ABB Bridge Controller and Process Bus Adapter BRC-300 and PBA-200
The Harmony Bridge Controller (BRC-300) is a high-perfor mance, high-capacity process controller. It is a rack controller
designed to interface with both Harmony block I/O and Har mony rack I/O in the Symphony™ Enterprise Management
and Control System. The controller is fully compatible with the
INFI 90® OPEN system in functionality, communication and
packaging. The controller collects process I/O, performs con trol algorithms and outputs control signals to process level
devices. It also imports and exports process data of other con trollers and system nodes, and accepts control commands
from operators and computers connected to the network.
This instruction provides information about how the controller
works, and how to install, configure, operate and troubleshoot
the controller.
The controller is designed for redundancy (two controllers
needed). This can be achieved while remaining connected to
the Hnet or not.
NOTES:
1. The Harmony Bridge Controller BRC-300 is referred to as controller
throughout this instruction.
2. The PBA-200 Processor Bus Adapter is referred to as PBA throughout
this instruction.
This release of the BRC-300 controller with G.0 firmware does not
support module bus functionality. References to module bus in this
revision of the instruction should be ignored and not used
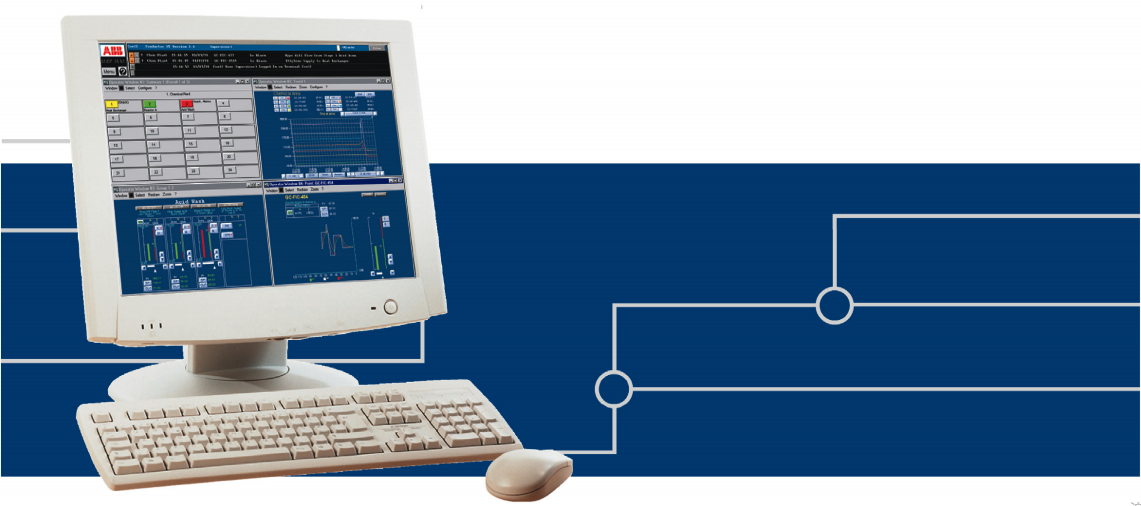
GENERAL
WARNINGS
Equipment Environment
All components, whether in transportation, operation or storage,
must be in a noncorrosive environment.
Electrical Shock Hazard During Maintenance
Disconnect power or take precautions to insure that contact with
energized parts is avoided when servicing.
Special Handling
This module uses electrostatic sensitive devices.
SPECIFIC
WARNINGS
Disconnect power before installing dipshunts on the module mount ing unit backplane. Failure to do so will result in contact with cabinet
areas that could cause severe or fatal shock. (p. 3-10, 3-12)
If removing an existing PBA-100 mounting bracket on the MMU
backplane, disconnect power before. Failure to do so will result in
contact with cabinet areas that could cause severe or fatal shock.
(p. 7-3)
Wear eye protection whenever working with cleaning solvents.
When removing solvents from printed circuit boards using com pressed air, injury to the eyes could result from splashing solvent as
it is removed from the printed circuit board. (p. 6-2)
Do not reset a controller before the LEDs or controller status byte
indicate that the controller is available. Resetting a controller prema turely could result in unpredictable operation, loss of output data, or
loss of control. (p. A-2)
SPECIFIC
CAUTIONS
Do not replace a BRC-200 with a BRC-300. (p. 1-3)
Do not operate the controller with the machine fault timer circuit dis abled (jumper pins connected). Unpredictable controller outputs and
configuration corruption may result. The unpredictable controller
outputs may damage control equipment connected to the controller.
(p. 3-16)
To avoid potential controller damage, evaluate your system for com patibility prior to controller installation.
This controller uses connec tions to the module mounting unit backplane that served other
functions in early Network 90 systems. (p. 3-16)
ABB will provide assistance in the operation and repair of its
products. Requests for sales or application services should be
made to your nearest sales or service office. ABB can also pro vide installation, repair and maintenance contract services.
When ordering parts, use nomenclature or part numbers and
part descriptions from equipment manuals. Parts without a
description must be ordered from the nearest sales or service
office. Recommended spare parts lists, including prices are
available though the nearest sales or service office.
ABB has modern training facilities available for training your
personnel. On-site training is also available. Contact your
nearest ABB sales office for specific information and schedul ing.
Additional copies of this instruction, or other instructions, can
be obtained from the nearest ABB sales office at a reasonable
charge.
The BRC-300 is a high-performance, high-capacity process
controller. It is a rack controller designed to interface with
Harmony block I/O, Harmony rack I/O, and S800 I/O in the
Symphony Enterprise Management and Control System. The
controller is fully compatible with the INFI 90 OPEN system in
functionality, communication, and packaging.
The controller is a stand-alone device that can handle specific
control and information processing applications in addition to
multiple-loop analog, sequential, and batch control. It has the
power to execute demanding process control applications that
are data intensive, program intensive or both. The controller
supports multiple control languages such as C and function
codes (FC).
The Symphony system uses a variety of analog, control, and
digital I/O devices to interface with the process. Control I/O is
available from block I/O using the Harmony communication
network (Hnet) or from Harmony rack I/O controllers using
the I/O expander bus. Figure 1-1 shows the controller architecture.
For added reliability, the controller has circuitry that supports
redundancy. A redundant controller waits in a standby mode
while the primary controller executes. If the primary goes
offline for any reason, there is a seamless transfer of control to
the redundant controller.
A Processor Bus Adapter (PBA) is required to support redundant Hnet buses. When no Hnet and termination unit (TU)
connection is needed, a PBA is not required.
NOTES:
1. The BRC-300 cannot have redundancy functionality connected with a
BRC-100 or BRC-200.
2. Using a front connector, the redundancy scheme changes the need for the
PBA except for Hnet systems. Also, a PBA is not needed for expander bus systems unless the serial ports or the stations link are needed.