Features
Complete Analog subsystem includes Base Converter
and Expander modules
Base Converter module has eight differential inputs
individually configurable for voltage or current
Accepts unipolar or bipolar Analog Inputs up to " 10
volts full scale
Accepts 4 to 20 milliamp current loop signals
Individual user scaling on each input channel on Base
Converter module; scaling on a per module basis for
Expander modules
Fast update rate for Base Converter module
Voltage and current Expander modules, each with 16
inputs, provides for additional inputs at a lower cost
per point
Complete subsystem can accept up to 120 inputs
No jumpers or DIP switches to configure
Easy configuration with MS-DOSor Windows
programming software configuration function.
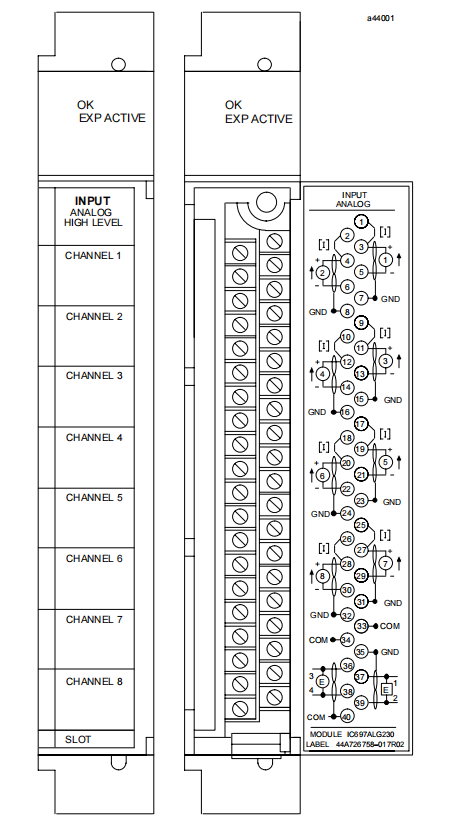
Functions
The High Level Analog Input subsystem for the Programmable Logic Controller (PLC) accepts analog inputs of up to Ç 10 volts full scale, or 4 to 20 milliamp
current loop signals. These inputs are converted to
digital form for use by the CPU or other controllers
accessing analog inputs via the VME backplane.
Converted data is presented as 2’s complement (sign
+ 15 bits). The basic converter is 14 bits resolution (1
part in 16384); an oversampling and averaging technique further enhances this resolution. Inputs are
protected against transient and steady-state overvoltage conditions.
Analog inputs use %AI references in the programmable controller. A maximum of 8K words of %AI
memory is currently available in the programmable
controller. Each input channel uses one word (16 bits)
of %AI memory.
Field wiring is made to a removable terminal board
and the module is mechanically keyed to ensure correct replacement with a similar module type in the
field. I/O references are user configurable without the
use of jumpers or DIP switches on the module.
Configuration is done using the configuration function of the MS-DOS or Windowsprogramming software running on Windows 95 or Windows NT over
Ethernet TCP/IP or through the SNP port. The Programming Software configuration function is installed
on the programming device. The programming device can be an IBM XT, AT, PS/2 or compatible Personal Computer.
High Level Analog Input System Modules
Three module types are included in the High Level
Analog Input subsystem: a Base Converter module, a
Current Expander module, and a Voltage Expander
module. A typical subsystem will use a Base Convert er module and (if required) one or more expander
modules.
Base Converter module - catalog number
IC697ALG230
This module has eight differential inputs and
an expansion port. Each input can be individu ally configured for either voltage or current.
Each of the input channels also has individual
user scaling.
On-board load resistors are included for normal
input current ranges up to Ç 40 mA. If other
current ranges or different resolution is re quired, external resistors may be used.
Standard system configurations for Ç 10 volts
and 4 to 20 mA are available. These, and other
lower input ranges, can be scaled to engineer ing units with the user scaling feature.
Expander Modules
Up to seven Expander modules can be daisy chained off the Base Converter module to in crease the number of inputs of the total subsys tem up to a maximum of 120.
The Base Converter module accepts any mix of
the two Expander module types.
A common user scaling factor applies to all in puts on each Expander module, however each
Expander module may be individually scaled as
required.
Current Input Expander module - catalog number
IC697ALG440
The Current Expander module has 16 current
inputs each accepting up to Ç 20 mA.
Voltage Input Expander module - catalog number
IC697ALG441
The Voltage Expander module has 16 differen tial voltage inputs each accepting up to Ç 10V
signals.
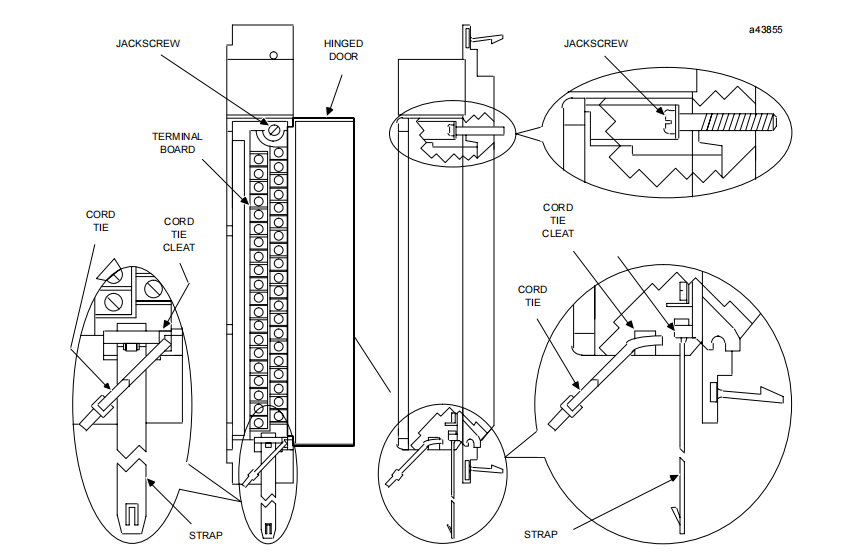
Recommended Field Wiring Procedures
The following procedures are recommended when
connecting field wiring to the detachable terminal
board on an Analog Input Base Converter or Expander module. Module features referenced in the following procedures which are common to all IC697 I/O
modules are illustrated in the following figure.
Figure 8. Removal of I/O Terminal Board
5. After completing connections to all modules in a
rack, the wire bundle must be secured. To ensure
that the wire bundle is secured properly, it is recommended that a cable tie be wrapped around the
wire bundle and tightly secured through the cable
tie cleat located at the lower right corner of the
terminal board. For extremely large wire bundles,
additional cable ties should be used.
6. A door label insert is included with each module to
indicate circuit wiring information and provide
space to record user circuit wiring identification.
A slot is provided on the hinged door to allow for
insertion of this label. If the label is difficult to insert, crease the scored edge before insertion. The
outside label has a color coded stripe to allow
quick identification of the module voltage type
(blue: low voltage; red: high voltage).
7. After field wiring is completed, the terminal board
should be securely fastened to the rack by inserting the terminal board strap (attached to each
module) into the small rectangular slots in the bottom card guide grill on the rack. This strap not
only secures the terminal board to the rack, it also
provides a way of identifying the wired terminal
board with its correct mating rack slot location.
8. For adequate module ventilation, it is recommended that at least a 5 inch (127mm) clearance be
allowed above and below the rack grill. Wire
bundles should not obstruct the rack grill work.
Removing an I/O Module
The instructions below should be followed when removing an I/O module from its slot in a rack.
Grasp the board firmly at the top and bottom of
the board cover with your thumbs on the front of
the cover and your fingers on the plastic clips on
the back of the cover.
Squeeze the rack clips on the back of the cover
with your fingers to disengage the clip from the
rack rail and pull the board firmly to remove it
from the backplane connector.
Slide the board along the card guide and remove it
from the rack.