ABB ACS6000 3BHS212794E01 SYSTEM DRIVES
Important note - main circuit breaker
The main circuit breaker (MCB) is a major protection device of the drive. If
a serious fault occurs in the drive, the MCB must disconnect the main
power supply to the drive immediately. The main power supply must be
disconnected without delay on an open or trip command from the drive to
prevent hazard to the personnel and further damage to the equipment.
The MCB is located on the primary side of the converter transformer.
Figure 2-2 Drive system overview
Note: MCBs and protection relays are not included in the drive supply.
Typical MCBs devices
• Vacuum circuit breakers
• SF6 circuit breakers
• Fused contactors or motor control centers
Dedicated protection relay
• Transformer or drive primary cable protection (DTL)
• Transformer protection (if applicable)
• Transformer secondary cable protection (if applicable)
• Backing up the drive protection
(1) Main power supply
(2) MCB control interface
(3) Higher-level control system
(4) Local MCB control
(5) MCB
(6) Protection relay
(7) Converter transformer
(8) Drive
(9) Motor
2.7.1 Safety and protection requirements
The system integrator must ensure that the following minimum safety
and protection requirements for the drive are met:
• ISO 13849-1
• IEC 60204-1
2.7.2 Safety and protection requirements for the MCB
The following safety requirements are also in the MCB specifications for
the drive:
• MCB open and/or trip command: must be wired directly from the
drive to the MCB. If you want to wire the command through a PLC or
DCS system, the system must be certified to meet SIL three-level
requirements and to fulfill the maximum MCB opening timing
requirements. The drive must also be able to open the MCB at any
time. It is not permitted to interrupt the open and/or trip
command, eg, with a local-remote switch in the MCB.
• Closing control of the MCB: when the MCB is in service position, the
drive must have exclusive control over closing the MCB, ie, local
closing of the MCB is not permitted.
• MCB maximum opening time: cannot exceed the maximum time that
is defined in the product or project-specific MCB specifications.
Typical maximum values for the drive are defined as follows:
• Maximum protection trip time: 75 ms
The maximum protection trip time is the maximum allowed
breaking time (open and arcing) of the breaking device after the
open command has been initiated to prevent further damage to the
drive, such as diode failures.
• Maximum safety trip time: 500 ms
The maximum safety trip time is the maximum allowed time to
ensure safe disconnection of the main power supply to prevent any
hazard to personnel.
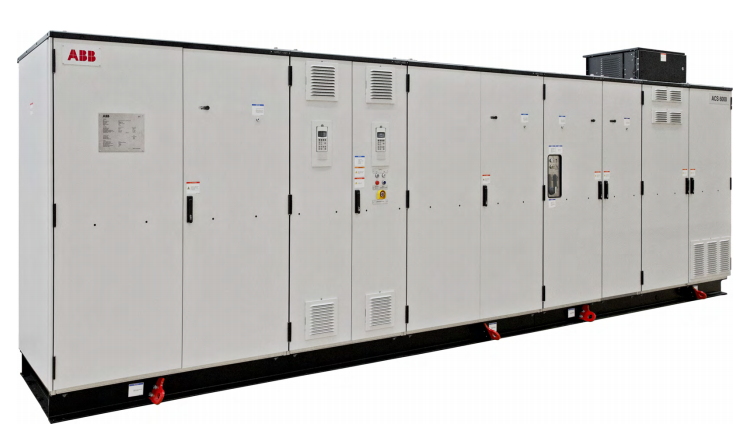
Figure 2-3 MCB opening timing diagram
In order to meet the stipulated safety requirements, ABB recommends one
of the following:
• MCB is equipped with 2 independent opening coils
• MCB is equipped with an opening coil and an undervoltage coil for
monitoring of the control voltage
• Upstream protection coordination scheme is provided which uses
the "breaker failure" (ANSI 50BF) signal to automatically trip the
upstream breaker, in case the MCB does not open.
IMPORTANT! The upstream breaker must open within the maximum
safety trip time after a failure has occurred.
2.8 Maintenance recommendation
The MCB trip circuits should be checked annually.
(1) Short-circuit occurs
(2) Open and or trip command is set at the drive control output
(3) No further damage to the drive
(4) No hazard to personnel
(5) Maximum protection trip time
(6) Maximum safety trip time
Power electronics and cabinet features
3.1 Drive system topology
The ACS6000 drive system consists of the following components:
• Main circuit breaker: For more information, see “2.8 Maintenance
recommendation” on page 49.
• Input transformer: Required if the line voltage must be adapted to
the motor voltage. For more information, see the “Main
transformer specification”.
• Drive
• Motor
3.1.1 Drive
The ACS6000 is a voltage source frequency converter for high-power
induction and synchronous motors. The drive features a common DC bus
permitting the configuration of single-motor or multi-motor solutions.
Figure 3-1 Common DC-bus principle for single motor drive (A) and multimotor drive (B)
The ACS6000 has a flexible modular design with standard and optional
cabinet units. Each cabinet unit is dedicated to a specific function.
Figure 3-2 ACS6000 drive example
The drive is assembled from standard and optional cabinet units. Each
unit is dedicated to a specific function.
Note: For more information on the cabinet units in your drive, see the
Layout drawing in “Appendix C – Mechanical drawings”.
(1) Active rectifier unit (ARU):
Self-commutated, 6-pulse, 3-level
voltage source inverter with
IGCT technology
(2) Drive control panel for local
operation: Keypad with multi language display, main supply on/
off pushbuttons, and emergency
off push button
(3) Inverter unit (INU):
Self-commutated, 6-pulse, 3-level
voltage source inverter with
IGCT technology
(4) Capacitor bank unit (CBU):
DC capacitors for smoothing the
intermediate DC voltage
(5) Water cooling unit (WCU):
Supplies deionized water for
cooling the main
power components
(6) Terminal unit (TEU) and control
unit (COU): Contains the power
terminals and the control
swing frame
(7) Braking chopper unit (BCU),
resistor braking unit (RBU) or
voltage limiter unit (VLU):
Optional cabinet units
(8) Excitation unit (EXU):
Optional cabinet unit that supplies
a synchronous motor
with excitation
ACS6000 cabinet units
3.1.1.2 Final drive configuration
The final drive configuration depends on the following factors:
• Required output power
• Configuration of the main power supply (input transformer or
direct-to-line connection)
• Ability to recover energy (active or diode front end)
• Motor type (synchronous or asynchronous)
• Single or multi-motor application.
3.1.2 Motor
See the “Motor specification”.
3.2 Standard cabinet units
The following sections describe the ARU, INU, LSU, CBU, TEU, COU and
WCU cabinets.
3.2.1 Active rectifier unit (ARU)/inverter unit (INU)
An ARU and INU have the same mechanical and electrical designs.
• ARU: The ARU is a 6-pulse self-commutated voltage source inverter
that rectifies the line voltage of the supply network and maintains
the DC-link voltage at a constant level irrespective of changes in the
supply network.
The active 6-pulse rectifier allows for regenerative braking.
• INU: The INU controls the 3-phase motor voltage and converts the
DC-link voltage to the required AC motor voltage and frequency.
The INU is a self-commutated voltage source inverter in 6-pulse, 3-
level topology. To increase the drive power, 4 units can be operated
in parallel on 1 motor.
Standard cabinet units Optional cabinet units
• Active rectifier unit (ARU)
• Inverter unit (INU)
• Line supply unit (LSU)
• Capacitor bank unit (CBU)
• Terminal unit (TEU)
• Control unit (COU)
• Water cooling unit (WCU)
• Input reactor unit (IRU)
• Input filter unit (IFU)
• Voltage limiter unit (VLU)
• Braking units:
- Resistor braking unit (RBU)
- Braking chopper unit (BCU)
• Excitation unit (EXU)
• Customer interface unit (CIU)