ABB PFCL201C 10KN tension pillow sensor unit
Pos
Center of gravity A
Max. moment of inertia around the X, Y and Z axes at center of
gravity.
Jox, Joy, Joz
Wrist torque
The table below shows the maximum permissible torque due to payload.
Note
The valuesare for reference only,and should not be used for calculating permitted
load offset (position of center of gravity) within the load diagram, since those
also are limited by main axes torques as well as dynamic loads. Also arm loads
will influence the permitted load diagram, contact your local ABB organization.
Max torque valid at
load
Max wrist torque
axis 6
Max wrist torque
axis 4 and 5
Robot variant
7 kg 6.2 Nm 12.5 Nm IRB 1200-7/0.7
5 kg 4.4 Nm 8.9 Nm IRB 1200-5/0.9
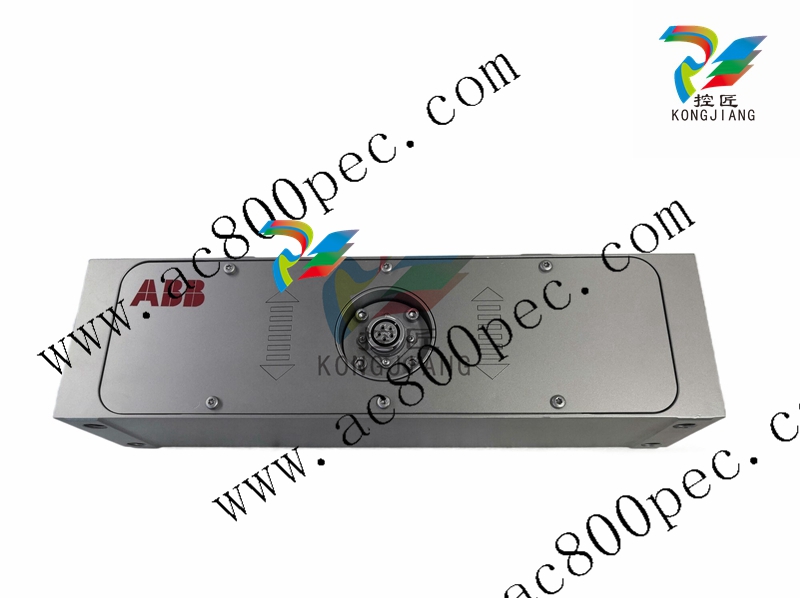
General
Higher values can be reached with lower loads than the nominal because of our
dynamical motion control QuickMove2. For specific values in the unique customer
cycle, or for robots not listed in the table below, we recommend then to use
RobotStudio.
Maximum Cartesian design acceleration for nominal loads
Controlled Motion
Max acceleration at nominal load
COG [m/s2]
E-stop
Max acceleration at nominal load
COG [m/s2]
Robot type
68 IRB 1200-7/0.7 88
79 IRB 1200-5/0.9 94
Note
Acceleration levels for E-stop and controlled motion includes acceleration due
to gravitational forces. Nominal load is define with nominal mass and cog with
max offset in Z and L (see load diagram).
1.5 Fitting of equipment
1.5.1 Introduction to fitting of equipment
General
Extra loads can be mounted on to the upper arm. Definitions of load area and
permitted load are shown in figure below. The center of gravity of the extra load
shall be within the marked load areas. The robot is supplied with holes for fitting
of extra equipment. (See Holes for fitting extra equipment on page 33).