Honeywell Low VoltageTerminal Block (Barrier Style) Note 3 900TBK-0101
Each I/O module includes a status indicator for the module. Digital Input and Digital Output modules alsoinclude a status indicator for each channel. Terminal blocks available include the Euro style (Error!
Reference source not found. left) and the Barrier style (Error! Reference source not found. right).
For more information on I/O modules and associated terminal blocks, refer to the section in this manual on
Input/Output Installation and Wiring.
Personal Computer
A Personal Computer is required to create the control and data acquisition strategy (configuration file) that
runs in the controller, using the Designer configuration software. The PC can also be used to
download/upload configuration files to/from the controller, and can be used to download program updates
to firmware in the Controller Module and/or Scanner Modules.
A PC can be connected to the controller via the RS-232 port for legacy system.
For the new system, a PC can be connected to the controller via the RS-485 to USB cable connected to
RS485 Port , which can be connected to external Honeywell qualified RS485 to USB converter, and can
also be networked to the controller via the Ethernet 10/100Base-T Open Connectivity Network port.
Redundant controllers: PC communicates with Lead Controller only.
NOTE: For specific PC requirements and for specific software requirements, refer to the Designer Software
Users Manual.
RS-232 Modem Devices
In Legacy systems the PC configuration tool can connect from the RS-232 serial port of the Controller
Module to a serial port on the PC.
For new system, the PC Configuration tool connects to the galvanically isolated RS-485 port on the
Controller Module using an external Honeywell qualified RS-485 to USB converter.
The PC can be located remote from the Controller by using Modems and telephone links. Modems and
suitable cabling are available from third-party vendors.
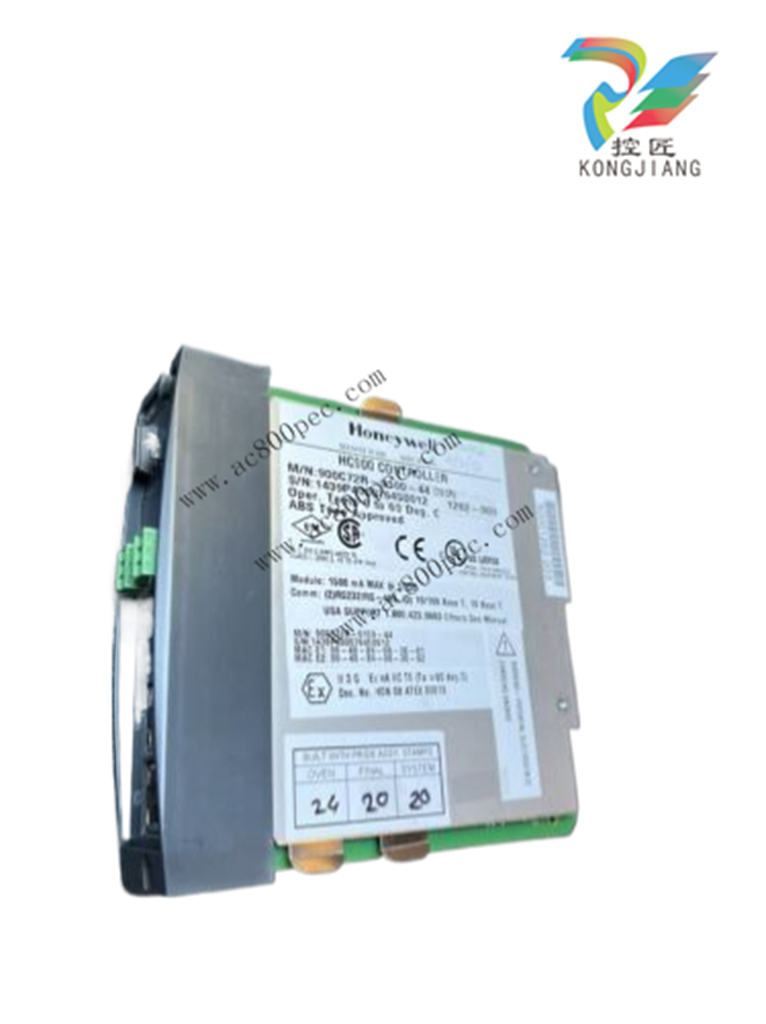
Figure 18 – HC900 Controller Configurations
In any of the racks shown in each controller configuration can be 4-, 8-, or 12-slot versions.
The Ethernet cables for the I/O expansion links are standard shielded Cat 5 cables, with standard RJ45
connectors. Each cable segment can be up to 100 meters (328 feet) long.
You can also use fiber optic cable for connections between the controller and a remote rack. Please refer to
HC900 specification document (51-52-03-31) for more details.
Configuration 1 is the C30/C30S/C50/C50S/C70/C70S CPU with I/O but no I/O expansion racks.
Configuration 2 shows the C50/C50S/C70/C70S CPU with 1 I/O expansion rack. The Ethernet cable
connects directly between the 10/100 Base-T connectors on the C50/C70 CPU Controller Module and the
Scanner Module.
ATTENTION:
For 2 or more I/O expansion racks a switch is required. Use only Honeywell recommended switches
(part no. 50008930-001, 50089785-001). The total number of switches is limited to 2 in series between
a CPU and its scanners.
Configuration 3 shows the C50/C50S/C70/C70S CPU with 3 I/O expansion racks. Since there are at least 2
I/O expansion racks a switch is required. When an Ethernet switch is used to connect to expansion I/O, a
cable goes between the I/O port on the controller to the switch. Two cables go from the switch to 2
scanners. A third cable goes from the switch to a second switch, which connects to a third remote scanner.
I/O implementation requirements include:
Constructing a configuration file, and loading it into the Controller Module. This file includes I/O
numbering assignments for each I/O Function Block regarding Rack Number, Module Number ("slot"
number, or position in the rack, starting from the left), and Channel Number.
Physically assigning Rack Numbers, by positioning DIP switch settings in the Scanner Module for each
rack.
Placing the appropriate module type in each slot in each rack.
The I/O expansion network uses Honeywell private protocol that optimizes I/O performance and security.
The configuration and operation of the I/O expansion network is automatic, it is entirely under control of
built-in private software that resides in the Controller Module and in each Scanner Module included in the
HC900 system. The controller examines the control strategy stored in its memory, verifies that the physical
configuration (Rack Numbers and I/O Module type- by Module Number) matches the stored control
strategy, and establishes communication with each of the I/O modules in each of the I/O racks.
I/O Expansion Network (C75 /C75S)
I/O for redundant controllers is the same as I/O Expansion Network page 33, with the following
exceptions/notes.
In Figure 18, any of the racks shown in each controller configuration can be 4-, 8- or 12-slot versions.
Redundant I/O power not available with 4-slot.
Double the amount of Switches and Ethernet cables are required to configure the redundant I/O Link.
Maximum of 2 switches between each CPU (CPU A and CPU B) and the I/O racks.
Ethernet Open Connectivity Network
The configuration of the Ethernet Open Connectivity Network varies with specific applications in purpose
and in complexity. In some applications, configuration is straightforward and within the capabilities of
experienced installation technicians. In other applications (for example, those that include inter-connection
to other networks such as Intranet and Internet), a working knowledge of networking is required.
The Ethernet Open Connectivity Network for a given HC900 Controller enables:
Redundant Networks.
Peer-to-peer communication (Safety peer communication for SIL controller from release 6.300)
Connection to other PC hosts
Inter-connection to other networks (such as for sending Alarm/Event messages via e-mail.)
These ports are to be considered part of the control network layer and as such care must be taken to
reduce exposure to uncontrolled network influences. A properly configured firewall such as the
MOXA EDR-810 is recommended to help mitigate.
CAUTION
Communications lockout is possible in high network traffic conditions.
Extraneous traffic is possible when sharing bandwidth with other devices. We recommend putting the
controller on a private network segment. Failure to do so could, in high traffic cases, result in
communications lockout requiring the controller to be power-cycled.