ABB 086406-002 stepper linear control board
Transmission and distribution networks are frequently being expanded and reinforced,often resulting in more complex networks.This is valid for
electrical transmission and distribution networks,
as well as for gas,oil,water,wastewater and district
heating grids.
The task of monitoring and controlling the energy
transportation in order to achieve an economical
operation control requires an ongoing penetration
of the grid down to the lowest levels.
The increasing availability requirements of energy
and its distribution and transportation also increases the demand of control systems.New and
improved communication possibilities with higher
transmission bandwidths and new transmission
media allow telecontrol technology to mange this.
Continually increasing capabilities of decentralized
control and closed-loop control solutions,based
on higher performance microcontroller technology,also allows more functions to run directly in the
station.This is valid not only for new remote stations,but also in stations which have to be upgraded due to a higher demand for information or
station that need to be modernized due to age
(retrofit).
In all cases,the telecontrol interface is the basic
functional package.
The adaptation of new Intelligent Electronic Devices (IED) and expansion with application functions based on Programmable Logic Controller
(PLC) solutions must also be possible.It is the task
of modern RTU's to provide the right solution to
these requirements.
The deregulation activities in the energy market,
especially the metering tasks,requires more online
information in order to control the energy flow
and energy consumption.Municipal utility companies,responsible for the electrical,gas,water and
wastewater grids,are moving towards controlling
these networks in a more centralized fashion,i.e.in
one central control center utilizing only one control system.This requires the different telecontrol
communication links to be harmonized.
The process data object model has to be coordinated between the different grid types.
The standardization of telecontrol protocols and
the increasing capabilities of communication networks makes this possible.
A new RTU must be able to support demands of
higher flexibility by adapting ANSI and IEC telecontrol protocol standards.The new RTU shall
have the capacity to be connected to new communication media and digital communication networks.
Our strengths
• Usable for different applications
• Remote Control
• Station Automation
• Communication Gateway
• Process-oriented configuration with open data
exchange concept and MS-ExcelTM-Integration
• Integrated Human Machine Interface
with basic monitoring and control functions
• No special tool for diagnoses required
due to utilisation of web server technologies
• Programmable PLC functions
• Support of standard transmission/communication protocols
• Events detection with a time resolution
of 1 ms
• Real-time acquisition with DCF77,GPS,SNTP
or IRIG-B
• Flexible system concept
- scalable redundancy
- scalable I/O
- scalable communication
• High performance central processing units
with 32-bit processor and multiple interfaces
• Distributed input/output units with high
degree pre-processing functions
• Only a few types of different I/O modules
• Same I/O modules used in RTU200 and RTU232
• Applicable from medium voltage to highest
voltage level
• Local presence of ABB in more than 50 countries
• 2'000 worldwide RTU560 installations per year,
more than 10'000 RTU560 installations in total
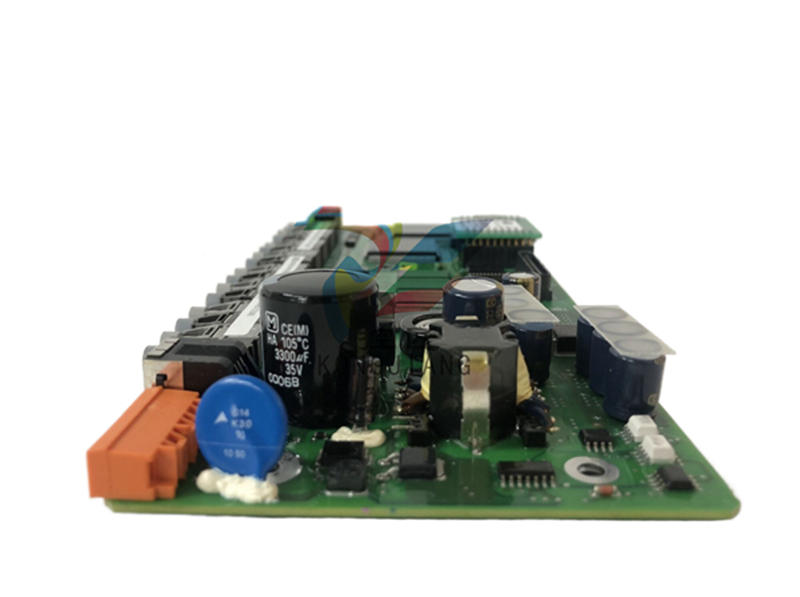
The engineering work is an important cost factor
that can be reduced by standardizing the process
object model and ensuring that it supports stateof-the-art engineering tools.The engineering tool
of the RTU must be able to perform the task of a
single,stand-alone RTU,as well as be able to be
integrated into an overall data engineering concept for a network control system.
In addition to the basic functions,(i.e.data acquisition and control) modern telecontrol systems are
required to provide a higher degree of functionality within the stations e.g.:
• High functional scope for telecontrol application
functions
• Execute control and closed-loop applications
using PLC capabilities
• Archive features to provide process data availability over longer periods for recovering or decoupling,e.g.the storing of disturbance files recorded by protection relays in an archive and
analyzing them later,after transferring them to
an Office PC
• Communication with
multiple Network
Control Centers
(NCC).of process data
filtering according to
the demands of the
NCC.Possible with different telecontrol protocols for each NCC
• Extended diagnosis
functionality of the
RTU equipment to
reduce the costs for
problem analysis and maintenance by accessing
the information via Internet or Intranet options.
This should be possible independent of the directly connected telecontrol links
• Interfacing various types of IEDs,such as digital
protection relays or new transducers via fieldbus interfaces,etc
• Flexibility and space for future demands to extend the RTU for additional installed primary
process units and/or higher demands in terms of
control
The architecture of a telecontrol system must be
designed in such a way that it,thanks to its modularity and flexibility,can be adapted to the conditions and sizes of the different stations.It should
also be open for later extensions of any type.