Honeywell Relay Output Remote Terminal Panel (RTP) Note 6 (NOT FOR SIL2 SYSTEMS) 900RTR-H001
2. For straight through cable, arrange wires as shown in the following table. Wires go “straight through”,no crossovers.
Straight-through cable assembly
Cable left end
Left to right
Wire color/pin number
10Base-T / 100Base-T
Signal Description
Cable right end
Left to right
Wire color/pin number
white/orange/1 Tx + white/orange/1
Orange/2 Tx - Orange/2
white/green/3 Rx + white/green/3
Blue/4 Unused Blue/4
white/blue/5 Unused white/blue/5
Green/6 Rx - Green/6
white/brown/7 Unused white/brown/7
Brown/8 Unused Brown/8
3. Crimp an RJ45 connector to each cable end. To ensure reliability do not untwist the pairs any more than
necessary to complete the crimp connection. Use care to ensure that the cable drain wire is securely
connected to the shield of the RJ45 connector when the cable is crimped. Reference the
manufacturer’s instructions.
Electrical Considerations
All racks should be mounted in an appropriate metal enclosure. A diagram that shows recommended
wiring practice for the cabinet enclosure is given in Figure 29 – Cabinet Wiring, Single Chassis, and Figure
30 – Cabinet Wiring, Multiple Chassis. When Redundant power supplies are used in Redundant controller
racks or I/O racks, separate line power sources are recommended to provide the highest level of redundancy
and system operation.
Deviations from the installation conditions specified in this manual may invalidate this product’s
conformity with Low Voltage and EMC.
Hazardous voltages exist in the equipment enclosure.
Identify and avoid contact with voltage sources.
Failure to comply with these instructions could result in death or serious injury.
Controller Grounding
PROTECTIVE BONDING (grounding) of this controller and the enclosure in which it is installed shall be
in accordance with National Electrical Code (ANSI/NFPA 70) and with local electrical codes.
Figure 29 – Cabinet Wiring, Single Chassis
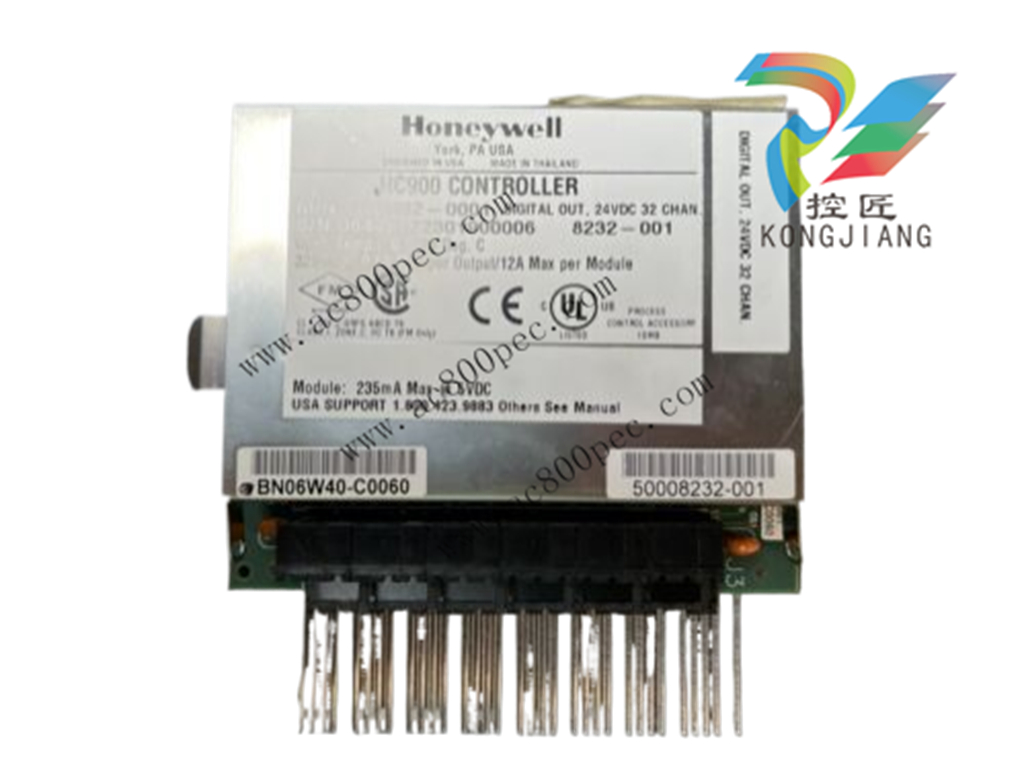
For P01 power supply use 3.0A, slow-blow for 115VAC operation; 2.5A, slow-blow for 230VAC
operation. For P02 power supply, use 2.5A, slow-blow for 115VAC operation; 2.0A, slow-blow for
230VAC operation. For P24 power supply use 7.0A slow-blow.
Figure 31 – Redundant power supplies each with external fuse and switch
CE Conformity
Electrical noise produces undesirable effects in measurements and control circuits.
Digital equipment is especially sensitive to the effects of electrical noise. You should use the following
methods to reduce these effects:
Supplementary bonding of the controller enclosure to a local ground, using a No. 12 (4 mm2
) copper
conductor, is recommended. This may help minimize electrical noise and transients that may adversely
affect the system.
Separate external wiring – group connecting wires into bundles (see Table 5) and route the individual
bundles through separate conduits or metal trays.
Use shielded twisted pair cables for all Analog I/O, Process Variable, RTD, Thermocouple, dc millivolt,
low level signal, 4-20 mA, Digital I/O, and computer interface circuits. Ground shields as described in
the section I/O Module Installation and Wiring page 77.
Use suppression devices for additional noise protection. You may want to add suppression devices at the
external source. Appropriate suppression devices are commercially available.
Refer to document 51-52-05-01 How to Apply Digital Instrumentation in Severe Electrical Noise
Environments for additional installation guidance.
Grouping Wires for Routing
Wires that carry relatively high electrical energy can produce unwanted noise in wires that transmit signals
of relatively low energy, particularly when they are placed parallel in long wiring runs. Collect and bundle
wires of similar type, and route the bundle separate from bundles of other types. Table 6 provides
suggested guidelines for grouping wires.
Table 5 – Guidelines for Grouping Wires
Wire Group Wire Functions
High voltage
(>50 Vdc/Vac)
AC Line power wiring
Earth ground wiring
Control relay output wiring
Line voltage alarm wiring
Signal
(<15 Vdc)
Analog signal wire, such as:
Input signal wire (thermocouple, 4 mA to 20 mA, etc.)
4-20 mA output signal wiring
Slidewire feedback circuit wiring
Communications
Low voltage
(<50 Vdc/Vac)
Low voltage alarm relay output wiring
Low voltage wiring to solid state type control circuits
Master Control Relay
A Master Control Relay (MCR) structure is a safety mechanism for shutting down the process control
system in emergency conditions. This mechanism, which is hard-wired (provided and installed by the
User) can include several Emergency Stop switches., strategically located near process equipment. An
example of an MCR structure is given in Figure 32.
Operating any of the Emergency-Stop switches opens the holding path for the MCR. When the MCR
de-energizes, the MCR contact opens, disconnecting all AC power that is supplied to AC Input Modules
and to AC Output Modules. Notice that AC power is disconnected only from the AC input/output modules.
Power is still available to Power Supplies at the Controller Rack and at each I/O expansion rack. The
Controller Module and the Scanner Modules in the racks continue to execute diagnostics and other
programs.
The Master Control Relay does not remove power from the Controller rack or from any of the I/O
expansion racks.
Before performing service tasks such as installation of terminal connections or fuse
replacement, use the appropriate switch(s) to disconnect power from the power supply at each
module.
Ensure that wiring design precludes over-riding of the MCR by operator actions.
Failure to comply with these instructions could result in death or serious injury.
Class 1, Division 2 Installations
DO NOT REMOVE OR REPLACE MODULES WHILE CIRCUIT IS LIVE UNLESS
THE AREA IS KNOWN NOT TO CONTAIN FLAMMABLE VAPORS.