ADVANCED 120A10 Analog Servo Drive
The 120A10 PWM servo drive is designed to drive
brush type DC motors at a high switching frequency.
A single red/green LED indicates operating status. The
drive is fully protected against over-voltage, under
voltage, over-current, over-heating and short-circuits
across motor, ground and power leads. Furthermore,
the drive can interface with digital controllers or be
used stand-alone and requires only a single
unregulated DC power supply. Loop gain, current
limit, input gain and offset can be adjusted using 14-
turn potentiometers. The offset adjusting
potentiometer can also be used as an on-board input
signal for testing purposes.
Features
Optical Isolation Between High & Low Power
Signals
Four Quadrant Regenerative Operation
DIP Switch Selectable Modes
Differential Input Command
Digital Fault Output Monitor
On-Board Test Potentiometer
Offset Adjustment Potentiometer
Adjustable Input Gain
DIP Switch Selectable Tuning
Drive Status LED
Directional Inhibit Inputs for Limit Switches
MODES OF OPERATION
Current
Voltage
IR Compensation
Velocity
COMMAND SOURCE
±10 V Analog
FEEDBACK SUPPORTED
Tachometer (±60 VDC)
COMPLIANCES & AGENCY APPROVALS
UL
cUL
CE Class A (LVD)
CE Class A (EMC)
RoHS II
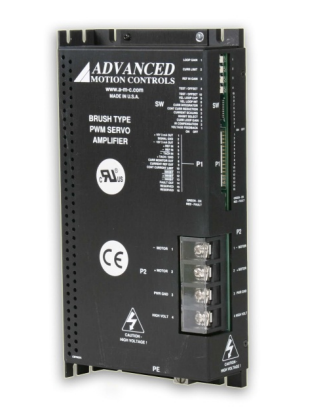
Switch Functions
Switch Description Setting
On Off
1 Voltage feedback. Mode dependent (see mode selection table
below). On Off
2 IR compensation. Activates or deactivates IR feedback. ON for
IR compensation mode and OFF for other modes. On Off
3 Current loop proportional gain adjustment. ON by default. Decrease Increase
4 Inhibit logic. Sets the logic level of inhibit pins. Active Low Active High
5
Current scaling. When OFF, increases sensitivity of current sense
thus reducing both peak and continuous current limit by 50%.
The scaling of the current monitor output signal becomes ½ its
ordinary value when this switch is OFF.
Full-current Half-current
6 Current limit ratio. Used to set continuous-to-peak current limit
ratio. Default is OFF. Cont./Peak Ratio = 25% Cont./Peak Ratio = 50%
7 Current loop integral gain. Activates or deactivates integration.
OFF by default. Inactive Active
8 Outer loop integration. Activates or deactivates integration. ON,
by default, for current mode and OFF for other modes. Inactive Active
9
Outer loop integral gain adjustment. It is recommended to leave
this switch OFF for most applications, but ON for Hall Velocity
Mode.
Decrease Increase
10
Test/Offset. Switches the function of the Test/Offset pot between
an on-board command input for testing or a command offset
adjustment. OFF by default.
Test Offset
Mode Selection Table
Mode SW1 SW2 SW8 Tachometer
CURRENT OFF OFF ON Not Connected
VOLTAGE ON OFF OFF Not Connected
IR COMPENSATION ON ON OFF Not Connected
TACHOMETER VELOCITY OFF OFF OFF Connected
Potentiometer Functions
Potentiometer Description Turning CW
1 Loop gain adjustment for voltage/velocity modes. Turn this pot
fully CCW in current mode. Increases gain
2
Current limit. It adjusts both continuous and peak current limit
while maintaining the continuous/peak ratio set by the
dipswitches.
Increases limit
3 Reference gain. Adjusts the ratio between input signal and output
variables (voltage, current, or velocity). Increases gain
4
Offset / Test. Used to adjust any imbalance in the input signal or in
the amplifier. Can also be used as an on-board signal source for
testing purposes.
Adjusts offset in negative direction
Note: Potentiometers are approximately linear and have 12 active turns with 1 inactive turn on each end.