GE FANUC H-6721 Control Systems
The Mark VIeS Safety controller and I/O can operate independently or integrated with the rest of the Mark VIe controllers for
safety-critical applications that conform to IEC® 61508.
The ControlST* Software Suite, which contains the ToolboxST* application software, is used or programming, configuration,
trending, and analyzing diagnostics for Mark controls and related systems. It provides quality, time-coherent data at controller
and plant level for effectively managing control system equipment. ControlST simplifies maintenance while retaining a
unique set of certified hardware and software blocks. ToolboxST provides a means to lock or unlock the Mark VIeS Safety
controller for configuration and Safety Instrumented Function (SIF) programming
The Universal I/O (UIO) control cabinet provides a platform for an independent, miniature version of the Mark VIe or Mark
VIeS Safety control. The PUAA module is the standard Mark VIe compatible module, while the YUAA module is the
companion module that is used in the Mark VIeS Safety control system. The UIO control cabinet is a lower cost, smaller
footprint alternative to the standard Mark control cabinet. The control cabinet is installed at sites when there are I/O, power,
and/or space limitations in the existing Mark VI, Mark VIe, or Mark VIeS control cabinet. This is especially required for
upgrades when there are space restrictions. This unit may also be used as an independent Mark VIe or Mark VIeS control
system, communicating directly with the Unit Data Highway (UDH) or Plant Data Highway (PDH), regardless of the existing
controller at the site. The UIO control system supports specific I/O. For a list of supported I/O, refer to the Mark VIe and
Mark VIeS Control Systems Volume II: System Guide for General-purpose Applications (GEH-6721_Vol_II). ToolboxST is
used to set up, configure, and download to the UIO Mark VIe controller.
The information in this document applies to the overall Mark* VIe control system or
Mark VIeS Functional Safety System control products; however, your application may
not be licensed to access full system capability and I/O packs as described in this
document. For example, the Mark VIeS Functional Safety System for General
Markets only utilizes the following I/O packs:
•• Analog I/O (YAIC)
•• Universal Analog (YUAA)
•• Vibration Input Monitor (YVIB)
•• Relay Output (YDOA)
•• Discrete Contact Input (YDIA)
•• Power Distribution System Diagnostics (PPDA)
•• Serial Modbus Communication (PSCA)
•• Mark VIeS Safety Controller (UCSCS2x)
•• Mark VIe Controller for Gateway (UCSCH1x)
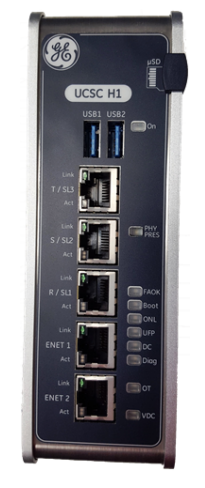
The Mark VIe controller is a stand-alone, single-board controller with scalable
processing power. It includes built-in power supplies and requires no batteries or
jumper settings. Controllers run the ControlST* Software Suite, providing a common
software environment for turbine and generator excitation controls in the power island
and balance of plant equipment to simplify operations and maintenance.
The Mark VIeS Safety controller is IEC 61508 certified to SIL 3.
Controllers are loaded with software specific to its application, such as steam, gas,
land-marine (LM), Balance of Plant (BoP), offshore drilling, desalination, CS, and
Wind Power Conversion. It can run Relay Ladder Diagrams (RLD) or blocks. The
IEEE® 1588 protocol is used through the R, S, and T I/O networks (IONet) to
synchronize the clock of the I/O modules and controllers to within ±100 microseconds.
Data is transferred to and from the control system database in the controller over the
I/O networks (IONet). IONet data includes process inputs/outputs to the I/O packs.
In a dual system, IONet data also includes:
• Internal state values and initialization information from the designated controller
• Status and synchronization information from both controllers
In a triple module redundant (TMR) system, IONet data also includes:
• Internal state values for voting and status and synchronization information from all
three controllers
• Initialization information from the designated controller
GE’s Industrial Ethernet 10/100 switches (ESWA and ESWB) provide the performance and features needed in today’s
real-time industrial control systems. Use 8-port ESWA or 16-port ESWB Ethernet switches in all control system I/O networks
to maintain the reliability needed for I/O module reception of controller outputs.
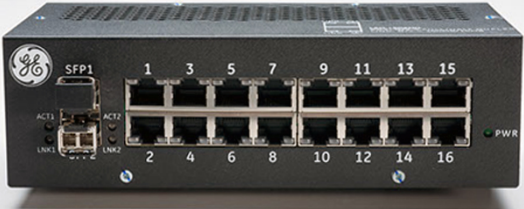
The I/O modules contain three basic parts: terminal board, terminal block, and I/O pack.
The terminal board mounts to the cabinet and comes in two basic types: S and T. The I/O
pack mounts to the terminal board J-port connector. Both terminal board types provide the
following features:
• Terminal blocks for I/O wiring
• Mounting hardware
• Input isolation and protection
• I/O pack connectors
• Unique electronic ID
I/O packs have a common processor board and a data acquisition board that is unique
to the type of connected device. I/O packs on each terminal board digitize the I/O
variables, perform algorithms, and communicate with the controller.
The I/O pack provides fault detection through a combination of special circuitry in the
data acquisition board and software running in the Central Processing Unit (CPU)
board. The fault status is transmitted to and used by the controllers. The I/O pack
transmits inputs and receives outputs on both network interfaces if connected.
Each I/O pack also sends an identification message (ID packet) to the main controller
when requested. The packet contains, the hardware catalog number of the I/O board,
the hardware revision, the board barcode serial number, the firmware catalog number,
and the firmware version. The I/O packs have a temperature sensor that is accurate to
within ±2 °C (±3.6 °F). Every I/O pack temperature is available in the database and can
be used to generate an alarm.