GE RS-FS-9001 FLAME TRACKER
3 INSTALLATION
3.1 MECHANICAL
The maximum operating temperature for the flame sensor is 302 F (150 C). If the peak ambient
temperature at the location of the sensor exceeds this then cooling will be required. There are three methods
available for cooling: Water-cooling, air-cooling with ambient air, and air-cooling with pressurized air.
Water cooling requires the use of a water cooling coil Part Number sp-566, GE Part Number
353B3490G001. The water-cooling coil requires water at a temperature of 50 F to 135 F (10 C to 57 C) at
a flow rate of 1.0 gpm (3.8 lpm) per sensor. When using water-cooling the flame sensor can be operated to
an ambient temperature of (455F) 235C.
Air-cooling with ambient air can be used in installations where the enclosure is cooled with forced air. This
would be typical of LM2500 and LM6000 aircraft engine applications. The air velocity at the sensor must be 5
ft/sec (1.5 m/sec), or greater, at a temperature of 50 F (10 C), or less, above outside ambient. Under these
conditions the sensors will operate at outside ambient temperatures up to 140 F (60 C).
Air-cooling with pressurized air requires the use of Air-Cooling Can. GE Reuter-Stokes Part Number RS-E2-
0259 (GE Part Number 07482SOCNL44821P01). The Air-Cooing Can is installed in the same manner as the
water-cooling coil. The Air-Cooling Can requires 25-psi (170 kPa) minimum at 120 F (49 C) maximum.
Do not complete step 2 in the “FLAME SENSOR AND WATER COOLING JACKET INSTALLATION
INSTRUCTIONS” on the next page. Leave the sensors installed hand tight until after the sensor checkout
described in Section 3.3.
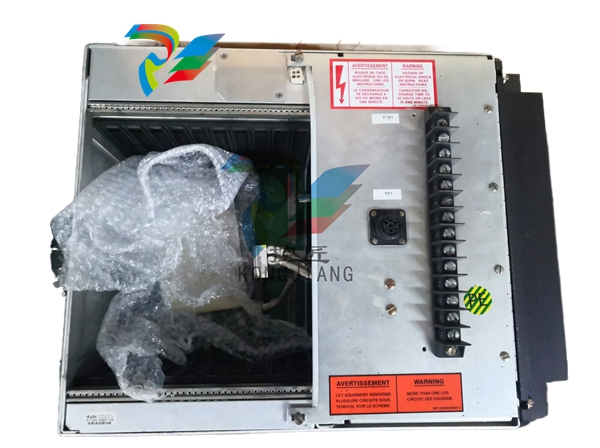
1. Apply a small amount of Never-Seez PN NG-165(GE PN 248A9779P001) to threads, prior
to reinstalling the Flame Sensor
2.Inspect the window and clean with Isopropanol soaked swab. If required install hand tight
(3-4 Full turs) tighten with a wrench approximately 2.5 turns.Tighten further as required to
align keys on cable connector with slots in sensor connector
3. Slide cooling coil over Flame Sensor major diameter and orient tubes on the coil as required
for assembly. Tighten clamps 50-60 in. lbs.Install Swagelok fittings re-torque damps to 50-
60 in. lbs. after first shut down
Note:50-60 in.lbs=5.6 - 6.8 Nm.When installing the Water Cooling Coil,ensure that the edge of the
Sheet Metal Band is not in contact with the cooling tubes. This will ensure that no rubbing or fretting of the
cooling tubes by the band's edge will occur during turbine operation.
The Flame Tracker™ is connected to the controller as a typical two wire current transmitter. It can be
operated from any well-filtered dc supply from 12 volts to 30 volts. The supply should be capable of supplying
100 milliamps.
The power supply must be protected to prevent the supply voltage from exceeding 30 volts in normal use
and more than 42 volts under transient conditions. The sensor is protected against reverse polarity. The
maximum value for the sense resistor plus the wire resistance is dependent on the supply voltage. At 24 volts
this value is 560 ohms. Resistance values for other voltages can be determined from the chart in Figure 2.
Figure 1 shows the preferred wiring for the sensor with the Rsense of the controller in the return line of the
sensor. This configuration can be used with controllers that have single ended inputs (one side of the input
grounded) or differential inputs (neither side of the input grounded). For pin outs and cable color code see
Figure 1.
3.3 CONNECTOR PINOUT
The pinout for the power connector is as follows:
CONNECTOR LEGEND
PIN CIRCUIT DESIGNATIONA -B +
C Ground
D Not Used
E Not Used
3.4 SENSOR CHECKOUT
Disconnect the sensors and unscrew them from the turbine. Plug the sensor cables back in to each of the
sensors. Apply power to the sensors. Check the current values at the controller for each of the sensors. The
sensors are sensitive to light, and may have some reading, depending on the ambient light level. Test each
sensor by covering the port to see the zero flame intensity signals, and with a flashlight to see a positive
reading. With no light the reading should be 3.7 to 4.1 milliamps, while with most flashlights the reading should
be above 8 milliamps. An LED flashlight may not work for this application. Variations in flashlight type,
strength, or battery voltage may cause variation in signal output. The flashlight test is intended as a field test
for general functionality only and is not a controlled or quantitative test. If a sensor is outside these rough
check limits see Section 5.0.
Disconnect the sensor cables, and reinstall the sensors according to the instruction in Section 3.1. At this
time step 2 of Section 3.1 should be completed and the sensor cables reconnected. Make sure that the
sapphire window is clean; if it needs cleaning, do this according to the maintenance instructions in Section 4.0.
Check that all sensors are reading between 3.7 to 4.1 milliamps.
3.5 CONTROLLER SETUP
The Flame Sensor provides a minimum output of 5 milliamps when exposed to the minimum flame intensity
specified in GE specification number 362A1052. The set point for flame off should be set to 6.25%, which
equals 5 milliamps. The set point for flame on should be 10%, which equals 5.6 milliamps. If the intensity
levels are to low for these settings their may be other