ABB AO2000-LS25 Laser analyzers
The analyzer is an optical instrument for continuous in-situ gas monitoring in stack, pipes,
process chambers or similar and is based on tunable diode laser absorption spectroscopy
(TDLAS). The analyzer utilizes a transmitter/receiver configuration (mounted diametrically
opposite each other) to measure the average gas concentration along the line-of-sight path.
The measuring principle is infrared single-line absorption spectroscopy, which is based on
the fact that each gas has distinct absorption lines at specific wavelengths. The measuring
principle is illustrated in Figure 1-1. The laser wavelength is scanned across a chosen absorp tion line of the gas to be measured.
The absorption line is carefully selected to avoid cross
interference from other (background) gases. The detected light intensity varies as a function
of the laser wavelength due to absorption of the targeted gas molecules in the optical path
between transmitter and receiver. In order to increase sensitivity the wavelength modulation
technique is employed: the laser wavelength is slightly modulated while scanning the absorp tion line. The detector signal is
spectrally decomposed into frequency components at har monics of the laser modulation frequency. The second harmonics
of the signal is used tomeasure the concentration of the absorbing gas. The line amplitude and line width are both
extracted from the second harmonics line shape, which makes the measured concentration
insensitive to line shape variations (line broadening effect) caused by background gases.
NOTE: The analyzer measures the concentration of only the FREE molecules of the specific
gas, thus not being sensitive to the molecules bound with some other molecules into com plexes and to the molecules attached to or
dissolved in particles and droplets. Care should be
taken when comparing the measurements with the results from other measurement tech niques.
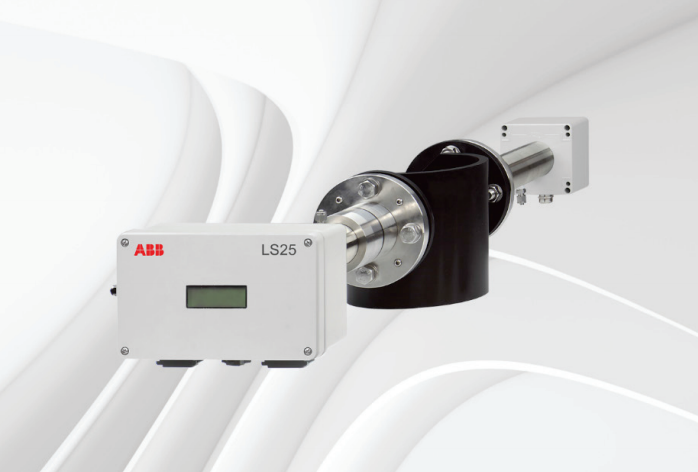
1.3 Instrument description
The analyzer consists of 3 separate units (see Figure 1-2):
Transmitter unit with purging
Receiver unit with purging
Power supply unit
Transmitter unit
The transmitter unit contains the laser module with a temperature stabilized diode laser, col limating optics, and the main electronics in a coated Aluminum box.
The receiver unit con tains a focusing lens, the photodetector and the receiver electronics in a coated Aluminum
box. Both transmitter and receiver units have environmental protection IP66, and the standard op tical windows withstand pressures up to 5 bar (absolute pressure). The monitor is installed
by assembling the transmitter and receiver units with the supplied purging & alignment
units, which in turn are mounted onto the DN50 process flanges (see
Figure 3-1). The optical alignment is easy and reliable, and the purging prevents dust and
other contamination from settling on the optical windows.
A block diagram of AO2000-LS25 is shown in Figure 1-3.
The power supply unit transforms 100-240 V AC to 24 V DC (if 24 VDC is available it can be
supplied directly to the transmitter unit). The power supply box is connected to the transmit ter box with a cable. The 4–20 mA input signals from external
gas temperature/pressure sen sors can be connected to the screw terminals inside the power box or directly to the cable
connector on the transmitter unit.
The receiver electronics is connected with the transmitter electronics with a cable. The de tected absorption signal from the photodetector is amplified and
transferred to the trans mitter unit through this cable. The same cable transfers the required power from the trans mitter unit to the receiver unit.
The transmitter Al box contains the major part of the electronics. The CPU board performs all
instrument control and calculation of the gas concentration. The main board incorporates all
electronics required for instrument operation such as diode laser current and temperature
control and analogue-to-digital signal conversion. A display (LCD) continuously displays the
gas concentration, laser beam transmission and instrument status. The RS-232 port can be
used for direct serial communication with a PC. The optional Ethernet board provides TCP/IP
comm
1.4 Software
Software for the analyzer consists of 2 programs:
1. A program hidden to the user and integrated in the CPU electronics, running the micro
controller on the CPU card. The program performs all necessary calculations and self monitoring tasks.
2. A Windows based program running on a standard PC connected through the RS-232
connection. The program enables communication with the instrument during installa tion, service and calibration.
The operator will need to use the PC based program only during installation and calibration
and not during normal operation of the instrument. See Section 4 for more details.
1.5 Laser classification and warnings
The diode lasers used in the analyzer operate in the near infrared (NIR) range between 700
and 2400 nm depending on the gas to be measured.
Laser Class 1M for sample component O2
Laser Class 1 for all other sample components
according to IEC 60825-1.
NOTE: The lasers emit invisible light!
WARNING: Class 1M Laser Product – Do not open when energized! Do not view directly with
optical instruments!
WARNING: Class 1 Laser Product – Do not open when energized!
2 Preparations
2.1 Tools and other equipment
The following equipment is necessary to install and calibrate the equipment:
2 pcs open-end spanners for M16 bolts
1 pcs Allen key 5 mm for the locking screws on flanges
1 pcs PC (386 or higher). Used during installation and calibration
1 pcs flat screwdriver 2.5 mm for electrical connections
2.2 Flow conditions at measuring point
When deciding the placement of the analyzer in the process, we recommend a minimum of 5
stack diameters of straight duct before and 2 stack diameters of straight duct after the
point of measure.
2.3 Monitor placement
Both the transmitter and receiver units should be easily accessible. A person should be able
to stand in front of either the transmitter unit or the receiver unit and adjust the M16 fixing
bolts using two standard spanners. For the receiver unit there should be at least 1 m free
space measured from the flange fixed to the stack and outwards as shown in Figure 2-1.