ABB Freelance AC800F
AC 800F opens up the flexibility of Fieldbus
technology to the user. The AC 800F collects
and processes diagnostic and process data
from four Fieldbus lines, which may be of different types. It does this in addition to the
tasks of a “conventional” process station.
The AC 800F is available in two versions:
• 4 MB static RAM, 4 MB EPROM
• 16 MB synchronous dynamic RAM,
8 MB EPROM
Up to 4 (different) fieldbus modules can be
plugged into the AC 800F. The communication
with other controllers runs via Ethernet.
The AC 800F optionally provides several levels
of redundancy:
• device redundancy with 2 AC 800F
• power supply redundancy (24 V DC)
• Ethernet communication redundancy
(standard)
• Cable redundancy for Profibus DP,
requires external equipment (RLM01)
The data protection is made via battery back-up
by Ethernet or battery modules with appropriate
functionality.
• Process Station with integrated fieldbus
capability
• 4 high-speed fieldbus lines
• Supports different fieldbus types, even
simultaneously:
PROFIBUS-DP, up to 12 MBd
Modbus
CAN
Foundation Fieldbus H1 (with LD800
HSE)
• Easy engineering:
fully integrated in Control Builder F
• One unified database for field devices
shared by the control level and the Human
System Interface (HSI)
• Module recognition with factory and operational parameters
• Comprehensive diagnostics for proactive
maintenance
• Compact, rugged design
• Front panel connectors
• DIN Rail (C-rail) or wall mounting for easy
installation
• Ambient temperature 0-60 °C (32-140 °F)
with temperature monitoring
• EMC certification according to EN50082
• Certification:
CE, NAMUR, CSA, UL, EN61000-6-2.
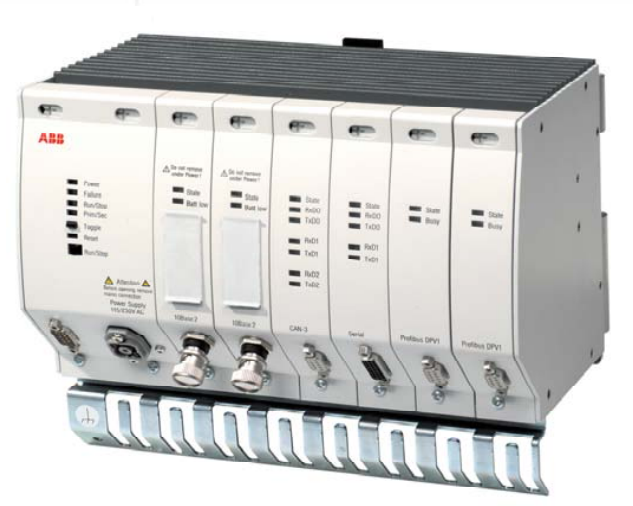
AC 800F Controller Redundancy
Controller redundancy can be achieved by installing two
AC 800F. To ensure quick and smooth takeover by the secon dary AC 800F in case the primary AC 800F fails, a dedicated
redundancy communications link through the second Ethernet
module makes sure that both AC 800F are always synchro nized. All inputs and outputs are designed to support redundant
operation.
Profibus Line Redundancy
Using the Redundancy Link Module RLM 01 will do the conver sion of one simple, non-redundant Profibus line into two recip rocally redundant lines.
You can position the Redundancy Link Module RLM 01 directly
after a Profibus module (master), before a bus segment with
several slaves or before an individual slave. PROFIBUS sta tions with redundant couplers can be directly connected to the
PROFIBUS set redundant by RLM 01. Stations with only one in terface can be optionally assigned to the one or other line.
For technical description dates of the Redundancy Link Module
RLM 01 see document 3BDD011600R0201.
An alternative solution to the Profibus line redundancy is to use
a Fiber Optic Ring, for example with the OZD Profi 12M module
from firm Hirschmann
AC800F Redundancy together with Profibus Line Re dundancy
You can achieve both; controller redundancy and Profibus line
redundancy by using two AC 800F with one RLM01 each. This
topology combines the advantages of controller redundancy
with the one of line redundancy as described in the above
paragraphs.
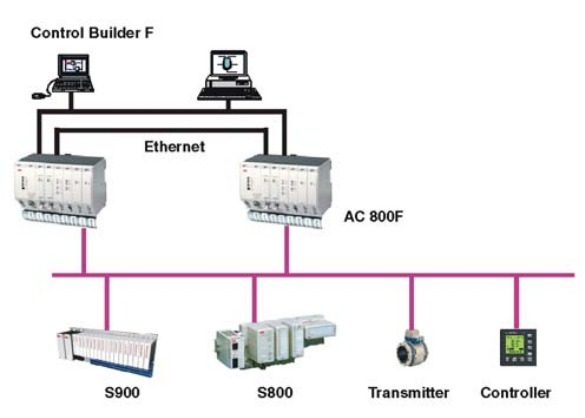
SA 801F 115/230 V AC yes yes max. 3 Profibus modules FI 830F are supported
SD 802F 24 V DC yes yes max. 3 Profibus modules FI 830F are supported
EI 801F 10Base2 yes yes yes, without battery buffering
EI 802F AUI yes yes yes, without battery buffering
EI 803F 10BaseT yes yes yes, without battery buffering
FI 810F CAN-3 yes yes yes
FI 820F Serial yes yes yes
FI 830F Profibus yes yes yes
AM 801F Battery Backup yes yes no
SA 811F 115/230 V AC no yes yes
SD 812F 24 V DC no yes yes
EI 811F 10Base2 no yes yes *
EI 812F AUI no yes yes *
EI 813F 10BaseT no yes yes *
FI 840F FF/HSE no yes yes
AM 811F Battery Backup no yes yes *
Features
Page 4 June 2006
Super Scalar RISC microprocessor (up to 150 MIPS)
16 K internal CPU cache RAM
RAM memory with error detection and correction
PM 802F: 4 MB static
PM 803F: 16 MB synchronous dynamic
Flash-EPROM
PM 802F: 4 MB, 32-bit words
PM 803F: 8 MB, 32- bit words
EEPROM, serial, 16 Kbit
Monitoring of the temperature inside the device
Watchdog
4 slots for fieldbus modules
2 slots for Ethernet communications modules, 32-bit data
bus, 100 MBytes/s
Battery backup incl. battery watchdog
Description
The basic unit, PM 802F and respectively PM803F, cyclically
scans signals from the fieldbus sensors via the corresponding
fieldbus modules, processes these signals according the application programs installed by the user and sends appropriate
signals to the fieldbus actuators via the fieldbus modules.
Controller redundancy can be achieved by installing two
AC 800F. To ensure quick and smooth takeover by the secondary AC 800F in case the primary AC 800F fails, a dedicated
redundancy communications link through the second Ethernet
module makes sure that both AC 800F are always synchronized. All inputs and outputs are designed to support redundant
operation.
Data communication between AC 800F, process and operator
stations runs over the Ethernet system bus on the first Ethernet
module. Data exchange with the engineering station is also carried via the system bus. Engineering station communications
can involve new or updated configuration files being
downloaded to the process stations, or information about the
connected modules being reported back. When fieldbus modules are installed or exchanged, the required configuration information is automatically updated.
Configuration and real-time process data is stored in RAM. To
safeguard this data in case of power loss, the RAM power is
backed up with batteries located either on the Ethernet modules
or on battery modules.
The PM 803F has more memory than the PM 802F and is
therefor capable to handle larger projects. Due to increased
memory size and different technology the buffering times were
reduced.
202
239 164
152
E1 E2 F1 F3 F2 F4 Slot P
Technical Data
CPU Intel 80960HT25/75
32-bit RISC Super Scalar processor
up to 150 MIPS
RAM PM802F:
4 MB static read/write memory
battery back up
PM 803F
16 Mbytes synchronous dynamic
read/write memory, battery back up
I/O scan cycle time Selectable by configuration. Depends on
the capabilities of the fieldbus module
Processing time for
1000 instructions < 1.0 ms for binary and 16 bit arithmetic
instructions
< 2 ms for fixed point arithmetic instructions
< 1.5 ms for 32 bit arithmetic instructions
Power consumption:
Basic unit only: PM 802F PM 803F
max. 6.3 W max. 7.8 W
depending on CPU usage and cycle time
Power supply PM 802F PM 803F
115 - 230 V AC SA 801F SA 811F
2 x 24 V DC SD 802F SD 812F
Max. power output see power supply modules
Weight 1.6 kg
max. 5 kg (fully assembled)
Dimensions Width 239 mm, 9.4 inches
Height 202 mm, 8 inches
Depth 164 mm, 6.5 inches