ABB 3BHE039770R0102 PPD539 Contr. Devic
To ensure the best possible accessibility and
continuous trouble-free operation, we provide
cost-efficient spare parts and services for your
system.
ABB offers a comprehensive range of spare parts
with short lead times, which helps minimize
downtime if a failure occurs. In addition, preventive
maintenance kits make it possible to plan
maintenance in advance. This maximizes availability
and increases maintenance performance.
Our LifeCycle Parts Services portfolio meets
customers’ needs to minimize costs and maximize
the value of their investments in ABB equipment.
Whether you need to repair a broken part or
purchase a spare part, our services achieve
cost-efficient maintenance.
ABB is highly qualified and provides a wide range
of technical knowledge and support. We ensure
that our customers receive the best possible return
on their assets throughout the entire product life
cycle.
Product portfolio
ABB’s control systems portfolio ranges from
stand-alone products to Distributed Control
Systems (DCS).
We also supply any size of application, from small
systems to SIL3-certified Safety Instrumented
Systems and Collaborative Process Automation
Systems (CPAS) for an extended automation scope.
The services highlighted in this brochure cover the
following ABB Control Technologies families:
• System 800xA
• Freelance
• Advant Master
• Advant OCS with MOD 300 Software
• Satt
• Symphony DCI System Six
• Symphony Harmony/INFI 90
• Symphony Melody
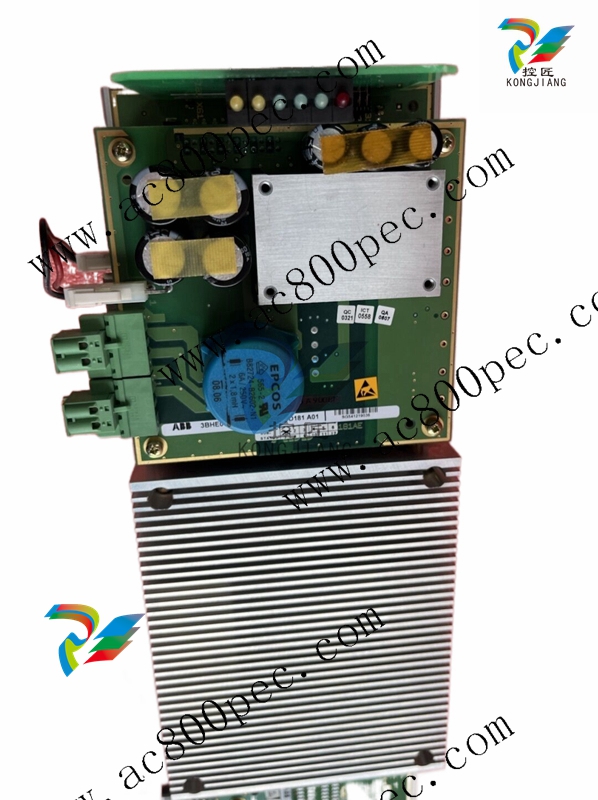
The life cycle management model divides a product's
life cycle into four phases: active, classic, limited
and obsolete. Each phase has different implications for the end user in terms of services and
support provided.
All control systems effectively remain in Active
phase, with individual component products
(hardware and software) transitioning through
the lifecycle phases of Active, Classic, Limited and
Obsolete as they are superseded by newer technologies and offerings.
Spare Parts availability is secured in the phases –
Active, Classic and Limited. New Spare Parts are
actively manufactured in the Active and Classic
phases. In the Limited phase, stocked parts can
be complemented with other Spare Parts Services, such as the Parts Repair Service and the
Parts Refurbishment Service.
Spare Parts are supported for a period of 10 years
from time when the product enters the Classic
phase. When the product reaches the Obsolete
phase the spare parts availability can no longer
be guaranteed. However, the Service organization
may still be able to support the product, or parts
of it, on a best effort basis, limited to available
parts and component inventory.
—
We ensure that our customers
receive the best possible return
on their assets throughout the
entire product life cycle.
Extended Life Cycle Support
Upon individual customer request, ABB can offer
Extended Life Cycle Support agreements to meet
individual customer needs for Spare Parts Services
beyond the standard product lifecycle commitment.
The Extended Lifecycle Support agreements can
include Parts, Parts Repair Services and
Refurbished Parts Services during the product
Life Cycle.
In each life cycle phase, ABB commits to supply,
support and service delivered products to meet
customer expectations throughout the product
lifetime.
ABB offers quick and easily-accessible web-based
information and order systems to facilitate spare
part management. A comprehensive range of
products are available with more than 100,000
spare parts and related Life Cycle Parts Services
for a wide assortment of equipment.
Through your web browser you can access key
information, e.g. specific spare part availability,
locate the equipment that utilizes the particular
spare part, and view technical details and photographs of most spare parts. You can make inquiries,
search for a spare part or place an order at your
convenience 24 hours a day.
Parts are arranged in a hierarchical structure that
spans the entire product range – from equipment
level to a single spare part. Searching for a part is
simple: just enter its type, article number or
description.
In most cases, you can also verify your choice
by viewing a photograph of the part in question.
In addition, several sort and search functions
simplify the information management for you.
To get access, please contact your local ABB office.
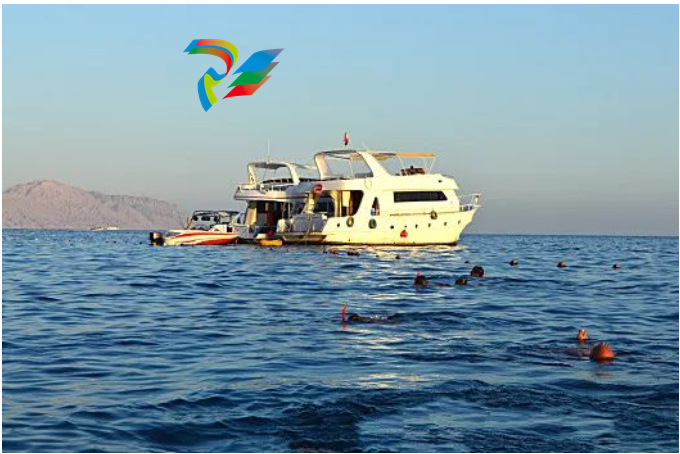
The myABB/ My Control System
customer self-service tool, available 24/7, offers
you a single point of online access to information,
services and service contacts for the ABB family
of control systems and all ABB products.
You’ll quickly find that new MyABB/ My Control
System web portal is a great way to increase your
productivity, minimize cost, and extend the useful
life of your ABB control products and systems.
My Control System is a valuable source for maintenance information and for enhancement of the
control system and provides ready answers to
frequently asked questions, thus reducing the
effort spent looking for information and shortening
software delivery times. All relevant ABB control
system information is in one place and just a
couple of mouse clicks away. A basic version of
My Control System (limited access) will be
provided to all ABB customers.
Automation Sentinel subscribers will enjoy
premium access, which includes features such as
software downloads, access to validated security
updates and documentation already filtered for
each system.
Automation Sentinel
Automation Sentinel is ABB’s subscription based
control system lifecycle management and support
program that assists system owners to actively
manage their control system lifecycle, support
and maintenance.
With this program, system owners can keep their
control software up-to-date and maintain a flexible
path forward to new system software technology.
Automation Sentinel provides exclusive services
for the maintenance, evolution and continual
enhancement of the installed base of ABB control
systems.
System LifeCycle Fingerprint Report
System Lifecycle Fingerprint, available for ABB
control system customers with an myABB/My
Control System account together with a Fingerprint license, provides a comprehensive strategic
maintenance analysis of the installed ABB control
system hardware. It extends the service of System
Lifecycle Benchmark, with the benefit of providing
the full scope of analysis and recommendations
for taking actions.
Based on computer aided data collection from
the installed ABB control system, an analysis and
evaluation is performed by an ABB Field Service
engineer. As a result, a System Fingerprint report
is then presented by ABB Field Service authorities.
Based on the life-cycle status of the individual
installed units and ABB Field Service Engineer's
experience with the customer plant, an evaluation
will be conducted leading to a strategic hardware
maintenance plan.
In addition to the current lifecycle status of the
installed devices, the System Lifecycle Fingerprint
report provides an easy to read table summary of
the forecast lifecycle for the installed devices, and
briefly summarizes key findings and recommended
actions, helping to avoid unwelcome failures and
production losses.