Honeywell 120/240VAC, 60W 900P01-0101
Table 15 Host ConnectionsItem Description
Connection Status Shows condition of each virtual connection.
See Host Connection Diagnostics Status Indicators, Table 16
Protocol The protocol used by the host to communicate with the controller (Modbus TCP).
IP Address The IP address of the host device that is using this connection.
Messages Received Number of messages received without errors.
Application Errors Number of message requests that resulted in an exception.
Clear Statistics Resets to zero the number of messages received and application errors.
Table 16 Host Connection Status Indicators
Status Possible Cause Controller Action What to do
GOOD N/A N/A N/A
APPLICATION
ERROR
At least one response to
a host resulted in an
exception code.
1. Rack 1 monitor
block's COMPORT
DIAG is set to
WARNING.
2. Rack 1 monitor
block's RACK OK
pin is turned off.
3. ASYS block's HW
OK pin is turned off
At host, determine which message
is causing the exception code and
fix.
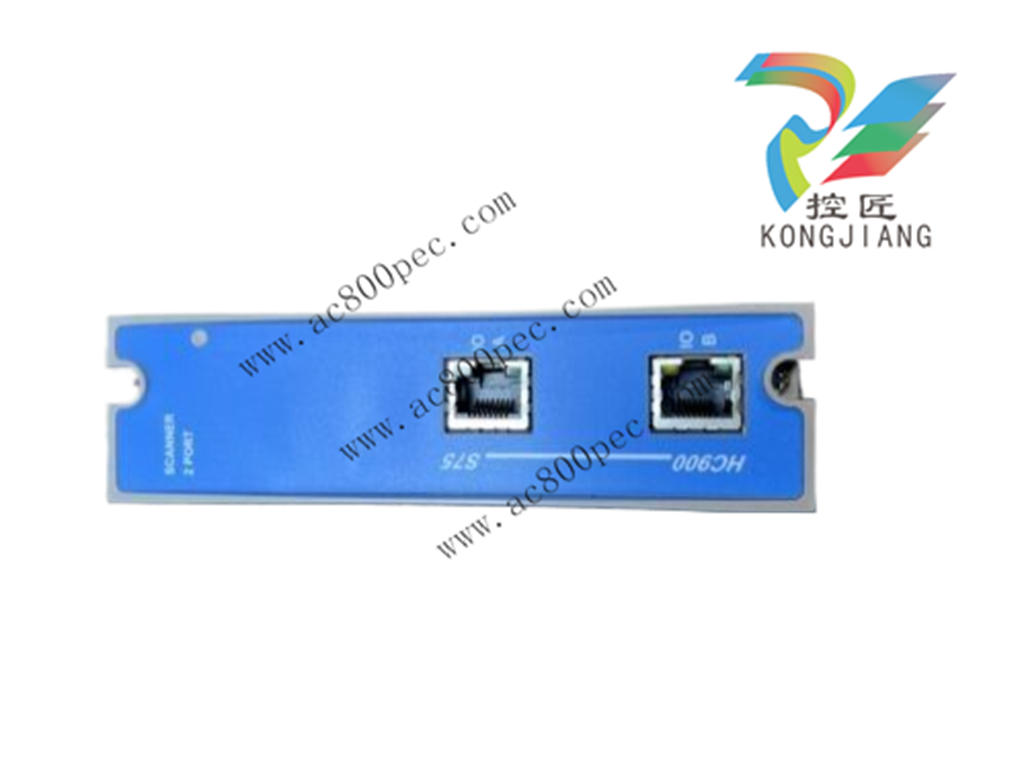
Table 17 Peer Connections
Item Description
Peer Controller Name Controller name of the peer device. All peer devices must have the same network
name. All peer devices that share a common network name must have unique
controller names.
IP Address IP address of the peer. The IP address is automatically determined when a peer
device is discovered via its network and controller names.
Peer Status See Peer Connection Status Indicators, Table 18.
Messages Received Number of messages received from the peer device.
Messages Transmitted Number of messages sent to the peer device.
Write Requests Number of write event messages sent to the peer device.
Write Request Failures Number of write event messages that have not been acknowledged by the peer device
within the scan rate configured for the peer data exchange. A non-zero value means
the network is congested and message transfer is being impeded.
Producer Failures Number of times the peer device has not responded to a data exchange connection
request. Non-zero value means the peer device is not available because the controller
is in Program mode, controller power is off, or controller name does not exist in the
network. The network is defined as all devices that:
• are on the same physical network,
• are within the IP address range per the configured IP mask,
• share the same peer network name.
Clear Statistics Reset to zero the number of messages received and application errors.
Table 18 Peer Connection Status
Status Possible Cause Controller Action What to do
GOOD N/A Peer is connected and
updating normally
N/A
APPLICATION
ERROR
The peer connection
could not be
established due to an
internal program
problem.
N/A 1. Reset the controller to restart
the UDP/IP protocol stack and
reset buffer allocations.
2. Contact Honeywell Technical
Assistance if the problem
exists.
SETUP ERROR The peer device
indicated that the one
or more data item is
not valid.
The error will occur when
an incompatibility exists
between peer devices with
regard to variable or signal
assignments.
This error should not
occur when exchanging
data between HC900
controllers.
Contact Honeywell Technical
Assistance if the status occurs.
PEER FAIL The assigned peer
could not be located on
the network.
N/A 1. Check the controller name and
network name of the peer
device to assure that they
match that specific PDE block.
2. Check that the IP addresses of
the peer devices are all within
the range of the IP mask.
3. Check that the peer devices
have the same IP subnet mask.
See Network parameters for IP
mask setting.
PORT FAIL The peer data
exchange IO
subsystem could not
be started due to
internal resource
problem.
N/A 1. Reset the controller to restart
the Ethernet IO hardware and
reassign processor IO
mapping.
2. Contact Honeywell Technical
Assistance if the problem
exists.
NOT STARTED The assigned peer IO
connection has not yet
been attempted.
Normal state during
startup and during
configuration mode.
This status should
automatically change
to GOOD after both
peer controllers are in
the RUN mode.
1. If this status persists during run
time, check that the peer
device is properly connected
and that the control name and
network name is correct.
2. Check that the IP masks of all
peer devices to assure that all
IP addresses are within the
same subnet.
3. Check that all external network
components such as switches
and routers allow passing of
UDP packets on port 502.
4. Check that the peer device is
powered on and is in RUN
mode.