GE FANUC Mark* VIe Control
Mark* VIe is a flexible control system for multiple applications. It features high speed, networked I/O for simplex, dual, and triple redundant systems. Industry standard Ethernet
communications are used for I/O, controllers, and supervisory
interface to operator and maintenance stations, and third-party systems.
ToolboxST* is used for Mark VIe and related controls as a common software
platform for programming, configuring I/O, trending, and analyzing diagnostics. It
provides a single source of quality, time-coherent data at the controller and plant
level for effectively managing equipment assets.
A single-board controller is the heart of the system. It includes the main processor
and redundant Ethernet drivers for communicating with networked I/O and
additional Ethernet drivers for the control network. A QNX® real-time, multitasking
operating system is used for the main processor and I/O. Application software is
provided in a configurable control block language, and is stored in non-volatile
memory. It conforms to IEEE-854 32-bit floating-point format.
IONet is a dedicated, full-duplex, point-to-point protocol that provides a
deterministic, high-speed 100 MB communications network suitable for local or
remote I/O with a fiber interface. It provides communication between the main
processor(s) and networked I/O blocks, called I/O packs.
100 MB Ethernet is used for
communication to local and
remote I/O packs. The IONet
is available in single, dual,
and triple configurations.
Each I/O pack is mounted on a board with barrier or box-type terminal blocks. The
I/O pack contains two Ethernet ports, a power supply, a local processor, and a data
acquisition board. Computation power grows as I/O packs are added to the control
system, enabling an overall control system frame rate of 10 ms in simplex, dual, or
triple redundant configuration. Some process sub-systems require even more
performance; therefore, the local processors in each I/O pack run algorithms at
higher rates as required for the application.
Redundancy
Every application has different requirements for redundancy depending on the
importance of the process. Mark VIe provides a wide range of redundancy options
that can be supplied in virtually any combination and mounted local or remote. Some
of these redundancy options include:
• Power sources and supplies single, dual, and triple
• Controllers (main processor) single, dual, and triple
• I/O network redundancy single, dual, and triple
• I/O packs per terminal board single, dual, and triple
• Ethernet Ports / I/O pack single or dual
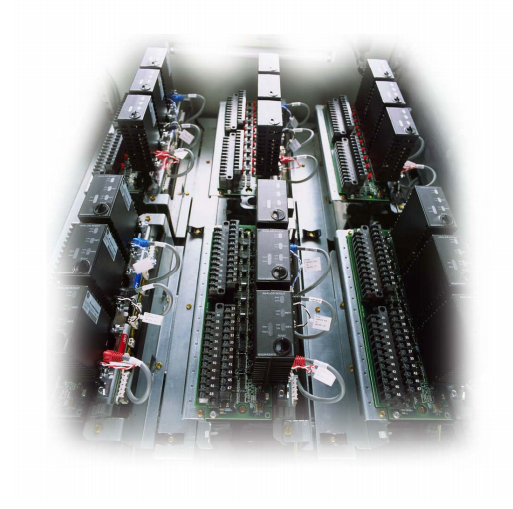
Controllers are continuously online and read input data directly from IONet. Dual
redundant systems transmit inputs from one or redundant I/O packs on dual IONets
to dual controllers. Outputs are transmitted to an output I/O pack that selects either
the first healthy signal or the signal of choice. Three output packs can be provided to
vote output signals for mission-critical field devices.
Dual redundant systems can be configured for single, dual, and triple sensors. Their
dual internal networks and controllers keep the process online if a controller or
power supply fails. Triple redundant systems are available to protect against soft or
partial failures of devices that continue to run but with incorrect signals/data.
These systems out vote a failed component with a 2-out-of-3 selection of the signal.
Application software in all three controllers runs on the voted value of the signal
while diagnostics identify the failed device. These sophisticated diagnostics
minimize the mean-time-to-repair (MTTR) while the on-line repair capability
maximizes the mean-time-between-forced-outages (MTBFO). Field sensors for these
systems can be single, dual, or triple.
A second controller can be provided to separate the application software for different
pieces of equipment. For example, a core engine control for an air-fuel governor can
run in one controller while a second controller can be dedicated to auxiliary control.
Note Every I/O pack communicates directly on IONet, which enables each I/O pack
to be replaced individually without affecting any other I/O in the system. Also, the
I/O pack can be replaced without disconnecting any field wiring.
I/O Interface
One or multiple I/O packs are mounted on each board to digitize the sensor signal,
perform algorithms, and communicate with a separate controller that contains the
main processor. I/O packs have a local processor board that runs a QNX operating
system and a data acquisition board that is unique to the type of input device. Local
processors run algorithms at faster speeds than the overall control system.
An on-board temperature sensor
provides continuous monitoring of
the environment in remote
locations.
An infrared transceiver is useful for low-level diagnostics. I/O values can be
monitored, I/O pack host/function names can be programmed, and error statuses can
be checked. This requires a Windows®-based diagnostic tool on a laptop or a
handheld computer.
• Dual 100 MB Ethernet ports
• 100 MB full duplex ports
• Online repair per I/O pack
• Operation -30°C to 65°C (-22 °F to 149 °F)
• Accuracy -30°C to 65°C (-22 °F to 149 °F)
• I/O packs rated Class 1, Div. 2
• Ambient temperature sensor
• LEDs: power status and attention
• LEDs: Ethernet link-connected and communication-active
• LEDs: application-specific
• Processor: 32-bit RISC CPU 266 mHz
• Infrared Transceiver: Low level diagnostics, monitor I/O,
set host/function names, error status
• Power: 28 V dc (typical)
• Internal solid-state circuit breaker and soft start
The I/O Processor contains a temperature sensor that is accurate to within ±2°C
(±3.6 °F). Detection of an excessive temperature generates a diagnostic alarm, and
the logic is available in the database (signal space) to facilitate additional control
action or unique process alarm messages. In addition, the temperature is
continuously available in the database.
A power supply provides a regulated 28 V dc power feed to each I/O pack. The
negative side of the 28 V dc is grounded through the I/O pack metal enclosure and its
mounting base. The positive side has solid-state circuit protection built-into the I/O
pack with a nominal 2 A trip point. Online repair is possible by removing the
28 V dc connector, replacing the I/O pack, reinserting the power connector, and
downloading software from the software maintenance tools.
Note Every I/O pack communicates directly on IONet, which enables each I/O pack
to be replaced individually without affecting any other I/O in the system. Also, the
I/O pack can be replaced without disconnecting any field wiring.
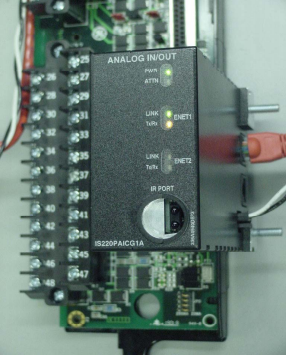
Terminal Blocks
Signal flow begins with a sensor connected to a terminal block on a board. There are
two types of boards available. T-type boards contain two 24 point, barrier-type,
removable, terminal blocks. Each point can accept two 3.0 mm2
(#12AWG) wires
with 300 V insulation per point with spade or ring type lugs. In addition, captive
clamps are provided for terminating bare wires. Screw spacing is 9.53 mm (0.375
inch) minimum, center-to-center.
A shield strip is provided next to each block, which is actually the left-hand side of
the metal base where the board is mounted. Wide and narrow boards are arranged in
vertical columns of high and low-level wiring that can be accessed from top and/or
bottom cable entrances. An example of a wide board is a board that contains
magnetic relays with fused circuits for solenoid drivers. T-type boards are normally
surface mounted, but can also be DIN-rail mounted.
Barrier and Box Type Boards with I/O Packs
S-type boards have one I/O pack for simplex and dual redundant systems. They are
half the size of T-type boards and are DIN-rail or surface mounted. Two versions of
the boards are available, H1 and H3. H1 boards have fixed terminal blocks, and H3
boards have removable terminal blocks. A H2 version is available for mounting of
custom blocks such as spring-cage or insulation displacement.
S-type boards have box type terminal blocks that accept one 3.0 mm2
(#12AWG)
wire or two 2.0 mm2
(#14AWG) wires with 300 V insulation per point. Screw
spacing is 5.08 mm (0.2 inch) minimum, center-to-center. A shield strip is provided
to the left of each block. It can be connected to a metal base for immediate grounding
or floated to allow individual ground wires from each board to be wired to a
centralized, cabinet ground strip.