The PACMotion controller is a versatile servo motion controller that combines the benefits
of a highly integrated motion and machine logic solution with the performance, flexibility
and scalability required for advanced machine automation. PACMotion is designed to
deliver unsurpassed machine productivity required for today’s high-speed machines and
lean manufacturing environments. The 4-axis servo motion controller is built on a high
performance hardware platform, with a new enhanced motion engine, operating system,
and open standard integrated programming paradigm. Add to that world-class reliability
of FANUC servos and you have a motion system designed to give you the best productivity
and accuracy possible. Please see GE Intelligent Platforms Motion Solutions Catalog
GFA-483 for more information about motion offerings.
GE IC695PMM335 PACMotion Servo Control
PACSystems RX3i Programmable ControllersThe PACMotion controller is a versatile servo motion controller that combines the benefits
of a highly integrated motion and machine logic solution with the performance, flexibility
and scalability required for advanced machine automation. PACMotion is designed to
deliver unsurpassed machine productivity required for today’s high-speed machines and
lean manufacturing environments. The 4-axis servo motion controller is built on a high
performance hardware platform, with a new enhanced motion engine, operating system,
and open standard integrated programming paradigm. Add to that world-class reliability
of FANUC servos and you have a motion system designed to give you the best productivity
and accuracy possible. Please see GE Intelligent Platforms Motion Solutions Catalog
GFA-483 for more information about motion offerings.
PACMotion Servo Control
IC695PMM335
Product Name PACMotion Module
Lifecycle Status Active
Module Type Servo Motion
Backplane Support Universal Backplane Only. Uses PCI Bus.
Number of Slots Module Occupies on
Backplane 1
Motion Path Planning 1 ms, Consistent update regardless of the number of axes in the system
Position Loop Update Rate 500 µs, All axes in the RX3i rack are updated simultaneously
Velocity Loop Update Rate 125 µs, All axes in the RX3i rack are updated simultaneously
Torque Loop Update Rate 62.5 µs, All axes in the RX3i rack are updated simultaneously
Controlled Axes/Module 4 ßi, ßHVi or aHVi series servos are supported via a fiber optic interface
Master Axes/Module 1, Can be a virtual time-based or incremental encoder master
Servo Command Interface Fiber Optic 50 Mb/s FANUC Serial Servo Bus (FSSB)
Fiber Terminal Block Cable Length Max. 100 meters between nodes 400 meters maximum for a 4 axis system
Maximum Axes per RX3i
DC Power Supplies: 40 + 10 master axes
(Requires 16 slot backplane, CPU and 4 DC power supplies)
AC Power Supplies: 32 + 8 master axes
(Requires 16 slot backplane, CPU and 3 AC power supplies)
Position Resolution aHVi Series 1,048,576 counts/rev, ßi and ßHVi Series 65,536 or 131,072 counts/rev.
ß2i and larger motors support the higher resolution.
Feedback Type Incremental/Absolute Serial Encoder.
Optional battery backup required for absolute feedback mode.
Faceplate I/O
24V General Purpose Inputs: 4 optically isolated; source/sink
24V High-Speed Inputs: 2 optically isolated; source/sink Open circuit detection;
can be used to connect a quadrature master encoder (500 kHz max)
24V General Purpose Inputs/Outputs: 2 optically isolated; source/sink 125 mA
maximum output current each “Connecto” Plug-on Screw Terminal
Floating Point Support Yes, Double precision IEEE 754.
Module Hot Insertion/Removal Yes
Cam Profiles per Module 256 at one time. Up to 2048 profiles can be stored
in the RX3i file system for use by any module.
Synch/Delayed Start Up to 8 axes Axes can be on any module and
are synchronized over the backplane.
High Speed Position Capture ±2 Inputs per axis: ±1 count = 10 µs jitter
Connector Type Plug-on Screw Terminal and Fiber
Internal Power Used 5 VDC 0.45A @ 5 VDC; 1.1A & 3.3 VDC
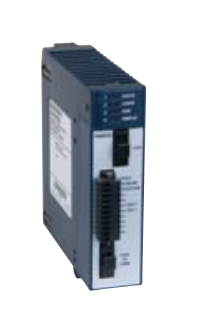