur. When activated, these functions will reset
the drive and resume operation after a fault.
Do not control the motor with an AC contactor or disconnecting device;
instead, use the control panel keysand ⑦, or commands via the l/O
board of the drive. The maximum allowed number ofcharging cycles of the DC
capacitors, ie, power-ups by applying power, is five in ten minutes.
Note:
●If an external source for start command is selected and it is ON, the drive will
start immediately after an input voltage break or fault reset unless the drive is
configured for 3-wire (a pulse) start/stop.
.When the control location is not set to local, the stop key on the control panel
will not stop the drive.
Permanent magnet motor drives
WARNING! Do not run the motor over the rated speed. Motor overspeed leads to
overvoltage which may damage orexplode the capacitors in the intermediate circuit
of the drive.