ABB PE1315A 5FSE707630-7 photoelectric isolation pulse amplifier
Attachment bolts, specificationThe table specifies the type of securing screws and washers to be used to secure
the robot directly to the foundation. It also specifies the type of pins to be used.
M12x35 (robot installation directly on
foundation)
Suitable screws
4 pcs Quantity
8.8 Quality
13 x 20 x 2, steel hardness class 300HV Suitable washer
2 pcs, D6x20, ISO 2338 - 6m6x20 - A1 Guide pins
55 Nm ± 5 Nm Tightening torque
xx0900000643
Level surface requirements
WARNING
It is very important to always define correct actual load data and correct payload
of the robot. Incorrect definitions of load data can result in overloading of the
robot.
If incorrect load data and/or loads are outside load diagram is used the following
parts can be damaged due to overload:
• motors
• gearboxes
• mechanical structure
WARNING
In the robot system is the service routine LoadIdentify available, which allows
the user to make an automatic definition of the tool and load, to determine correct
load parameters. For detailed information, see Operating manual - IRC5 with
FlexPendant.
WARNING
Robots running with incorrect load data and/or with loads outside diagram, will
not be covered by robot warranty.
General
The load diagram includes a nominal pay load inertia, J0 of 0.06 kgm2 and an extra
load of 0.3 kg at the upper arm housing. At different moment of inertia the load
diagram will be changed. For robots thatare allowed tilted, wall or inverted mounted,
the load diagrams as given are valid and thus it is also possible to use RobotLoad
within those tilt and axis limits.
Control of load case by "RobotLoad"
To easily controla specific load case, use the calculation program ABB RobotLoad.
Contact your local ABB organization for more information.
The result from RobotLoad is only valid within the maximum loads and tilt angles.
There is no warning if the maximum permitted armload is exceeded. For over load
cases and special applications, contact ABB for further analysis.
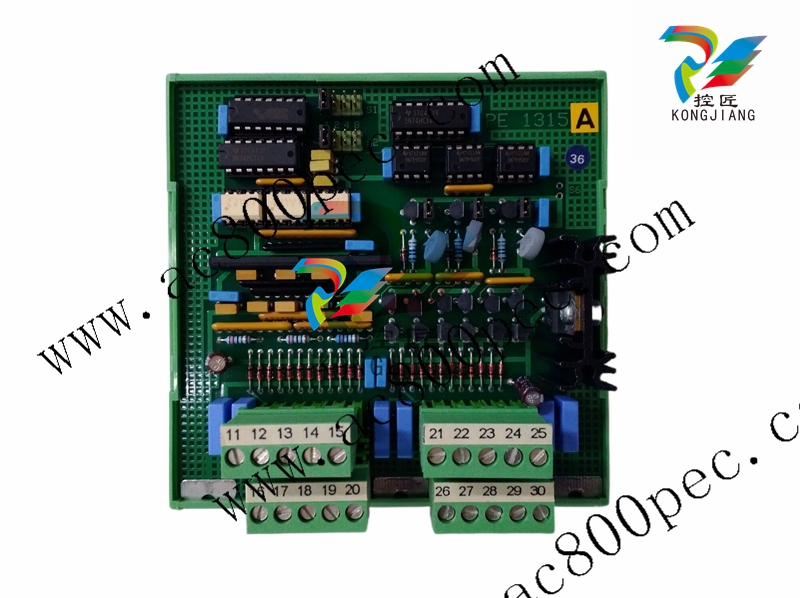
Total load given as: Mass in kg, center of gravity (Z and L) in m and moment of
inertia (Jox, Joy, Jox) in kgm2
. L= √(X2 + Y2).
Full movement of Axis 5 (±130º)
Max. value Axis Robot variant
J5 = Mass x ((Z + 0.082)2 + L
2) + max (Jox, Joy) ≤ 0.45 kgm2 IRB 1200-7/0.7 5
J5 = Mass x ((Z + 0.082)2 + L
2) + max (Jox, Joy) ≤ 0.45 kgm2 IRB 1200-5/0.9
J6= Mass x L
2 + J0Z ≤ 0.2 kgm2 IRB 1200-7/0.7 6
J6= Mass x L
2 + J0Z ≤ 0.2 kgm2 IRB 1200-5/0.9
xx1400000342
Description Position
Center of gravity A
Max. moment of inertia around the X, Y and Z axes at center of
gravity.
Jox, Joy, Joz
Limited axis 5, center line down
Max. value Axis Robot variant
J5 = Mass x ((Z + 0.082)2 + L
2) + max (Jox, Joy) ≤ 0.45 kgm2 IRB 1200-7/0.7 5
J5 = Mass x ((Z + 0.082)2 + L
2) + max (Jox, Joy) ≤ 0.45 kgm2 IRB 1200-5/0.9
J6= Mass x L
2 + J0Z ≤ 0.2 kgm2 IRB 1200-7/0.7 6
J6= Mass x L
2 + J0Z ≤ 0.2 kgm2 IRB 1200-5/0.9