GE FANUC A-S1300B ControlProduct
The ControlST* software suite, which contains the ToolboxST* toolset, is used with Mark
VIe controls and related systems for programming, configuration, trending, and analyzing
diagnostics. It provides quality, time-coherent data in the controllers and at the plant level
for effectively managing control system equipment.
The Mark VIeS Safety control is a stand-alone safety control system for safety-critical
applications that conform to IEC®-61508. It also uses the ControlST software suite to
simplify maintenance, but retains a unique set of certified hardware and software blocks.
The ToolboxST application provides a means to lock or unlock the Mark VIeS for
configuration and safety instrumented function (SIF) programming.
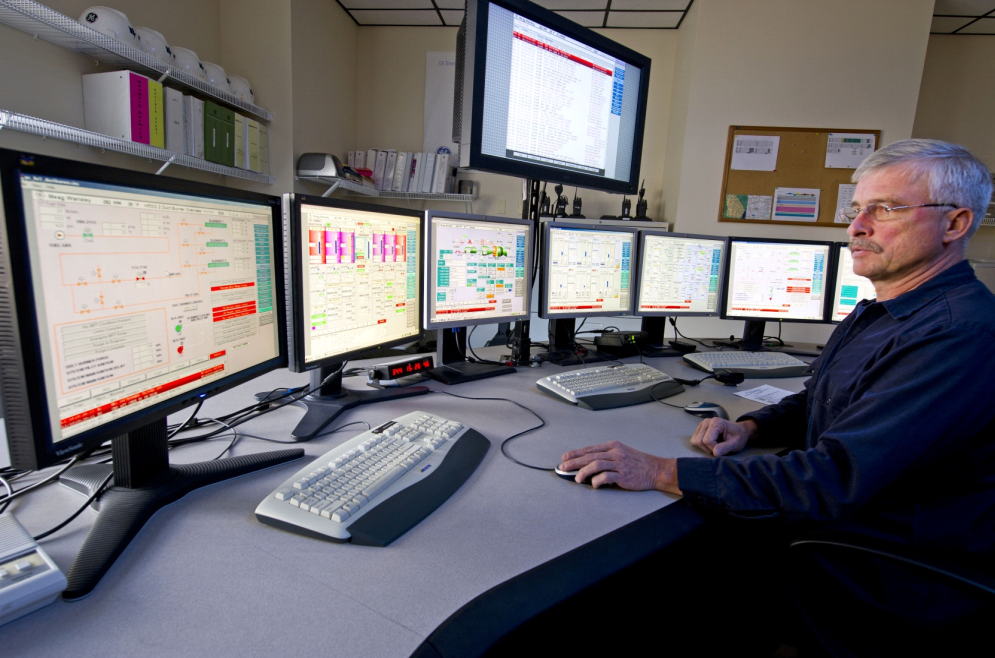
System Overview
A single-board controller is the heart of the system. The controller includes the main
processor and redundant Ethernet drivers to communicate with networked I/O, and
additional Ethernet drivers for the control network. A real-time, multi-tasking operating
system is used for the main processor and I/O modules. Control software is provided in a
configurable control block language and stored in non-volatile memory. It is similar to
IEEE® 854 32-bit floating-point format, and Sequential Function Charts (SFC) are also
available for complex sequencing.
100 MB Ethernet is used for
communication to local and
distributed I/O modules.
The I/O network (IONet) is a dedicated, full-duplex, point-to-point protocol. It provides a
deterministic, high-speed 100 MB communications network that is suitable for local or
distributed I/O devices, and provides communication between the main controllers(s) and
networked I/O modules. Online controllers continuously read input data directly from the
IONet, which is available in single, dual, and triple redundant configurations. Both copper
and fiber interfaces are supported.
The Mark VIe I/O modules consist of three basic parts: the terminal board, the terminal
block, and an I/O pack. Barrier or box-type terminal blocks are mounted on a terminal
board, which mounts on a DIN rail or base in the control cabinet. The I/O pack contains
two Ethernet ports, a power supply, a local processor, and a data acquisition board. I/O
capability grows as I/O packs are added to the control system, enabling use in a simplex,
dual, or triple redundant configuration. Some process sub-systems require even more
throughput; therefore, the local processors in each I/O pack run algorithms at higher rates
as required for the application.
Redundancy
Every application has different requirements for redundancy depending on the criticality
of the process. The Mark VIe control system provides a wide range of redundancy options
for local and remote distribution.
Redundancy Options
Control Components Redundancy Level
Power sources Single Dual Triple
Power supplies Single Dual Triple
I/O packs per I/O module Single N/A Triple
Ethernet ports per I/O pack Single Dual N/A
IONet Single Dual Triple
Control Network Single Dual N/A
Dual redundant systems transmit inputs from single or redundant input packs on dual
IONets to dual Mark VIe controllers. Controllers then run application software and
transmit outputs to output packs. Three output I/O packs may be provided to vote output
signals for mission-critical field devices. Dual redundant systems may be configured for
single, dual, and triple redundant sensors.
Triple redundant systems protect against soft or partial device failures. A failed
component is outvoted with a 2-out-of-3 logical selection (vote) or a median value
selection. Control software in all three Mark VIe controllers runs on the voted value of
the signal while diagnostics identify the failed device. These sophisticated diagnostics
reduce the mean-time-to-repair (MTTR) while the online repair capability increases the
mean-time-between-forced-outages (MTBFO). Field sensors for these systems may be
single, dual, or triple.
I/O Interface
Every I/O pack communicates
directly over the IONet, which
enables each I/O pack to be
replaced individually without
affecting other I/O packs in the
system. Additionally, the I/O
pack may be replaced without
disconnecting any field wiring.
One or multiple I/O packs are mounted on each module to digitize the sensor signal, run
algorithms, and communicate with a separate controller containing the main processor.
I/O packs have a local processor board that runs a real-time operating system and a data
acquisition board that is unique to the specific I/O application. Local processors run
algorithms at faster speeds than the overall control system, such as the regulation of servo
valves performed within a servo module.
Each I/O processor has a local temperature sensor accurate to ±2°C (±3.6 °F). Detection
of an excessive temperature generates a diagnostic alarm and the logic is available in the
database (signal space) to facilitate control action or unique process alarm messages. The
temperature is continuously available in the database. I/O module features include:
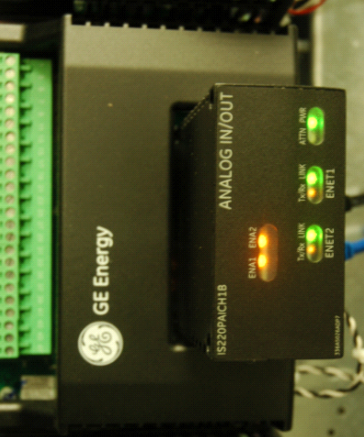
Dual 100 MB Ethernet ports
• 100 MB full-duplex ports
• Online repair per I/O pack
• Automatic reconfiguration
• Accuracy is specified over full operating
temperature
• Internal temperature sensor
• LEDs:
− Power status and attention
− Ethernet link-connected and
communication-active
− Application-specific
• 28 V dc power
• Internal solid-state circuit breaker and soft start
A power supply provides a regulated 28 V dc power feed to each I/O pack. The negative
side of the 28 V dc is grounded through the I/O pack metal enclosure and its mounting
base. The positive side has solid-state circuit protection built into the I/O pack with a
nominal 2 A trip point. Online repair is possible by removing the 28 V dc connector,
replacing the I/O pack, and re-inserting the power connector. I/O packs are automatically
reconfigured if the Auto-Reconfiguration feature is enabled.