ABB 07KT97H3 Programmable Processor Unit
5 Installation
Pneumatic connections
Air supply
Instrument air*
Purity Maximum particle size: 5 μm
Maximum particle density: 5 mg/m3
Oil content Maximum concentration 1 mg/m3
Pressure dew point 10 K below operating temperature
Supply pressure** Standard design:
1.4 to 6 bar (20 to 90 psi)
Marine version:
1.6 to 5.5 bar (23 to 80 psi)
Air consumption*** < 0.03 kg/h / 0.015 scfm
* Free of oil, water and dust in accordance with DIN / ISO 8573-1. Pollution
and oil content in accordance with Class 3
** Do not exceed the maximum output pressure of the actuator
*** Independent of supply pressure
6 Commissioning
Note
The electrical power supply and supply air pressure data
indicated on the name plate must be complied with during
commissioning.
CAUTION
Risk of injury due to incorrect parameter values!
Incorrect parameter values can cause the valve to move
unexpectedly. This can lead to process failures and result in
injuries.
• Before recommissioning a positioner that was previously
in use at another location, always reset the device to its
factory settings.
• Never start automatic adjustment before restoring the
factory settings!
Note
Please observe the information in Operation on page 32 to
operate the device!
Commissioning the positioner:
1. Open the pneumatic power supply.
2. Power-up the electric power supply and feed in the setpoint
signal 4 to 20 mA.
3. Checking mechanical mounting:
• Press and hold MODE; in addition, press or until
operating mode 1.3 (manual adjustment in the measuring
range) is displayed. Release MODE.
• Press or to move the actuator into the mechanical
end position; check the end positions; rotational angle is
displayed in degrees; for high-speed mode, press or
simultaneously.
Recommended rotational angle range
Linear actuators −28 to 28°
Rotary actuators −57 to 57°
Minimum angle 25°
4. Perform standard automatic adjustment in accordance with
Standard automatic adjustment on page 29.
Commissioning of the positioner is now complete, and the
device is ready for operation.
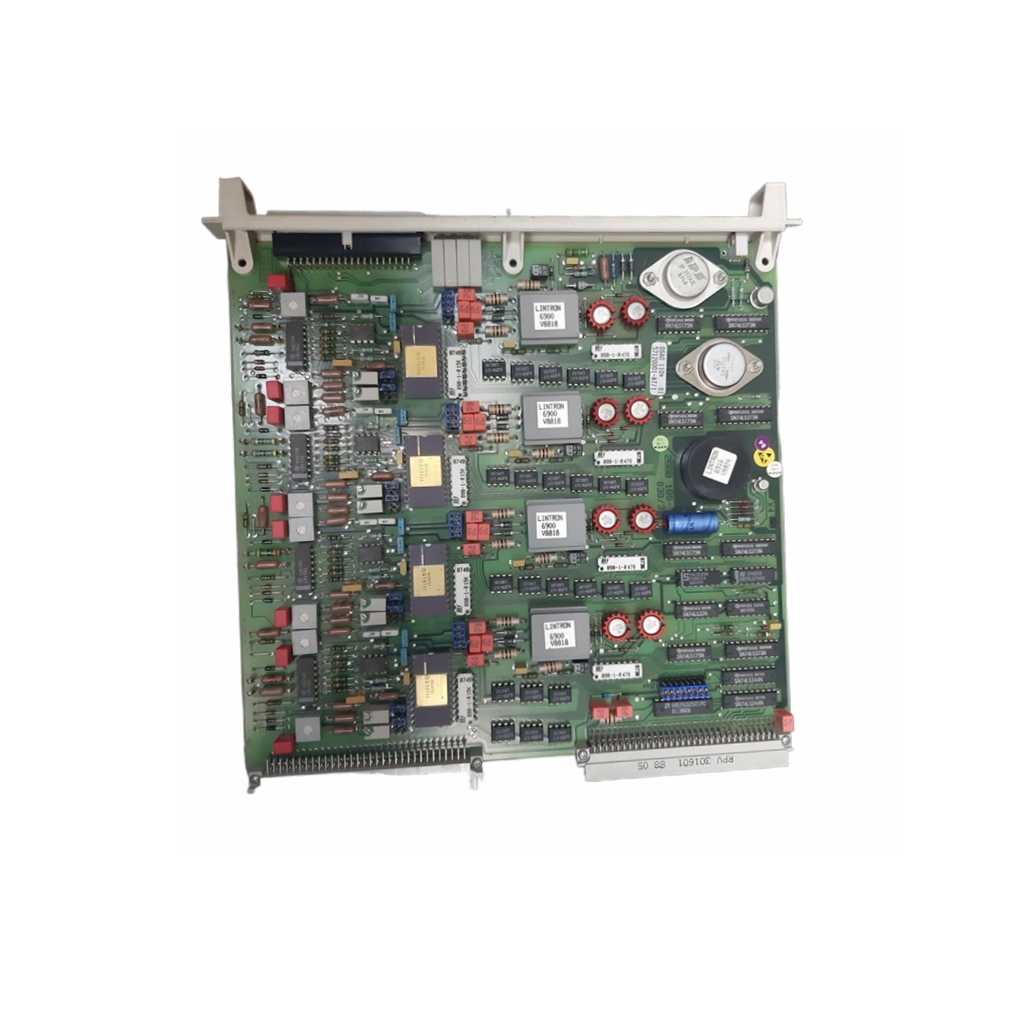
Operating modes
Selection from the operating level
1. Press and hold down MODE.
2. Also press and release rapidly as often as required. The
selected operating mode is displayed.
3. Release MODE.
The position is displayed in % or as a rotation angle.
Operating mode Mode indicator Position indicator
1.0
Control mode* with
adaptation of the control
parameters M10906a M10906f
1.1
Control mode* without
adaptation of the control
parameters M10906b M10906g
1.2
Manual adjustment** in
the operating range.
Adjust*** using or M10906c M10906g
1.3
Manual adjustment** in
the measuring range.
Adjust*** using or M10906d M10906h
* Since self-optimization in operating mode 1.0 is subject to several factors
during control operation with adaptation, incorrect adjustments could
appear over an extended period.
** Positioning not active.
*** For high-speed mode, press and simultaneously.
Standard automatic adjustment
Note
Standard Auto Adjust does not always result in optimum control
conditions.
Standard automatic adjustment for linear actuators*
1. MODE Press and hold until ADJ_LIN is displayed.
2. MODE Press and hold until the countdown ends.
3. Release MODE; this starts Autoadjust.
Standard automatic adjustment for rotary actuators*
1. ENTER Press and hold until ADJ_ROT is displayed.
2. ENTER Press and hold until the countdown ends.
3. Release ENTER; this starts Autoadjust.
If Autoadjust is successful, the parameters will be stored
automatically and the positioner will revert to operating mode
1.1.
If an error occurs during Autoadjust, the process will be
terminated with an error message.
Perform the following steps if an error occurs:
1. Press and hold down operating button or for
approximately three seconds.
The unit will switch to the operating level, mode 1.3 (manual
adjustment within the measuring range).
2. Check mechanical mounting in accordance with Mechanical
mounting on page 13 and repeat the standard automatic
adjustment.
* The zero position is determined automatically and saved during standard
automatic adjustment, counter-clockwise (CTCLOCKW) for linear actuators
and clockwise (CLOCKW) for rotary actuators
6 Commissioning
Sample parameters
‘Change the zero position of the LCD display from clockwise
(CLOCKW) to counter-clockwise limit stop (CTCLOCKW)’
Initial situation: the positioner is in bus operation on the
operating level.
1. Switching to the configuration level:
• Press and hold down and simultaneously,
• additionally quickly press and release ENTER,
• Wait for the countdown to go from 3 to 0,
• Release and .
The following is now shown in the display:
M10906i
2. Switching to parameter group 3._:
• Press and hold down MODE and ENTER simultaneously,
• additionally quickly press and release 2×,
The following is now shown in the display:
M10906j
• Release MODE and ENTER.
The following is now shown in the display:
M10906k
3. Selecting parameter 3.2:
• Press and hold down MODE,
• additionally quickly press and release 2×,
The following is now shown in the display:
M10906l
— Release MODE.
4. Changing parameter settings:
• Quickly press and release to select CTCLOCKW.
5. Switching to parameter 3.3 (Return to operating level) and
saving the new settings:
• Press and hold down MODE,
• additionally quickly press and release 2×,
The following is now shown in the display:
M10906m
• Release MODE,
• Quickly press and release to select NV_SAVE,
• Press ENTER and hold down until the countdown goes
from 3 to 0.
The new parameter setting is saved and the positioner
automatically returns to the operating level. It continues in the
operating mode that was active prior to the configuration level
being called up.
Setting the option modules
Setting the mechanical position indication
1. Loosen the screws for the housing cover and remove it.
2. Rotate the position indicator on the shaft to the desired
position.
3. Attach the housing cover and screw it onto the housing.
Tighten the screws so that they are hand-tight.
4. Attach the symbol label to mark the minimum and maximum
valve positions on the housing cover.
Note
The labels are located on the inside of the housing cover.